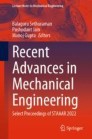
International Conference on Sustainable Technologies and Advances in Automation, Aerospace and Robotics
STAAAR 2022: Recent Advances in Mechanical Engineering pp 295–302 Cite as

Design and Analysis of Morphed Wings
- Abhishek Thakur 13 ,
- Arockia Selvakumar Arockia Doss ORCID: orcid.org/0000-0002-7810-6994 13 &
- Daniel Schilberg 14
- Conference paper
- First Online: 21 July 2023
142 Accesses
Part of the book series: Lecture Notes in Mechanical Engineering ((LNME))
A flying machine either uses a flapping mechanism, a fixed wing or a rotating blade in order to produce lift. While considering fixed wing aircraft or a drone, in order to produce a lift or a decent, the major contributing part is the aileron. An aileron area with respect to the wing is nearly 15%. Rather a discreet movement of aileron, the wing surface can be morphed in order to produce an effect similar to aileron. This research is done to compare and analyze a morphed wing with an aileron-based wing in order to produce the lift and identify maneuvering effects for a drone. Continuous lift force distribution throughout the wing is observed over a range of different wind speeds, and the results are found to be satisfactory.
- Maneuverability
This is a preview of subscription content, log in via an institution .
Buying options
- Available as PDF
- Read on any device
- Instant download
- Own it forever
- Available as EPUB and PDF
- Compact, lightweight edition
- Dispatched in 3 to 5 business days
- Free shipping worldwide - see info
Tax calculation will be finalised at checkout
Purchases are for personal use only
Babinsky H (2003) How do wings work? www.iop.org/journals/physed
Sofla AYN, Meguid SA, Tan KT, Yeo WK (2010) Shape morphing of aircraft wing: status and challenges. Mater Des 31(3):1284–1292
Article Google Scholar
Budarapu PR, Sudhir Sastry YB, Natarajan R (2016) Design concepts of an aircraft wing: composite and morphing airfoil with auxetic structures. Front Struct Civ Eng 10(4):394–408. https://doi.org/10.1007/s11709-016-0352-z
Li D, Zhao S, Ronch AD, Xiang J, Drofelnik J, Li Y, Zhang L, Wu Y, Kintscher M, Monner HP, Rudenko A, Guo S, Yin W, Kirn J, Storm S, De Breuker R (2018) A review of modelling and analysis of morphing wings. Progr Aerosp Sci 100:46–62. ISSN 0376-0421. https://doi.org/10.1016/j.paerosci.2018.06.002
Ajaj RM, Parancheerivilakkathil MS, Amoozgar M, Friswell MI, Cantwell WJ (2021) Recent developments in the aeroelasticity of morphing aircraft. Prog Aerosp Sci 120. https://doi.org/10.1016/j.paerosci.2020.100682
Muhammed SP, Ajaj RM, Khan KA (2020) A compliant polymorphing wing for small UAVs. Chin J Aeronaut 33(10):2575–2588
Woods BK, Bilgen O, Friswell MI (2014) Wind tunnel testing of the fish bone active camber morphing concept. J Intell Mater Syst Struct 25(7):772–785
Hasse A, Zuest I, Campanile LF (2011) Modal synthesis of belt-rib structures. Proc Inst Mech Eng Part C J Mech Eng Sci 225(3):722–732
Google Scholar
Berci M, Toropov VV, Hewson RW, Gaskell PH (2014) Multidisciplinary multifidelity optimisation of a flexible wing aerofoil with reference to a small UAV. Struct Multidiscip Optim 50(4):683–699
Airoldi A, Crespi M, Quaranta G, Sala G (2012) Design of a morphing airfoil with composite chiral structure. J Aircr 49(4):1008–1019
Li D, Zhao S, da Ronch A et al (2018) A review of modelling and analysis of morphing wings. Prog Aerosp Sci 100:46–62
Communier D, Botez RM, Wong T (2020) Design and validation of a new morphing camber system by testing in the price—Païdoussis subsonic wind tunnel. Aerospace 7(3):23
Meguid S, Su Y, Wang Y (2017) Complete morphing wing design using flexible-rib system. Int J Mech Mater Des 13(1):159–171
Chanzy Q, Keane A (2018) Analysis and experimental validation of morphing UAV wings. Aeronaut J 122(1249):390–408
Kudva JN, Martin CA, Scherer LB et al (1999) Overview of the DARPA/AFRL/NASA smart wing program. In: Smart structures and materials 1999 industrial and commercial applications of smart structures technologies. International Society for Optics and Photonics, pp 230–236
Lobo do Vale J, Raffaelli J, Suleman A (2021) Experimental validation and evaluation of a coupled twist-camber morphing wing concept. Appl Sci 11:10631. https://doi.org/10.3390/app112210631
Cody L, Kelly C, Shaaban A (2012) Use of XFOIL in design of camber-controlled morphing UAVs. Comput Appl Eng Educ 20:673–680
Critzos CC, Heyson HH, Boswinkle Jr RW (1955) Aerodynamic characteristics of NACA 0012 airfoil section at angles of attack from 0 degrees to 180 degrees (No. NACA-TN-3361)
Ryaciotaki-Boussalis H, Guillaume D (2015) Computational and experimental design of a fixed-wing UAV. In: Valavanis K, Vachtsevanos G (eds) Handbook of unmanned aerial vehicles. Springer, Dordrecht. https://doi.org/10.1007/978-90-481-9707-1_121
Rao D (2020) Design and analysis of fixed-wing UAV. The print has aerodynamic, structural and stability analysis of a Fixed-Wing UAV
Ghalandari M, Mahariq I, Ghadak F, Accouche O, Jarad F (2021) Aeroelastic optimization of the high aspect ratio wing with aileron. Comput Mater Continua 70. https://doi.org/10.32604/cmc.2022.020884
Wu SF, Grimble MJ, Breslin SG (1997) Quantitative feedback theory for lateral robust flight control systems design. 4. TITLE AND SUBTITLE, 235
Download references
Author information
Authors and affiliations.
Vellore Institute of Technology, Chennai, Tamil Nadu, India
Abhishek Thakur & Arockia Selvakumar Arockia Doss
Bochum University of Applied Sciences, Bochum, Germany
Daniel Schilberg
You can also search for this author in PubMed Google Scholar
Corresponding author
Correspondence to Arockia Selvakumar Arockia Doss .
Editor information
Editors and affiliations.
School of Mechanical Engineering, VIT Bhopal University, Bhopal, Madhya Pradesh, India
Balaguru Sethuraman
Pushpdant Jain
Department of Mechanical Engineering, National University of Singapore, Singapore, Singapore
Manoj Gupta
Rights and permissions
Reprints and permissions
Copyright information
© 2023 The Author(s), under exclusive license to Springer Nature Singapore Pte Ltd.
About this paper
Cite this paper.
Thakur, A., Doss, A.S.A., Schilberg, D. (2023). Design and Analysis of Morphed Wings. In: Sethuraman, B., Jain, P., Gupta, M. (eds) Recent Advances in Mechanical Engineering. STAAAR 2022. Lecture Notes in Mechanical Engineering. Springer, Singapore. https://doi.org/10.1007/978-981-99-2349-6_27
Download citation
DOI : https://doi.org/10.1007/978-981-99-2349-6_27
Published : 21 July 2023
Publisher Name : Springer, Singapore
Print ISBN : 978-981-99-2348-9
Online ISBN : 978-981-99-2349-6
eBook Packages : Engineering Engineering (R0)
Share this paper
Anyone you share the following link with will be able to read this content:
Sorry, a shareable link is not currently available for this article.
Provided by the Springer Nature SharedIt content-sharing initiative
- Publish with us
Policies and ethics
- Find a journal
- Track your research
Suggestions or feedback?
MIT News | Massachusetts Institute of Technology
- Machine learning
- Social justice
- Black holes
- Classes and programs
Departments
- Aeronautics and Astronautics
- Brain and Cognitive Sciences
- Architecture
- Political Science
- Mechanical Engineering
Centers, Labs, & Programs
- Abdul Latif Jameel Poverty Action Lab (J-PAL)
- Picower Institute for Learning and Memory
- Lincoln Laboratory
- School of Architecture + Planning
- School of Engineering
- School of Humanities, Arts, and Social Sciences
- Sloan School of Management
- School of Science
- MIT Schwarzman College of Computing
A new twist on airplane wing design
Press contact :, media download.
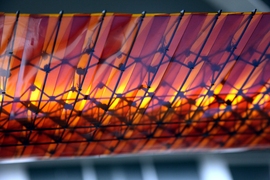
*Terms of Use:
Images for download on the MIT News office website are made available to non-commercial entities, press and the general public under a Creative Commons Attribution Non-Commercial No Derivatives license . You may not alter the images provided, other than to crop them to size. A credit line must be used when reproducing images; if one is not provided below, credit the images to "MIT."

Previous image Next image
When the Wright brothers accomplished their first powered flight more than a century ago, they controlled the motion of their Flyer 1 aircraft using wires and pulleys that bent and twisted the wood-and-canvas wings. This system was quite different than the separate, hinged flaps and ailerons that have performed those functions on most aircraft ever since. But now, thanks to some high-tech wizardry developed by engineers at MIT and NASA, some aircraft may be returning to their roots, with a new kind of bendable, “morphing” wing.
The new wing architecture, which could greatly simplify the manufacturing process and reduce fuel consumption by improving the wing’s aerodynamics, as well as improving its agility, is based on a system of tiny, lightweight subunits that could be assembled by a team of small specialized robots, and ultimately could be used to build the entire airframe. The wing would be covered by a “skin” made of overlapping pieces that might resemble scales or feathers.
The new concept is described in the journal Soft Robotics, in a paper by Neil Gershenfeld, director of MIT’s Center for Bits and Atoms (CBA); Benjamin Jenett, a CBA graduate student; Kenneth Cheung PhD ’12, a CBA alumnus and NASA research scientist; and four others.
A test version of the deformable wing designed by the MIT and NASA researchers is shown undergoing its twisting motions, which could replace the need for separate, hinged panels for controlling a plane's motion. (Kenneth Cheung/NASA)
Researchers have been trying for many years to achieve a reliable way of deforming wings as a substitute for the conventional, separate, moving surfaces, but all those efforts “have had little practical impact,” Gershenfeld says. The biggest problem was that most of these attempts relied on deforming the wing through the use of mechanical control structures within the wing, but these structures tended to be so heavy that they canceled out any efficiency advantages produced by the smoother aerodynamic surfaces. They also added complexity and reliability issues.
By contrast, Gershenfeld says, “We make the whole wing the mechanism. It’s not something we put into the wing.” In the team’s new approach, the whole shape of the wing can be changed, and twisted uniformly along its length, by activating two small motors that apply a twisting pressure to each wingtip.
This approach to the manufacture of aircraft, and potentially other technologies, is such a new idea that “I think we can say it is a philosophical revolution, opening the gate to disruptive innovation,” says Vincent Loubiere, a lead technologist for emerging technologies and concepts at Airbus, who was not directly involved in this research. He adds that “the perspectives and fields this approach opens are thrilling.”
Like building with blocks
The basic principle behind the new concept is the use of an array of tiny, lightweight structural pieces, which Gershenfeld calls “digital materials,” that can be assembled into a virtually infinite variety of shapes, much like assembling a structure from Lego blocks. The assembly, performed by hand for this initial experiment, could be done by simple miniature robots that would crawl along or inside the structure as it took shape. The team has already developed prototypes of such robots.
The individual pieces are strong and stiff, but the exact choice of the dimensions and materials used for the pieces, and the geometry of how they are assembled, allow for a precise tuning of the flexibility of the final shape. For the initial test structure, the goal was to allow the wing to twist in a precise way that would substitute for the motion of separate structural pieces (such as the small ailerons at the trailing edges of conventional wings), while providing a single, smooth aerodynamic surface.
Building up a large and complex structure from an array of small, identical building blocks, which have an exceptional combination of strength, light weight, and flexibility, greatly simplifies the manufacturing process, Gershenfeld explains. While the construction of light composite wings for today’s aircraft requires large, specialized equipment for layering and hardening the material, the new modular structures could be rapidly manufactured in mass quantities and then assembled robotically in place.
Side perspective of the test wing at Langley Research Center’s 12-Foot Low Speed Tunnel. (Kenneth Cheung/NASA)
Gershenfeld and his team have been pursuing this approach to building complex structures for years, with many potential applications for robotic devices of various kinds. For example, this method could lead to robotic arms and legs whose shapes could bend continuously along their entire length, rather than just having a fixed number of joints.
This research, says Cheung, “presents a general strategy for increasing the performance of highly compliant — that is, ‘soft’ — robots and mechanisms,” by replacing conventional flexible materials with new cellular materials “that are much lower weight, more tunable, and can be made to dissipate energy at much lower rates” while having equivalent stiffness.
Saving fuel, cutting emissions
While exploring possible applications of this nascent technology, Gershenfeld and his team consulted with NASA engineers and others seeking ways to improve the efficiency of aircraft manufacturing and flight. They learned that “the idea that you could continuously deform a wing shape to do pure lift and roll has been a holy grail in the field, for both efficiency and agility,” he says. Given the importance of fuel costs in both the economics of the airline industry and that sector’s contribution to greenhouse gas emissions, even small improvements in fuel efficiency could have a significant impact.
Wind-tunnel tests of this structure showed that it at least matches the aerodynamic properties of a conventional wing, at about one-tenth the weight.
The “skin” of the wing also enhances the structure’s performance. It’s made from overlapping strips of flexible material, layered somewhat like feathers or fish scales, allowing for the pieces to move across each other as the wing flexes, while still providing a smooth outer surface.
The modular structure also provides greater ease of both assembly and disassembly: One of this system’s big advantages, in principle, Gershenfeld says, is that when it’s no longer needed, the whole structure can be taken apart into its component parts, which can then be reassembled into something completely different. Similarly, repairs could be made by simply replacing an area of damaged subunits.
“An inspection robot could just find where the broken part is and replace it, and keep the aircraft 100 percent healthy at all times,” says Jenett.
Following up on the successful wind tunnel tests, the team is now extending the work to tests of a flyable unpiloted aircraft, and initial tests have shown great promise, Jenett says. “The first tests were done by a certified test pilot, and he found it so responsive that he decided to do some aerobatics.”
Some of the first uses of the technology may be to make small, robotic aircraft — “super-efficient long-range drones,” Gershenfeld says, that could be used in developing countries as a way of delivering medicines to remote areas.
“Ultralight, tunable, aeroelastic structures and flight controls open up whole new frontiers for flight,” says Gonzalo Rey, chief technology officer for Moog Inc., a precision aircraft motion-controls company, who was not directly involved in this work, though he has collaborated with the team. “Digital materials and fabrication are a fundamentally new way to make things and enable the conventionally impossible. The digital morphing wing article demonstrates the ability to resolve in depth the engineering challenges necessary to apply the concept.”
Rey adds that “The broader potential in this concept extends directly to skyscrapers, bridges, and space structures, providing not only improved performance and survivability but also a more sustainable approach by achieving the same strength while using, and reusing, substantially less raw material.”
And Loubiere, from Airbus, suggests that many other technologies could also benefit from this method, including wind turbines: “Simply enabling the assembly of the windmill blades on the spot, instead of using complex and fuel-consuming transport, would enhance greatly the cost and overall performance,” he says.
The research team also included graduate students Sam Calisch at MIT’s Center for Bits and Atoms; Daniel Cellucci at Cornell University; Nick Cramer at the University of California at Santa Cruz; and researcher Sean Swei at NASA’s Ames Research Center in Mountain View, California. The work was supported by the NASA Aeronautics Research Institute Team Seeding Program, the NASA ARMD Convergent Aeronautics Solutions Program, and the NASA Space Technology Research Fellowship program.
Share this news article on:
Press mentions, the wall street journal.
Wall Street Journal reporter Robert Lee Hotz writes that MIT engineers have developed a flexible airplane wing that could improve a plane’s fuel consumption by improving the wing’s aerodynamics. Hotz explains that the wing’s “elastic airfoil can morph continuously to reduce drag, increase stall angle, and reduce vibration control flutter.”
Previous item Next item
Related Links
- Paper: “Digital morphing wing: Active wing shaping concept using composite lattice-based cellular structures.”
- Neil Gershenfeld
- Center for Bits and Atoms
- School of Architecture and Planning

Related Topics
- Aeronautical and astronautical engineering
- Self-assembly
- Energy efficiency
Related Articles
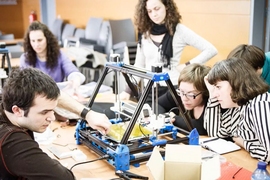
3 Questions: Neil Gershenfeld and the spread of Fab Labs
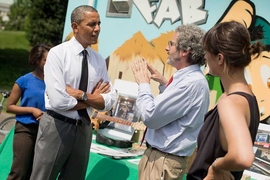
MIT’s Mobile Fab Lab participates in White House Maker Faire
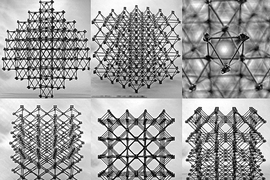
How to make big things out of small pieces
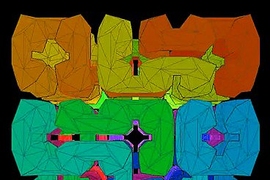
The robotic equivalent of a Swiss army knife
Hope on the horizon: digital fabrication.

Shape-shifting robots
More mit news.
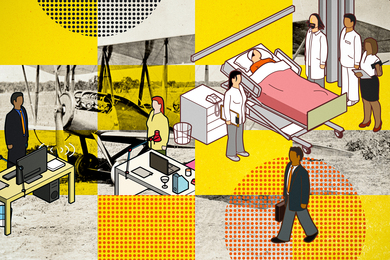
Most work is new work, long-term study of U.S. census data shows
Read full story →
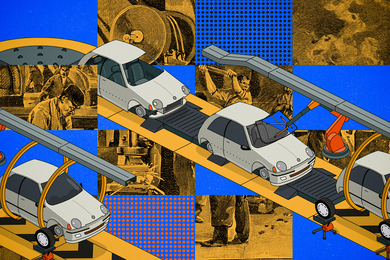
Does technology help or hurt employment?
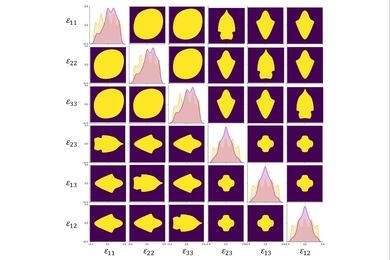
A first-ever complete map for elastic strain engineering
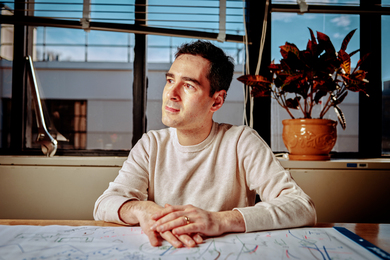
“Life is short, so aim high”
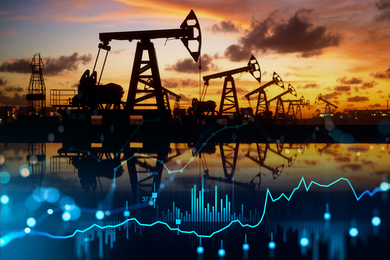
Shining a light on oil fields to make them more sustainable
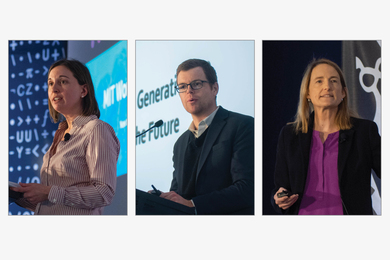
MIT launches Working Group on Generative AI and the Work of the Future
- More news on MIT News homepage →
Massachusetts Institute of Technology 77 Massachusetts Avenue, Cambridge, MA, USA
- Map (opens in new window)
- Events (opens in new window)
- People (opens in new window)
- Careers (opens in new window)
- Accessibility
- Social Media Hub
- MIT on Facebook
- MIT on YouTube
- MIT on Instagram
For New Insights into Aerodynamics, Scientists Turn to Paper Airplanes
A series of experiments using paper airplanes reveals new aerodynamic effects--findings that enhance our understanding of flight stability.
Findings Unveil Mechanisms that Explain Flight Stability
A series of experiments using paper airplanes reveals new aerodynamic effects, a team of scientists has discovered. Its findings enhance our understanding of flight stability and could inspire new types of flying robots and small drones.
“The study started with simple curiosity about what makes a good paper airplane and specifically what is needed for smooth gliding,” explains Leif Ristroph, an associate professor at New York University’s Courant Institute of Mathematical Sciences and an author of the study , which appears in the Journal of Fluid Mechanics . “Answering such basic questions ended up being far from child’s play. We discovered that the aerodynamics of how paper airplanes keep level flight is really very different from the stability of conventional airplanes.”
“Birds glide and soar in an effortless way, and paper airplanes, when tuned properly, can also glide for long distances,” adds author Jane Wang, a professor of engineering and physics at Cornell University. “Surprisingly, there has been no good mathematical model for predicting this seemingly simple but subtle gliding flight.”
Since we can make complicated modern airplanes fly, the researchers say, one might think we know all there is to know about the simplest flying machines.
“But paper airplanes, while simple to make, involve surprisingly complex aerodynamics,” notes Ristroph.
The paper’s authors began their study by considering what is needed for a plane to glide smoothly. Since paper airplanes have no engine and rely on gravity and proper design for their movement, they are good candidates for exploring factors behind flight stability.
To investigate this phenomenon, the researchers conducted lab experiments by launching paper airplanes with differing centers of mass through the air. The results, along with those from studying plates falling in a water tank, allowed the team to devise a new aerodynamic model and also a “flight simulator” capable of predicting the motions.
A video and image showing the experimental results may be downloaded from Google Drive .
To find the best design, the researchers placed different amounts of thin copper tape on the front part of the paper planes, giving them varied center of mass locations. Lead weights added to the plates in water served the same purpose.
“The key criterion of a successful glider is that the center of mass must be in the ‘just right’ place,” Ristroph explains. “Good paper airplanes achieve this with the front edge folded over several times or by an added paper clip, which requires a little trial and error.”
In the experiments, the researchers found that the flight motions depended sensitively on the center of mass location. Specifically, if the weight was at the center of the wing or only displaced somewhat from the middle, it underwent wild motions, such as fluttering or tumbling. If the weight was displaced too far toward one edge, then the flier quickly dove downwards and crashed. In between, however, there was a “sweet spot” for the center of mass that gave stable gliding.
The researchers coupled the experimental work with a mathematical model that served as the basis of a “flight simulator,” a computer program that successfully reproduced the different flight motions. It also helped explain why a paper airplane is stable in its glide. When the center of mass is in the “sweet spot,” the aerodynamic force on the plane’s wing pushes the wing back down if the plane moves upward and back up if it moves downward.
“The location of the aerodynamic force or center of pressure varies with the angle of flight in such a way to ensure stability,” explains Ristroph.
He notes that this dynamic does not occur with conventional aircraft wings, which are airfoils—structures whose shapes work to generate lift.
“The effect we found in paper airplanes does not happen for the traditional airfoils used as aircraft wings, whose center of pressure stays fixed in place across the angles that occur in flight,” Ristroph says. “The shifting of the center of pressure thus seems to be a unique property of thin, flat wings, and this ends up being the secret to the stable flight of paper airplanes.”
“This is why airplanes need a separate tail wing as a stabilizer while a paper plane can get away with just a main wing that gives both lift and stability,” he concludes. “We hope that our findings will be useful in small-scale flight applications, where you may want a minimal design that does not require a lot of extra flight surfaces, sensors, and controllers.”
The paper’s other authors were Huilin Li, a doctoral candidate at NYU Shanghai, and Tristan Goodwill, a doctoral candidate at the Courant Institute’s Department of Mathematics.
The work was supported by grants from the National Science Foundation (DMS-1847955, DMS-1646339).
Press Contact
Academia.edu no longer supports Internet Explorer.
To browse Academia.edu and the wider internet faster and more securely, please take a few seconds to upgrade your browser .
Enter the email address you signed up with and we'll email you a reset link.
- We're Hiring!
- Help Center
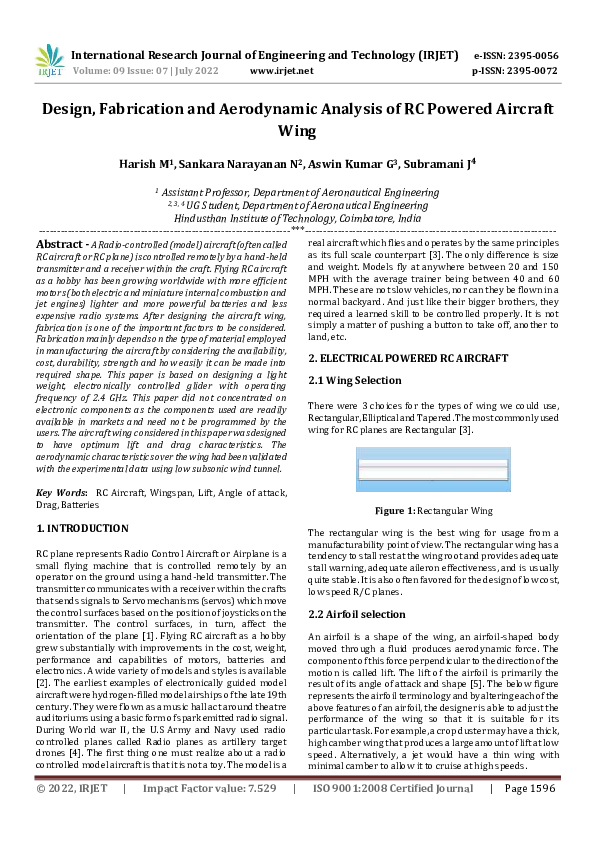
Design, Fabrication and Aerodynamic Analysis of RC Powered Aircraft Wing

2022, IRJET
A Radio-controlled (model) aircraft (often called RC aircraft or RC plane) is controlled remotely by a hand-held transmitter and a receiver within the craft. Flying RC aircraft as a hobby has been growing worldwide with more efficient motors (both electric and miniature internal combustion and jet engines) lighter and more powerful batteries and less expensive radio systems. After designing the aircraft wing, fabrication is one of the important factors to be considered. Fabrication mainly depends on the type of material employed in manufacturing the aircraft by considering the availability, cost, durability, strength and how easily it can be made into required shape. This paper is based on designing a light weight, electronically controlled glider with operating frequency of 2.4 GHz. This paper did not concentrated on electronic components as the components used are readily available in markets and need not be programmed by the users. The aircraft wing considered in this paper was designed to have optimum lift and drag characteristics. The aerodynamic characteristics over the wing had been validated with the experimental data using low subsonic wind tunnel.
RELATED TOPICS
- We're Hiring!
- Help Center
- Find new research papers in:
- Health Sciences
- Earth Sciences
- Cognitive Science
- Mathematics
- Computer Science
- Academia ©2024

IMAGES
VIDEO
COMMENTS
PRELIMINARY AERODYNAMIC WING DESIGN OPTIMISATION FOR WING-IN-GROUND EFFECT AIRCRAFT Rejish Jesudasan1, Raffaello Mariani2 & Ardeshir Hanifi3 1Postdoctoral Research Fellow, School of Engineering Sciences, [email protected] 2Assistant Professor, School of Engineering Sciences, [email protected] 3Researcher, School of Engineering Sciences, KTH Royal Institute of Technology, hanifi@kth.se
The performance of data-based optimization is verified in single-point, multi-point, and multi-objective wing shape design problems. We also show some innovative usage of the data-based optimization method in wing design that conventional optimization cannot handle. The rest of this paper is organized as follows.
This paper presents the multidisciplinary design analysis and optimization process of a blended wing body and its application to a long-haul commercial transport mission. View Show abstract
The folding wing configuration is a strong candidate for morphing wing design that changes the wing area, in turn affecting various aspects of flight such as climb rate, stall characteristics, and lateral stability. ... The first factor is that research should be conducted at the material level, developing and understanding new advanced ...
The computer aided design program developed in this research effort found the optimal locations of the two wing spars to be at 25% and 60% of the local chord length, respectively, after 136 ...
This paper presents a method for simultaneous optimization of the outer shape and internal topology of aircraft wings, with the objective of minimizing drag subject to lift and compliance constraints for multiple load cases. The physics are evaluated by the means of a source-doublet panel method for the aerodynamic response and linear elastic finite elements for the structural response, which ...
The aerodynamic loads generated in a wing are critical in its structural design. When multi-element wings with wingtip devices are selected, it is essential to identify and to quantify their structural behaviour to avoid undesirable deformations which degrade the aerodynamic performance. This research investigates these questions using numerical methods (Computational Fluid Dynamics and Finite ...
This paper aims to examine the categories of flying robots based on the features that include a range from petite to large and its body structure, wing designs, tail design, propulsion system, and ...
This paper investigates the structural behaviour of the wing subjected to the aerodynamic loads during the flight using finite element analysis of wing flexure deformation. In this work, three different types of wing models are established. Material characteristics, the wing structure, and design principles have been taken into account. The assembly of the wing model consists of the thin skin ...
It indicates the initial arrangement of the wing is basically reasonable. As can be seen in Table 2, the mass of the wing in case 1 is 11.51% lower than that of the initial wing, while that in case 2 is a 12.39% weight reduction. This indicates that the deletion of the front ribs is of great bene t to weight loss.
This research explores the feasibility of this concept by designing a tensegrity-based twisting wing to replace the original wing of an existing UAV. Primary design parameters such as wingspan, airfoil shape, and chord length are kept constant while a design-of-experiment using the Taguchi method was conducted to evaluate the effect of varying ...
The designs that can realize a shape-shifting aircraft include variable-span wing, folding wing, variable area wing, variable-sweep wing, and so on. F-14, F-111, X-53, B-1, and MiG-23 have adopted the variable-sweep wing design scheme to adaptively adjust their performance in the subsonic and supersonic flight regimes.
An optimization technique called shape-linked optimization, which is different from the traditional optimization method, is introduced in this paper. The research introduces an updated wing optimization design in an effort to adapt to continuous structure changes and shapes while optimizing for a lighter weight of the structure. The changing tendencies of the thickness of wing skins and the ...
SUBMIT PAPER. Proceedings of the Institution of Mechanical Engineers, Part G: Journal of Aerospace Engineering ... Box wing aircraft conceptual design. In: 28th international congress of the aeronautical sciences, Brisbane, ... Encyclopedia of Research Design. 2010. SAGE Knowledge. Whole book . Releasing Leadership Brilliance.
In this research, aileron and morphed wings are designed and analyzed for better lift forces maneuverability at various wind speeds. Further, the conceptual design of the proposed wings using NACA 0012 standard profile is given in Sect. 2. Later in Sect. 3, ANSYS CFD simulation and analysis results are discussed in detail.
Caption. A newly developed wing architecture could greatly simplify the manufacturing process and reduce fuel consumption by improving the wing's aerodynamics. It is based on a system of tiny, lightweight subunits that could be assembled by a team of small specialized robots, and could ultimately be used to build the entire airframe. Credits.
Findings Unveil Mechanisms that Explain Flight Stability. A series of experiments using paper airplanes reveals new aerodynamic effects, a team of scientists has discovered. Its findings enhance our understanding of flight stability and could inspire new types of flying robots and small drones. "The study started with simple curiosity about ...
This paper presents the overall pros and cons of the effect of surface roughness elements over a NACA 4412 tapered, swept back half wing with a sweep angle of 30º and a dihedral angle of 5º.
International Research Journal of Engineering and Technology (IRJET) e-ISSN: 2395-0056 Volume: 09 Issue: 07 | July 2022 p-ISSN: 2395-0072 www.irjet.net Design, Fabrication and Aerodynamic Analysis of RC Powered Aircraft Wing Harish M1, Sankara Narayanan N2, Aswin Kumar G3, Subramani J4 Assistant Professor, Department of Aeronautical Engineering 2, 3, 4 UG Student, Department of Aeronautical ...
This paper presents the study of a possible novel configuration called "PrandtlPlane," having a box-wing layout derived from Prandtl's "Best Wing System" concept. The paper deals with the ...
XFLR5 is software that enables 2D and 3D aerodynamic analysis of bodies and bearing areas, separately or jointly. The software makes analysis for small Reynolds numbers. The latest version has implemented five applications: a direct 2D analysis and design, a 3D analysis and design (airfoil & wing), two ways to design and compare 2D, design a 2D ...
UAVs have become an intense field of research for aircraft designers due to better capabilities compared to manned aircraft. However, their design procedure is a challenging process as it involves meeting the requirements while keeping the design robust and achieving lower take-off weight [13], [14], [15]. With all the applications and ...
This paper focuses on the aerodynamics and design of an unmanned aerial vehicle (UAV) based on solar cells as a main power source. The procedure includes three phases: the conceptual design, preliminary design, and a computational fluid dynamics analysis of the vehicle. One of the main disadvantages of an electric UAV is the flight time; in this sense, the challenge is to create an aerodynamic ...