Imagine a symphony orchestra where each musician plays their own tune without listening to others. The result would be chaotic and dissonant, right? Similarly, in the business world, when decision-making happens in silos and planning processes are disconnected, it’s like having a group of individuals playing their own instruments without any coordination. The harmony is lost, and the organization becomes inefficient, misses opportunities, and struggles to keep up with the fast-paced market.
Integrated Business Planning (IBP) addresses these challenges by providing a comprehensive framework that integrates strategic, operational and financial planning, analysis, and reporting to drive better business outcomes. A retail company experiences a sudden surge in online sales due to a viral social media campaign. Integrated planning incorporates supply chain planning, demand planning, and demand forecasts so the company can quickly assess the impact on inventory levels, supply chain logistics, production plans, and customer service capacity. By having real-time data at their fingertips, decision-makers can adjust their strategies, allocate resources accordingly, and capitalize on the unexpected spike in demand, ensuring customer satisfaction while maximizing revenue. This blog explores the significance of IBP in today’s modern business landscape and highlights its key benefits and implementation considerations.

Integrated business planning framework
Integrated Business Planning (IBP) is a holistic approach that integrates strategic planning, operational planning, and financial planning within an organization. IBP brings together various functions, including sales, marketing, finance, supply chain, human resources, IT and beyond to collaborate across business units and make informed decisions that drive overall business success. The term ‘IBP’ was introduced by the management consulting firm Oliver Wight to describe an evolved version of the sales and operations planning (S&OP process) they originally developed in the early 1980s.
Making up the Integrated Business Planning framework are six key pillars:
1. strategic planning.
Integrated Business Planning starts with strategic planning. The management team defines the organization’s long-term goals and objectives. This includes analyzing market trends, competitive forces, and customer demands to identify opportunities and threats. Strategic planning sets the direction for the entire organization and establishes the foundation for subsequent planning roadmap.
2. Operational planning
Operational planning focuses on translating strategic goals into actionable plans at the operational level. This involves breaking down the strategic objectives into specific targets and initiatives that different departments and functions need to execute.
For example, the sales department might develop a plan to enter new markets or launch new products, while the supply chain department focuses on inventory optimization and ensuring efficient logistics. The key is to align operational plans with the broader strategic objectives to ensure consistency and coherence throughout the organization.
3. Financial planning
Financial planning ensures that the organization’s strategic and operational plans are financially viable. It involves developing detailed financial projections, including revenue forecasts, expense budgets, and cash flow forecasts. By integrating financial planning with strategic and operational planning, organizations can evaluate financial profitability, identify potential gaps or risks, and make necessary adjustments to achieve financial targets.
4. Cross-functional collaboration
A fundamental aspect of IBP is the collaboration and involvement of various functions and departments within the organization. Rather than working in isolation, departments such as sales, marketing, finance, supply chain, human resources, and IT come together to share information, align objectives, and make coordinated decisions.
5. Data integration and analytics
IBP relies on the integration of data from different sources and systems. This may involve consolidating data from enterprise resource planning (ERP) systems, customer relationship management (CRM) systems, supply chain management systems, and other relevant sources. Advanced analytics and business intelligence tools are utilized to analyze and interpret the data, uncovering insights and trends that drive informed decision-making.
6. Continuous monitoring and performance management
The Integrated Business Planning process requires continuous monitoring of performance against plans and targets. Key performance indicators (KPIs) are established to measure progress and enable proactive management. Regular performance reviews and reporting enable organizations to identify deviations, take corrective actions, and continuously improve their planning processes.
What are the benefits of Integrated Business Planning?
By integrating strategic, operational, and financial planning organizations can unlock the full potential of IBP and drive business success and achieve their goals.
Enhanced decision-making
IBP facilitates data-driven decision-making by providing real-time insights into various aspects of the business. By bringing together data from various departments, organizations can develop a holistic view of their operations, enabling them to make better-informed decisions.
Improved alignment
By aligning strategic objectives with operational plans and financial goals, IBP ensures that every department and employee is working towards a common vision. This alignment fosters synergy and drives cross-functional collaboration.
Agility and responsiveness
In the rapidly changing business landscape, agility is crucial. IBP allows organizations to quickly adapt to market shifts, demand fluctuations, and emerging opportunities. By continuously monitoring and adjusting plans, businesses can remain responsive and seize competitive advantages.
Optimal resource allocation
Integrated Business Planning enables organizations to optimize resource allocation across different functions. It helps identify bottlenecks, allocate resources effectively, and prioritize initiatives that yield the highest returns, leading to improved efficiency and cost savings.
Risk management
IBP facilitates proactive risk management by considering various scenarios and identifying potential risks and opportunities. By analyzing data and conducting what-if analyses, companies can develop contingency plans and mitigate risks before they materialize.
Essential steps for implementing Integrated Business Planning
Implementing an effective IBP process requires careful planning and execution that may require substantial effort and a change of management, but the rewards are well worth it. Here are some essential strategic steps to consider:
1. Executive sponsorship
Establish leadership buy-in; gain support from top-level executives who understand the value of Integrated Business Planning and can drive the necessary organizational changes. Leadership commitment, led by CFO, is crucial for successful implementation.
2. Continuous improvement
Continuously monitor and adjust; implement mechanisms to monitor performance against plans and targets. Regularly review key performance indicators (KPIs), conduct performance analysis, and generate timely reports and dashboards. Identify deviations, take corrective actions, and continuously improve the planning processes based on feedback and insights.
3. Integration of people and technology
To foster cross-functional collaboration, the organization must identify key stakeholders, break down silos, and encourage open communication among departments. Creating a collaborative culture that values information sharing and collective decision-making is essential.
Simultaneously, implementing a robust data integration system, encompassing ERP, CRM, and supply chain management systems, ensures seamless data flow and real-time updates. User-friendly interfaces, data governance, and training provide the necessary technological support. Combining these efforts cultivates an environment of collaboration and data-driven decision-making, boosting operational efficiency and competitiveness.
4. Technology
Implement advanced analytics and business intelligence solutions to streamline and automate the planning process and assist decision-making capabilities. These solutions provide comprehensive functionality, data integration capabilities, scenario planning and modeling, and real-time reporting.
Integrated Business Planning software
From a tech perspective, organizations need advanced software solutions and systems that facilitate seamless data integration and collaboration to support IBP. Here are some key components that contribute to the success of integrated business planning:
1. Corporate performance management
A platform that serves as the backbone of integrated business planning by integrating data from different departments and functions. It enables a centralized repository of information and provides real-time visibility into the entire business.
2. Business intelligence (BI) tools
Business intelligence tools play a vital role in analyzing and visualizing integrated data from multiple sources. These tools provide comprehensive insights into key metrics and help identify trends, patterns, and opportunities. By leveraging BI tools, decision-makers can quickly evaluate financial performance, make data-driven business decisions and increase forecast accuracy.
3. Collaborative planning and forecasting solutions
Collaborative planning and forecasting solutions enable cross-functional teams to work together in creating and refining plans. These planning solutions facilitate real-time collaboration, allowing stakeholders to contribute their expertise and insights. With end-to-end visibility, organizations can ensure that plans are comprehensive, accurate, and aligned with business strategy.
4. Data integration and automation
To ensure seamless data integration, organizations need to invest in data integration and automation tools. These tools enable the extraction, transformation, and loading (ETL) of data from various sources. Automation streamlines data processes reduces manual effort and minimizes the risk of errors or data discrepancies.
5. Cloud-based solutions
Cloud computing offers scalability, flexibility, and accessibility, making it an ideal choice for integrated business planning. Cloud-based solutions provide a centralized platform where teams can access data, collaborate, and make real-time updates from anywhere, at any time. The cloud also offers data security, disaster recovery, and cost efficiencies compared to on-premises infrastructure.
6. Data governance and security
As organizations integrate data from multiple sources, maintaining data governance and security becomes crucial. Establishing data governance policies and ensuring compliance with data protection regulations are vital steps in maintaining data integrity and safeguarding sensitive information. Implementing robust data security measures, such as encryption and access controls, helps protect against data breaches and unauthorized access.
IBM Planning Analytics for Integrated Business Planning
IBM Planning Analytics is a highly scalable and flexible solution for Integrated Business Planning. It supports and strengthens the five pillars discussed above, empowering organizations to achieve their strategic goals and make better data-driven decisions. With its AI- infused advanced analytics and modeling capabilities, IBM Planning Analytics allows organizations to integrate strategic, operational, and financial planning seamlessly. The solution enables cross-functional collaboration by providing a centralized platform where teams from various departments can collaborate, share insights, and align their plans. IBM Planning Analytics also offers powerful data integration capabilities, allowing organizations to consolidate data from multiple sources and systems, providing a holistic view of the business. The solutions’s robust embedded AI predictive analytics uses internal and external data and machine learning to provide accurate demand forecasts. IBM Planning Analytics supports continuous monitoring and performance management by providing real-time reporting, dashboards, and key performance indicators (KPIs) that enable organizations to track progress and take proactive actions. As the business landscape continues to evolve, embracing Integrated Business Planning is no longer an option but a necessity for organizations. To succeed in this dynamic environment, businesses need an integrated approach to planning that brings all the departments and data together, creating a symphony of collaboration and coordination.
More from Artificial intelligence
Ai transforms the it support experience.
5 min read - We know that understanding clients’ technical issues is paramount for delivering effective support service. Enterprises demand prompt and accurate solutions to their technical issues, requiring support teams to possess deep technical knowledge and communicate action plans clearly. Product-embedded or online support tools, such as virtual assistants, can drive more informed and efficient support interactions with client self-service. About 85% of execs say generative AI will be interacting directly with customers in the next two years. Those who implement self-service search…
Bigger isn’t always better: How hybrid AI pattern enables smaller language models
5 min read - As large language models (LLMs) have entered the common vernacular, people have discovered how to use apps that access them. Modern AI tools can generate, create, summarize, translate, classify and even converse. Tools in the generative AI domain allow us to generate responses to prompts after learning from existing artifacts. One area that has not seen much innovation is at the far edge and on constrained devices. We see some versions of AI apps running locally on mobile devices with…
Chat with watsonx models
3 min read - IBM is excited to offer a 30-day demo, in which you can chat with a solo model to experience working with generative AI in the IBM® watsonx.ai™ studio. In the watsonx.ai demo, you can access some of our most popular AI models, ask them questions and see how they respond. This gives users a taste of some of the capabilities of large language models (LLMs). AI developers may also use this interface as an introduction to building more advanced…
IBM Newsletters
What Is Integrated Business Planning and Why Is It Important?

Think of modern integrated business planning, or IBP, as a mashup of supply chain optimization, financial planning and analysis (FP&A) and operational best practices, powered by a companywide culture that’s all about delivering the speed, savings and responsiveness today’s consumers demand while managing risk.
Note that IBP as a fuzzy, buzzword-laden process methodology has been around for years. It’s usually implemented by expensive consultants in sprawling, global corporations that know they need to unify siloed sales, supply, financial and operational resources — before more nimble competitors relegate them to the former Fortune 500 list.
We’re here to argue that IBP deserves a second look for any company that wants to maximize profits and minimize the risks associated with growth. No six-figure consultant required.
What Is Integrated Business Planning?
On paper, IBP is a process for aligning a company’s business goals with its finance, supply chain, product development, marketing and other operational functions. Think parts suppliers that work with automakers and need to constantly retool to accommodate design changes, or food producers operating on razor-thin margins that must manage both uncertain supply chains and fickle customer tastes.
Lag, and a competitor is standing by to take that business. Move quickly but in a disjointed manner and you may keep customers, but at the expense of higher cost of goods sold (COGS) and lower profitability.
For example, consider PickerBots, a fictional maker of custom machinery for manufacturing and warehouse operations. When the company launched in 2017, it found a niche in restaurant supply, but when that business slowed significantly in 2020 the founders decided to retool. Rather than simply changing up its marketing, the firm set out to revamp its business strategy. A top-down scenario planning exercise led to realigning its R&D, demand forecasting, profitability and revenue analysis, supply chain planning and marketing and sales strategy.
The company culture was already strong on innovative thinking, but the founders realized that the link between strategic planning and day-to-day operations could use improvement. Enter a new COO with the chops to align operations with product demand planning and sales and marketing while weighing in on financial targets and budgets.
Key Takeaways
- In a company that embraces IBP, there’s a direct line from purchasing, production and inventory to sales and marketing to financial targets and budgets.
- A key IBP benefit is that materials are bought at the right price, at the right time and in just the right quantity to fulfill market demand.
- Successful IBP delivers closer collaboration and more trust among departments, leading to improved decision-making.
- IBP may require significant cultural change and cannot be successful without unwavering commitment from the executive team.
Integrated Business Planning Explained
Many organizations mistake IBP for a supply-chain-centric exercise. While linking supply chain planning with other departments, from sales and operations through finance, is important, that’s just one element.
IBP aligns business g oals and financial t argets with decisions and execution across the entire business.
There is overlap with financial planning and analysis (FP&A). Because an IBP initiative gathers data from across the enterprise, companies get better at predictive analysis. Now, when purchasing forecasts a parts shortage, supply and operations can adjust before customers are affected.
It’s also not a one-and-done exercise. PickerBots’ new COO advises looking a minimum of 36 months out. Leaders will need to keep their eyes on that long-range plan while continually reviewing, revising and communicating financial and operating results. What supply chain gaps have opened up, and how can we close them? Do we need to update our scenario planning? Are we tracking the right financial KPIs?
A crucial element of IBP is that it integrates financials with operations. Here’s a structure that PickerBots plans to follow.
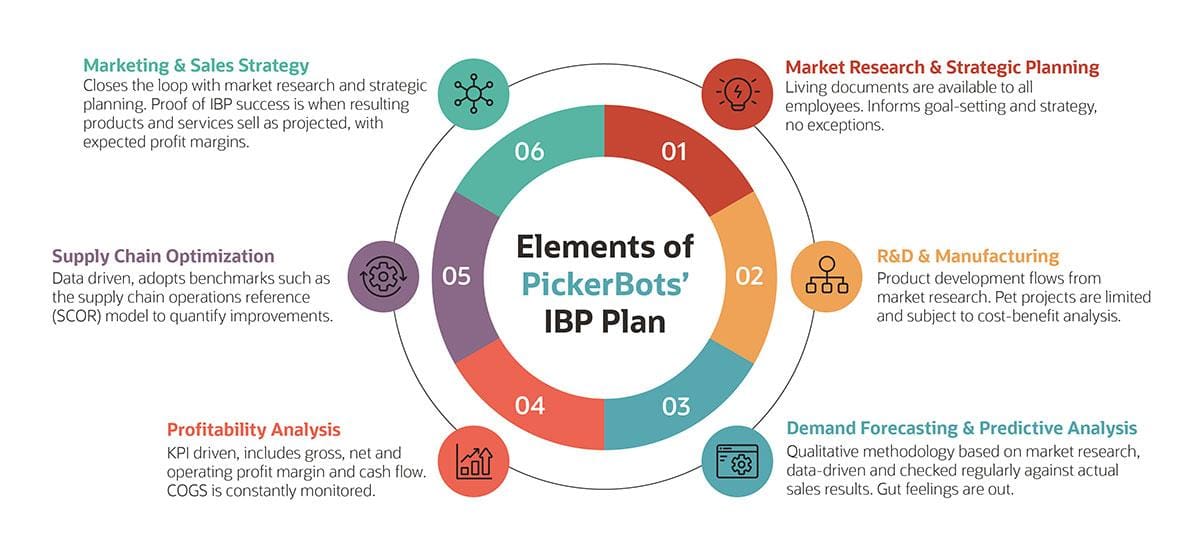
Why Is Integrated Business Planning Important?
Companies that undertake IBP realize a number of practical benefits, including reduced holding costs, more responsive customer service and demand fulfillment, shorter time to market for new products and an improved correlation between demand planning and fulfillment.
After PickerBot’s scenario planning and strategy session, the company decided to jump into the emerging collaborative robot, or cobot, market. A collaborative robot is designed to safely interact with human workers. PickerBot’s leaders believe demand will increase for “pick and place” cobots with fine motor skills for use on manufacturing lines as well as in agricultural settings.
Now that the company has its strategic direction, the COO wants to focus on three higher-level concepts before delving into more practical areas, like financial planning and analysis and supply chain optimization. That’s because without goal-setting, PickerBots won’t be able to define success.
Alignment and accountability
All executives must agree on three things: What are our corporate goals? What does success look like for each? How will I and my team contribute and be accountable?
The company’s goals are grouped into four areas: industry-focused, operations and supply chain, financial and marketing and sales. The management team will review all goals to make sure they align with strategy and are both actionable and achievable.
Industry-focused goal: Offer the most innovative cobots on the market
What success looks like: Develop a product that can match or exceed a human worker in its ability to pick fragile crops without damage.
Who will execute: The R&D team
Financial goal: Diversify revenue streams
What success looks like: Minimize dependence on one market/industry. Add a services arm to generate recurring revenue from maintenance contracts, powered by sensors built in to all new products.
Who will execute: Cross-functional led by CEO and finance
Other goals might be “control costs at each step and deliver cobots to customers on time and to specifications” with an expectation to lower COGS by 10% and raise the company’s Net Promoter Score by 25% within one year. Or for sales, “find 10 new customers for the company’s agricultural cobots and bundle maintenance contracts with each sale.” That ties back to revenue diversification.
An important point: Every manager is accountable for every goal, not just those that lie within their purviews.
Informed decisions and actions
Planning across PickerBots’ supply chain was disjointed, with engineers purchasing materials direct and little central planning or cost control. As part of the IBP process, the company will adopt sales and operations planning (S&OP) principles to improve its supply chain and logistics.
Actionable goals here include building visibility into how each department is working and tying the impact of decisions to financial goals. For example, by having R&D build in sensors that can automatically collect and transmit data on a cobot’s operational status, PickerBots can proactively perform preventative maintenance so the devices are almost never down — an important selling point and a way to contribute to maintenance income.
Organizationwide, divisions need to focus less on their own needs and view actions through the lens of all goals. That means the company needs to collect a lot of timely data and use it to issue reports so managers can make better decisions, more quickly. That may require an investment in ERP and other software.
Transparency/visibility
All department heads will take part in a monthly business review, where the group will assess progress in achieving the company’s objectives. The strategic plan is also available to all staff members, and quarterly all-hands meetings will be held to gather ideas and insights and walk through KPIs.
Four success metrics for the IBP process include:
1. Getting all stakeholders to buy in to corporate goals so that everyone agrees and understands what the business wants to achieve and how it will get there. There are clear responsibilities for each function in the pursuit of goals.
2. Basing business decisions on data. The integration of finance into product, demand and supply functions is key here, as are selecting the right KPIs.
3. Tying decision-making to outcomes and improving accountability. Because every department is responsible for providing accurate numbers and projections, there’s less risk that the CFO and finance team are left holding the bag if revenues fall short.
4. Shifting the culture to embrace cross-functional collaboration. An IBP process encourages openness and trust, and as a result more deeply engages and empowers employees. As an action item, each R&D and manufacturing team member will spend a week annually accompanying sales reps on customer calls.
What Is the Difference Between S&OP and IBP?
The term “IBP” was coined by management consultancy Oliver Wight to describe the next iteration of the sales and operations planning (S&OP) process Wight developed in the early 1980s.
The big difference between IBP and S&OP is that the latter has become the domain of supply chain and logistics specialists, particularly those involved in supply-and-demand balancing and planning. S&OP is execution-focused and involves a traditional budgeting process.
In contrast, IBP takes a more cross-functional and holistic approach to weaving business goals through every function. As a result, in theory, supply chain management is proactive and optimized.
IBP includes S&OP processes but because it involves cultural change, without executive buy-in, IBP will not be successful.
Some major differences between S&OP and IBP are:
6 Steps in the Integrated Business Planning Process
Now that its goals are set, PickerBots can take the next steps in its IBP journey.
1. Determine what is holding the company back. Is it a lack or growth or profitability? Is the product portfolio too complex? Has the business lost competitiveness in its space? For our manufacturing firm, the main problem was overfocus on one niche market.
2. Engage and educate employees. Once leadership buys in to goals, that enthusiasm must trickle down through the ranks. Unless everyone is committed to integrated business planning, success will be elusive. The COO recognizes that a formal employee engagement program will keep workers invested in the success of the business and actively working to meet strategic goals.
3. Set up a tiger team. IBP success comes from tight coordination, constant communication and accountability for KPIs. It’s a cultural shift that will take time to propagate throughout the business. To jumpstart things, PickerBots identified engaged employees within each functional area and assigned them to a daily 20-minute standup call. Now, say a shipment of RFID readers needed by manufacturing will be two weeks late. The purchasing team member shares that information promptly so that sales can manage customer expectations and finance can account for delayed revenue. If the problem recurs, the company can seek out new suppliers. No more surprises.
4. Establish a project/product prioritization process. IBP takes discipline. Only projects that forward the company’s strategic goals get resources. Same for products. That might mean sunsetting a line that’s still selling but lacks growth potential. All managers who require resources or have a product or service launch idea fill out a cost-benefit analysis template that is tailored to reveal whether expected benefits and costs align with goals. Leadership prioritizes using this process. No more sacred cows.
5. Expand the finance team’s influence. Finance needs to sit in on product planning, supply chain optimization and sales strategy meetings. Specifically, choose a finance team member well-versed in FP&A functions. FP&A professionals inform major decisions made by the executive team and collect and analyze financial data from across the organization to create reports that reveal whether goals are being met — and if not, why not? How do we fix the problem? Like many smaller firms, PickerBots doesn’t have a dedicated FP&A staffer, so the head of finance assigns an accounting team member who knows the business and has an aptitude for data collection and number crunching.
6. Adopt technology and tools to support IBP. If the forecasting process is seen as a quarterly or annual exercise imposed by finance and yielding little benefit to departments, IBP can’t succeed. Companies with static, point-in-time budgets need to adopt rolling forecasts to make sure the business stays on track. And, finance teams need to be able to easily access the data they need from each operational area. Both rolling forecasts and better use of data require technology and a commitment to transparency. You can’t manage what you can’t measure.
Traditional vs. Rolling Forecasts
5 tips to succeed at integrated business planning.
Some ways the COO plans to set PickerBots up for success include:
1. Sell IBP as a way to bring order from chaos. For example, large companies, especially those that have engaged in a number of mergers and acquisitions, may have thousands of SKUs and product codes. One big manufacturer Oliver Wight worked with used IBP to whittle 120,000 item numbers down to about 10,000 and reduce inventories by 50% while improving on-time, in-full delivery by up to 20%. For a smaller company, IBP can prevent ever getting in a situation where it needs to slash 90% of SKUs.
2. Adopt a continuous improvement mindset. All parts of any production or service system, particularly people, are interconnected, inform one another and are mutually dependent on generating successful outcomes. This practice’s origin comes from Kaizen, a Japanese term meaning “change for the better.” Originating in Japan, the business philosophy looks to continuously improve operations and involve all employees, from assembly line workers to the CEO. It’s a way to reinforce IBP.
3. Get buy-in from the CIO. PickerBots’ CIO came up through the ranks of manufacturing IT and is familiar with the concept of Total Quality Management (TQM), which has overlap with IBP. That went a long way in communicating the benefits of IBP and freeing up budget for technologies that can make IBP work, like ERP, enterprise performance management (EPM), supply chain management and real-time-capable accounting and finance software — especially important to realize the “one set of numbers” value proposition.
4. Apply risk management principles. Disasters large and small happen. While the zen of IBP skews toward positive and upbeat, make sure department heads are doing scenario planning and what-if analyses to model operational risk — like overdependence on one market. Consider assigning your tiger team a secondary function as a crisis management strike force.
5. Don’t forget HR. Labor is likely your company’s biggest operating expense, so ensure that it’s working for your IBP effort, not against it. A human resources professional can identify traits in applicants — like team players who are data driven and comfortable with transparency — that predict whether they will be contributors to IBP success.
Benefits of Integrated Business Planning
Research shows that the main benefit of implementing IBP is increased revenue, followed by forecast accuracy and improved Perfect Order Delivery rates.
Three additional key benefits:
Real-time insights: Once companies have instituted rolling forecasts, for example, finance can more quickly and accurately answer questions on spending and cash flow. Expect more accurate KPIs across the board.
Ownership: The flip side of accountability is that in a company fully embracing IBP, all employees assume responsibility for meeting all goals. So you’d better make sure that authority to make decisions is decentralized and tied to responsibility for outcomes, because there are few bigger morale killers than accountability without the power to effect success. Companies can further nurture a culture of ownership by tying rewards to meeting or exceeding goals.
Improved customer satisfaction: While more on-time, in-full deliveries make customers happy, that’s not the only way IBP improves Net Promoter Scores. Better planning yields better insights into what customers want, and a strong company culture often leads to improved customer empathy and its associated benefits.
Integrated Business Planning Adoption Challenges
Where a business starts with IBP depends on its maturity. Companies with dog-eat-dog cultures and highly siloed processes have a lot of work to do. These tend to be firms with traditional top-down management structures, static annual budgeting with little ability to generate forward-looking projections and dated business plans that are misaligned with current customer needs.
While all are thorny structural challenges, a leadership team that’s averse to placing trust and decision-making authority at lower levels of the organization is in even worse shape. Companies with autocratic, command-and-control styles must be willing to decentralize authority if they hope to realize IPB’s benefits.
Even businesses with mature, integrated processes and egalitarian cultures often get tripped up by “top down” versus “bottom up” KPI reporting and budgeting. IBP requires businesses to focus less on finance developing a top-line budget and then handing departmental budgets down from on high. Rather, they need to become comfortable with a bottom-up process, where departments start with a plan of what they want to achieve, calculate what it will cost and then feed a number up to the finance team, which uses that input to calculate the total budget.
Companies not already using at least a somewhat flexible budgeting process are likely to find this shift difficult. One way to jump-start the transformation might be a modern form of zero-based budgeting.
Steps of Zero-Based Budgeting for 2021
- Create a strategic vision for ZBB: Identify cost targets, relevant KPIs and goals.
- Evaluate business units to select ZBB candidates (also referred to as “decision units,” or any organ of the business that operates independently with its own budget).
- Start selected budgets from scratch (i.e., from zero).
- Each decision unit provides “decision packages,” which break down each activity in terms of its objective, funding needs, justification in the context of company goals, technical viability and alternative courses of action.
- Evaluate each proposed item to determine its value-add to the company and whether the entire cost is justified. What does the expenditure bring back to the company?
- Prioritize costs based on company goals. Reduce or cut expenses in areas that no longer produce significant value.
- Allocate funds among areas that are productive and aligned with the business’s growth drivers.
Elements of Integrated Business Planning
Integrated business planning takes place at a regular cadence; every month is most common, so we’ll use that in our example.
These steps are standard for IBP consultants, adaptable to most industries and bake in the PickerBots COO’s virtuous cycle of market research and strategic planning, R&D and manufacturing, demand forecasting and predictive analysis, profitability analysis, supply chain optimization and marketing and sales strategy.
1. Product management review. This includes all elements of product portfolio management. A cross-functional team meets monthly to review the overall status of all of product-related projects: Are they on track? Have we identified new risks and opportunities? Are the most high-value products or services prioritized? The goal is aligning the product portfolio with business goals and making sure needed raw materials and manufacturing floor capacity are lined up. Product managers revise as needed and publish an updated master plan, along with the resources it’ll take to deliver any changes.
2. Demand planning picks it up. This is a cross-functional process that helps businesses meet customer demand for products while minimizing excess inventory and avoiding supply chain disruptions. Demand planning can increase profitability and customer satisfaction and lead to efficiency gains. This team brings together members of sales, marketing and finance to determine whether they’re targeting the right markets, the right way. They work up an optimized demand plan. Relevant KPIs include sales forecast accuracy, inventory turns, fill rates and order fulfillment lead times.
3. Then, the ball goes to the supply planning team. These supply chain experts work out the optimal way to meet projected demand in a cost-effective way. The key is to have visibility into complex supply chains; a formal supply chain visibility (SCV) project helps spot and fix weaknesses, such as inventory shortfalls or order fulfillment issues, before they become major problems. Lower cost of goods sold (COGS) is the North star.
4. The integrated reconciliation team pulls together the initial product, demand and supply plans and consolidates them into one holistic business plan based on a 24- or 36-month projection; for iterative updates, teams highlight material changes. Decisions that could not be made by individual teams are prepared for executive review.
5. The executive team resolves conflicts and rolls the updated plan out to the entire company.
Integrated Business Planning Components
The components of integrated business planning comprise three buckets: Plan, execute and monitor and adjust.
Specific actions falling into each bucket vary depending on the consultancy or technology supplier. Some are more aligned with supply chain planning, while others center on S&OP or financial planning with plug-ins to other functional areas. Others are very industry-specific.
Let’s look at Oracle’s IBPX (Integrated Business Planning and Execution) for Manufacturing solution as an example. Key components include:
- Top-down and bottom-up, driver-based planning and forecasting
- Risk modeling for M&A and strategic initiatives
- Full financial statement structure for strategic and operational planning
- Predictive and prescriptive analytics and planning
- A preseeded S&OP process
- Near-real-time demand and supply balancing
- Real-time backlog management
- Automation of predictions and correction actions based on actuals
- AI-enabled operational planning, such as for sales territories and quotas
- IoT and sensor data flows integrated with automated decisions
Items like backlog management and enhanced support for IoT and sensor data are important to manufacturers like PickerBots. A retailer might be more interested in advanced inventory management. What’s important is that any solution, whether purchased as a suite or pulled together by an integrator or in-house team, supports the ability to do long- and medium-range and short-term planning based on a single, up-to-date data set that’s accessible to all authorized stakeholders.
Also look for the ability to easily model “what-if” scenarios, robust budgeting and costing and a roadmap to advanced technologies like AI and predictive analytics.
Integrated Business Planning Examples
We mentioned the Oliver Wight customer that whittled 120,000 SKUs down to about 10,000. That firm, Uponor Group, looked to IBP after a string of acquisitions left it with swelling inventories, an extremely complex portfolio and a lack of communication between siloed functions and far-flung locations. The Finnish company sells products for drinking water delivery as well as radiant heating and cooling equipment and has 3,900 employees in 30 countries. Uponor had a hard time getting a singular view of financial information across its subsidiaries, and each unit had its own practices for inventory management. Small events, such as holidays, would drive some sites to build up “just in case” inventory, and double-stocking in warehouses was common. Subsidiaries in different countries had different SKUs for the same items, and R&D was localized, with no collaboration across the company.
Upinor focused first on its supply chain and implemented S&OP processes, then advanced to IBP the following year. The results have been an increase in net sales of $1.1 billion euros, a 30% improvement in on-time in-full deliveries, a 50% reduction in inventories and increased visibility.
U.S.-based technology provider Juniper Networks also undertook an IBP project focused on implementing a digital supply chain with IBP, where the business planning process would extend S&OP throughout the supply chain, product and customer portfolios, customer demand and strategic planning.
Since undertaking the project, Juniper’s lead-time attainment is up 55%. and its inventory costs are down by 15%, allowing it to realize a positive ROI on the IBC project.
History of Integrated Business Planning
Oliver Wight developed S&OP in the 1980s as a methodology for a client that wanted to balance supply-and-demand volume. In the years since, the process evolved to integrate financials, inventory and new-product introductions.
The consultancy renamed S&OP as integrated business planning in the late 1990s to reflect the process of integrating all functions of the business behind one optimized plan. Since then, a newer term, “enterprise integrated business planning,” has emerged. EIBP includes scenario planning and extended supply chain collaboration and discusses how large companies will adopt new technologies, such as AI, big data and advanced analytics.
#1 Cloud ERP Software
Applications of Integrated Business Planning
IBP makes planning and operations much more transparent, so it’s ideal for companies moving to “just in time” manufacturing. It’s also predictive, once a company builds up some data. That can help with customer satisfaction.
PickerBots, as an example, found that it typically sees constrained supply chain capacity for motherboards in Q3. With that insight, sales and marketing can work to encourage customers to take delivery of systems in Q2 or Q4, manufacturing can prebuild products and supply chain leaders can work on alternate sources for parts that pose challenges.
Looking ahead to the future of IBP, we expect it to help companies:
- Work on ever-longer-range strategy planning, modeling and M&A activities with a higher degree of confidence.
- Detect and notify stakeholders of unanticipated events before they impact the business by using advanced technologies, including real-time sensor information and machine learning (ML) pattern recognition.
As companies build comfort with automation, advanced IBP systems can be set to take action based on analysis without human intervention. Consider a chain of bakeries; a system plugged into a long-range weather forecast system might detect a tropical storm that could raise the price of vanilla and automatically order extra.
Cloud-based technology such as ERP underpins all these advances. For example, PickerBots always set its sales goals monthly. But often these plans were delayed to let the executive team review and approve any changes, meaning operations was caught unawares. A tool like NetSuite Planning and Budgeting automates planning processes and centralizes company financial and operational data, so finance teams can disseminate updates quickly.
The next frontier? Expending IBP to business partners and suppliers, even customers. But first, companies need to get their own cultural and technology houses in order.
Business Strategy
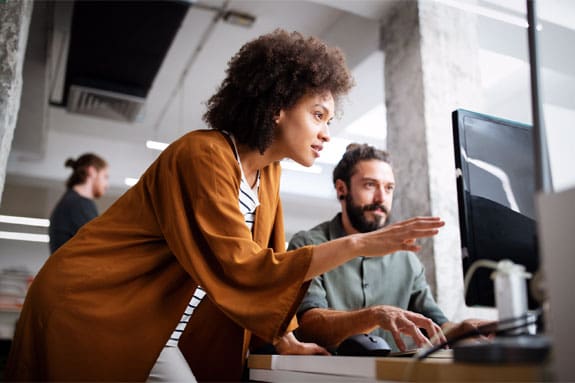
Business Process Automation: Ultimate Guide
A well-run business is always analyzing business processes and finding ways to make them more efficient. It also searches for ways to review, update, change, replace or eliminate its processes on a regular basis in order to…

Trending Articles
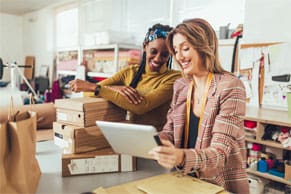
Learn How NetSuite Can Streamline Your Business
NetSuite has packaged the experience gained from tens of thousands of worldwide deployments over two decades into a set of leading practices that pave a clear path to success and are proven to deliver rapid business value. With NetSuite, you go live in a predictable timeframe — smart, stepped implementations begin with sales and span the entire customer lifecycle, so there’s continuity from sales to services to support.
Before you go...
Discover the products that 37,000+ customers depend on to fuel their growth.
Before you go. Talk with our team or check out these resources.
Want to set up a chat later? Let us do the lifting.
NetSuite ERP
Explore what NetSuite ERP can do for you.
Business Guide
Complete Guide to Cloud ERP Implementation
- Webinar Replays
- News & Press
- User Groups
- Brand Ambassadors
- OneStream Press
- Solution Exchange
- PartnerStream
- Financial Close & Consolidation
- Financial Signaling
- Reporting & Analytics
- Financial Data Quality
- Account Reconciliations
- Transaction Matching
- Compliance Solutions
- Tax Provision
- ESG Reporting & Planning
- Planning, Budgeting & Forecasting
- AI Financial Forecasting
- People Planning
- Capital Planning
- Sales Planning
- Profitability Analysis
- Manufacturing
- Financial Services
- Public Sector
- Higher Education
- Oracle Hyperion Conversion
- SAP ERP Customers

- Consulting Services
- Certification Program
- ONECommunity

- Customer Success
- News & Press
Complete Guide to Integrated Business Planning (IBP)

Integrated Business Planning, or IBP for short, is a strategic management process that connects various organizational departments to align business operations with financial goals. How? By integrating business functions – such as Sales, Marketing, Finance, Supply Chain and Operations – to create a holistic view of the company’s performance and future direction. This blog post offers a comprehensive guide to discuss what precisely IBP entails and how Finance can drive business results and collaboration within the organization via a robust and comprehensive IBP process.
What Is IBP?
While the business world and Finance have always had shared language and acronyms, some new (and reimagined) acronyms may now be flooding your feed. One such topic you may be hearing a lot about lately is Integrated Business Planning (IBP). Yet the concept of IBP isn’t new. In fact, it’s related to Sales & Operations Planning (S&OP) , a concept that’s been around awhile.
Still, IBP may seem overwhelming in the context of all the different acronyms related to financial and operational planning floating around lately. For example, IBP, S&OP, eXtended Planning and Analysis (xP&A) and others are just a few acronyms muddying the waters. But this comprehensive guide to all things IBP aims to help demystify the process.
So what, exactly, is IBP?
IBP ultimately aims to unify business strategy with planning, budgeting and forecasting activity for all business lines and functions – providing one version of the numbers. In turn, a trusted, common view of the numbers provides a robust baseline for agile decision-making. That common view also keeps all teams collectively trying to achieve the same corporate objectives while staying focused on specific KPIs. In other words, the different teams maintain their independence while working in unison to achieve corporate success by leveraging the same trusted and governed data.
The bottom line? IBP is about aligning strategy intent, unifying planning processes and bringing the organization together.
How IBP Works
The IBP process is a framework to address the C-suite needs and help implement the business strategy and manage uncertainty to improve decision-making. So what’s the secret sauce of IBP to make all of that happen? A collaboration between the different teams under a single view of the numbers that must unequivocally be tied to financial performance. That’s how the C-suite gets value from IBP. Consequently, Finance plays a central role in the IBP process.
IBP typically focuses on horizons of 24-60 months, as opposed to the short term. That focus equates to Integrated Tactical Planning or Sales and Operations Planning and Execution. Since the process must be fully integrated, it removes the departmental silos. Plus, the IBP process must adapt to the organizational construct of every business (IBP isn’t a one-size-fits-all type of process).
A typical IBP process involves several stages:
- Data Collection and Analysis : Gathering relevant data (e.g., sales forecasts, production capacities, inventory levels and financial projections) from different departments.
- Demand Planning: Predicting future demand based on historical data, market trends, customer feedback and sales forecasts.
- Supply Planning: Determining the resources and capabilities (e.g., materials, production capacity and distribution channels) needed to meet the forecasted demand.
- Financial Planning : Developing financial plans and budgets aligned with the demand and supply forecasts, considering factors such as revenue targets, cost structures and investment requirements.
- Scenario Planning: Creating alternative scenarios to assess how different strategies, market conditions or external factors impact business outcomes.
- Management Business Review : Collaborating across departments to make informed decisions on resource allocation, investments, pricing strategies and operational adjustments.
- Execution and Monitoring : Implementing the plans, tracking performance against targets, and continuously monitoring key metrics to identify deviations and take corrective actions.
The most efficient way to foster this collaboration is through a unified solution and data model that caters to the needs of the various agents involved on each review. In fact, Figure 1 shows how one solution gathering all the capabilities in the greyed area under a unified data model is the most efficient approach to IBP.

Figure 1: A Unified Data Model for IBP
Core Elements and Stages of the IBP Process
The IBP process includes the following core elements:
- Governance Structure : Establishing a cross-functional team with representatives from key departments to oversee the IBP process, define roles and responsibilities, and ensure alignment with organizational goals.
- Data Integration : Integrating data from different systems and sources to create a single source of truth for decision-making, using technologies such as enterprise resource planning (ERP) systems, Corporate Performance Management (CPM) tools, business intelligence (BI) tools and data analytics platforms.
- Collaborative Planning : Encouraging collaboration and communication between departments to share insights, align objectives and develop consensus-based plans that support overall business objectives.
- Continuous Improvement : Implementing feedback loops, performance reviews and process refinements to enhance the effectiveness and agility of the IBP process over time.
Want to learn how you can maximize the benefits of your IBP process and get leadership on board with the plan? Check out our eBook Unifying Integrated Business Planning Across Finance and Supply Chain . You’ll learn how to unify IBP across Finance and Supply Chain teams and read about use cases as proof points. Plus, you’ll gain an understanding of the unique capabilities OneStream’s Intelligent Finance Platform brings to unify Finance and Supply Chain planning activities.
Get Started With a Personal Demo

Streamline Financial Processes
A better way to drive your business
Managing the availability of supply to meet volatile demand has never been easy. Even before the unprecedented challenges created by the COVID-19 pandemic and the war in Ukraine, synchronizing supply and demand was a perennial struggle for most businesses. In a survey of 54 senior executives, only about one in four believed that the processes of their companies balanced cross-functional trade-offs effectively or facilitated decision making to help the P&L of the full business.
That’s not because of a lack of effort. Most companies have made strides to strengthen their planning capabilities in recent years. Many have replaced their processes for sales and operations planning (S&OP) with the more sophisticated approach of integrated business planning (IBP), which shows great promise, a conclusion based on an in-depth view of the processes used by many leading companies around the world (see sidebar “Understanding IBP”). Assessments of more than 170 companies, collected over five years, provide insights into the value created by IBP implementations that work well—and the reasons many IBP implementations don’t.
Understanding IBP
Integrated business planning is a powerful process that could become central to how a company runs its business. It is one generation beyond sales and operations planning. Three essential differentiators add up to a unique business-steering capability:
- Full business scope. Beyond balancing sales and operations planning, integrated business planning (IBP) synchronizes all of a company’s mid- and long-term plans, including the management of revenues, product pipelines and portfolios, strategic projects and capital investments, inventory policies and deployment, procurement strategies, and joint capacity plans with external partners. It does this in all relevant parts of the organization, from the site level through regions and business units and often up to a corporate-level plan for the full business.
- Risk management, alongside strategy and performance reviews. Best-practice IBP uses scenario planning to drive decisions. In every stage of the process, there are varying degrees of confidence about how the future will play out—how much revenue is reasonably certain as a result of consistent consumption patterns, how much additional demand might emerge if certain events happen, and how much unusual or extreme occurrences might affect that additional demand. These layers are assessed against business targets, and options for mitigating actions and potential gap closures are evaluated and chosen.
- Real-time financials. To ensure consistency between volume-based planning and financial projections (that is, value-based planning), IBP promotes strong links between operational and financial planning. This helps to eliminate surprises that may otherwise become apparent only in quarterly or year-end reviews.
An effective IBP process consists of five essential building blocks: a business-backed design; high-quality process management, including inputs and outputs; accountability and performance management; the effective use of data, analytics, and technology; and specialized organizational roles and capabilities (Exhibit 1). Our research finds that mature IBP processes can significantly improve coordination and reduce the number of surprises. Compared with companies that lack a well-functioning IBP process, the average mature IBP practitioner realizes one or two additional percentage points in EBIT. Service levels are five to 20 percentage points higher. Freight costs and capital intensity are 10 to 15 percent lower—and customer delivery penalties and missed sales are 40 to 50 percent lower. IBP technology and process discipline can also make planners 10 to 20 percent more productive.
When IBP processes are set up correctly, they help companies to make and execute plans and to monitor, simulate, and adapt their strategic assumptions and choices to succeed in their markets. However, leaders must treat IBP not just as a planning-process upgrade but also as a company-wide business initiative (see sidebar “IBP in action” for a best-in-class example).
IBP in action
One global manufacturer set up its integrated business planning (IBP) system as the sole way it ran its entire business, creating a standardized, integrated process for strategic, tactical, and operational planning. Although the company had previously had a sales and operations planning (S&OP) process, it had been owned and led solely by the supply chain function. Beyond S&OP, the sales function forecast demand in aggregate dollar value at the category level and over short time horizons. Finance did its own projections of the quarterly P&L, and data from day-by-day execution fed back into S&OP only at the start of a new monthly cycle.
The CEO endorsed a new way of running regional P&Ls and rolling up plans to the global level. The company designed its IBP process so that all regional general managers owned the regional IBP by sponsoring the integrated decision cycles (following a global design) and by ensuring functional ownership of the decision meetings. At the global level, the COO served as tiebreaker whenever decisions—such as procurement strategies for global commodities, investments in new facilities for global product launches, or the reconfiguration of a product’s supply chain—cut across regional interests.
To enable IBP to deliver its impact, the company conducted a structured process assessment to evaluate the maturity of all inputs into IBP. It then set out to redesign, in detail, its processes for planning demand and supply, inventory strategies, parametrization, and target setting, so that IBP would work with best-practice inputs. To encourage collaboration, leaders also started to redefine the performance management system so that it included clear accountability for not only the metrics that each function controlled but also shared metrics. Finally, digital dashboards were developed to track and monitor the realization of benefits for individual functions, regional leaders, and the global IBP team.
A critical component of the IBP rollout was creating a company-wide awareness of its benefits and the leaders’ expectations for the quality of managers’ contributions and decision-making discipline. To educate and show commitment from the CEO down, this information was rolled out in a campaign of town halls and media communications to all employees. The company also set up a formal capability-building program for the leaders and participants in the IBP decision cycle.
Rolled out in every region, the new training helps people learn how to run an effective IBP cycle, to recognize the signs of good process management, and to internalize decision authority, thresholds, and escalation paths. Within a few months, the new process, led by a confident and motivated leadership team, enabled closer company-wide collaboration during tumultuous market conditions. That offset price inflation for materials (which adversely affected peers) and maintained the company’s EBITDA performance.
Our research shows that these high-maturity IBP examples are in the minority. In practice, few companies use the IBP process to support effective decision making (Exhibit 2). For two-thirds of the organizations in our data set, IBP meetings are periodic business reviews rather than an integral part of the continuous cycle of decisions and adjustments needed to keep organizations aligned with their strategic and tactical goals. Some companies delegate IBP to junior staff. The frequency of meetings averages one a month. That can make these processes especially ineffective—lacking either the senior-level participation for making consequential strategic decisions or the frequency for timely operational reactions.
Finally, most companies struggle to turn their plans into effective actions: critical metrics and responsibilities are not aligned across functions, so it’s hard to steer the business in a collaborative way. Who is responsible for the accuracy of forecasts? What steps will be taken to improve it? How about adherence to the plan? Are functions incentivized to hold excess inventory? Less than 10 percent of all companies have a performance management system that encourages the right behavior across the organization.
By contrast, at the most effective organizations, IBP meetings are all about decisions and their impact on the P&L—an impact enabled by focused metrics and incentives for collaboration. Relevant inputs (data, insights, and decision scenarios) are diligently prepared and syndicated before meetings to help decision makers make the right choices quickly and effectively. These companies support IBP by managing their short-term planning decisions prescriptively, specifying thresholds to distinguish changes immediately integrated into existing plans from day-to-day noise. Within such boundaries, real-time daily decisions are made in accordance with the objectives of the entire business, not siloed frontline functions. This responsive execution is tightly linked with the IBP process, so that the fact base is always up-to-date for the next planning iteration.
A better plan for IBP
In our experience, integrated business planning can help a business succeed in a sustainable way if three conditions are met. First, the process must be designed for the P&L owner, not individual functions in the business. Second, processes are built for purpose, not from generic best-practice templates. Finally, the people involved in the process have the authority, skills, and confidence to make relevant, consequential decisions.
Design for the P&L owner
IBP gives leaders a systematic opportunity to unlock P&L performance by coordinating strategies and tactics across traditional business functions. This doesn’t mean that IBP won’t function as a business review process, but it is more effective when focused on decisions in the interest of the whole business. An IBP process designed to help P&L owners make effective decisions as they run the company creates requirements different from those of a process owned by individual functions, such as supply chain or manufacturing.
One fundamental requirement is senior-level participation from all stakeholder functions and business areas, so that decisions can be made in every meeting. The design of the IBP cycle, including preparatory work preceding decision-making meetings, should help leaders make general decisions or resolve minor issues outside of formal milestone meetings. It should also focus the attention of P&L leaders on the most important and pressing issues. These goals can be achieved with disciplined approaches to evaluating the impact of decisions and with financial thresholds that determine what is brought to the attention of the P&L leader.
The aggregated output of the IBP process would be a full, risk-evaluated business plan covering a midterm planning horizon. This plan then becomes the only accepted and executed plan across the organization. The objective isn’t a single hard number. It is an accepted, unified view of which new products will come online and when, and how they will affect the performance of the overall portfolio. The plan will also take into account the variabilities and uncertainties of the business: demand expectations, how the company will respond to supply constraints, and so on. Layered risks and opportunities and aligned actions across stakeholders indicate how to execute the plan.
Would you like to learn more about our Operations Practice ?
Trade-offs arising from risks and opportunities in realizing revenues, margins, or cost objectives are determined by the P&L owner at the level where those trade-offs arise—local for local, global for global. To make this possible, data visible in real time and support for decision making in meetings are essential. This approach works best in companies with strong data governance processes and tools, which increase confidence in the objectivity of the IBP process and support for implementing the resulting decisions. In addition, senior leaders can demonstrate their commitment to the value and the standards of IBP by participating in the process, sponsoring capability-building efforts for the teams that contribute inputs to the IBP, and owning decisions and outcomes.
Fit-for-purpose process design and frequency
To make IBP a value-adding capability, the business will probably need to redesign its planning processes from a clean sheet.
First, clean sheeting IBP means that it should be considered and designed from the decision maker’s perspective. What information does a P&L owner need to make a decision on a given topic? What possible scenarios should that leader consider, and what would be their monetary and nonmonetary impact? The IBP process can standardize this information—for example, by summarizing it in templates so that the responsible parties know, up front, which data, analytics, and impact information to provide.
Second, essential inputs into IBP determine its quality. These inputs include consistency in the way planners use data, methods, and systems to make accurate forecasts, manage constraints, simulate scenarios, and close the loop from planning to the production shopfloor by optimizing schedules, monitoring adherence, and using incentives to manufacture according to plan.
Determining the frequency of the IBP cycle, and its timely integration with tactical execution processes, would also be part of this redesign. Big items—such as capacity investments and divestments, new-product introductions, and line extensions—should be reviewed regularly. Monthly reviews are typical, but a quarterly cadence may also be appropriate in situations with less frequent changes. Weekly iterations then optimize the plan in response to confirmed orders, short-term capacity constraints, or other unpredictable events. The bidirectional link between planning and execution must be strong, and investments in technology may be required to better connect them, so that they use the same data repository and have continuous-feedback loops.
Authorize consequential decision making
Finally, every IBP process step needs autonomous decision making for the problems in its scope, as well as a clear path to escalate, if necessary. The design of the process must therefore include decision-type authority, decision thresholds, and escalation paths. Capability-building interventions should support teams to ensure disciplined and effective decision making—and that means enforcing participation discipline, as well. The failure of a few key stakeholders to prioritize participation can undermine the whole process.
Decision-making autonomy is also relevant for short-term planning and execution. Success in tactical execution depends on how early a problem is identified and how quickly and effectively it is resolved. A good execution framework includes, for example, a classification of possible events, along with resolution guidelines based on root cause methodology. It should also specify the thresholds, in scope and scale of impact, for operational decision making and the escalation path if those thresholds are met.

Transforming supply chains: Do you have the skills to accelerate your capabilities?
In addition to guidelines for decision making, the cross-functional team in charge of executing the plan needs autonomy to decide on a course of action for events outside the original plan, as well as the authority to see those actions implemented. Clear integration points between tactical execution and the IBP process protect the latter’s focus on midterm decision making and help tactical teams execute in response to immediate market needs.
An opportunity, but no ‘silver bullet’
With all the elements described above, IBP has a solid foundation to create value for a business. But IBP is no silver bullet. To achieve a top-performing supply chain combining timely and complete customer service with optimal cost and capital expenditures, companies also need mature planning and fulfillment processes using advanced systems and tools. That would include robust planning discipline and a collaboration culture covering all time horizons with appropriate processes while integrating commercial, planning, manufacturing, logistics, and sourcing organizations at all relevant levels.
As more companies implement advanced planning systems and nerve centers , the typical monthly IBP frequency might no longer be appropriate. Some companies may need to spend more time on short-term execution by increasing the frequency of planning and replanning. Others may be able to retain a quarterly IBP process, along with a robust autonomous-planning or exception engine. Already, advanced planning systems not only direct the valuable time of experts to the most critical demand and supply imbalances but also aggregate and disaggregate large volumes of data on the back end. These targeted reactions are part of a critical learning mechanism for the supply chain.
Over time, with root cause analyses and cross-functional collaboration on systemic fixes, the supply chain’s nerve center can get smarter at executing plans, separating noise from real issues, and proactively managing deviations. All this can eventually shorten IBP cycles, without the risk of overreacting to noise, and give P&L owners real-time transparency into how their decisions might affect performance.
P&L owners thinking about upgrading their S&OP or IBP processes can’t rely on textbook checklists. Instead, they can assume leadership of IBP and help their organizations turn strategies and plans into effective actions. To do so, they must sponsor IBP as a cross-functional driver of business decisions, fed by thoughtfully designed processes and aligned decision rights, as well as a performance management and capability-building system that encourages the right behavior and learning mechanisms across the organization. As integrated planning matures, supported by appropriate technology and maturing supply chain–management practices, it could shorten decision times and accelerate its impact on the business.
Elena Dumitrescu is a senior knowledge expert in McKinsey’s Toronto office, Matt Jochim is a partner in the London office, and Ali Sankur is a senior expert and associate partner in the Chicago office, where Ketan Shah is a partner.
Explore a career with us
Related articles.
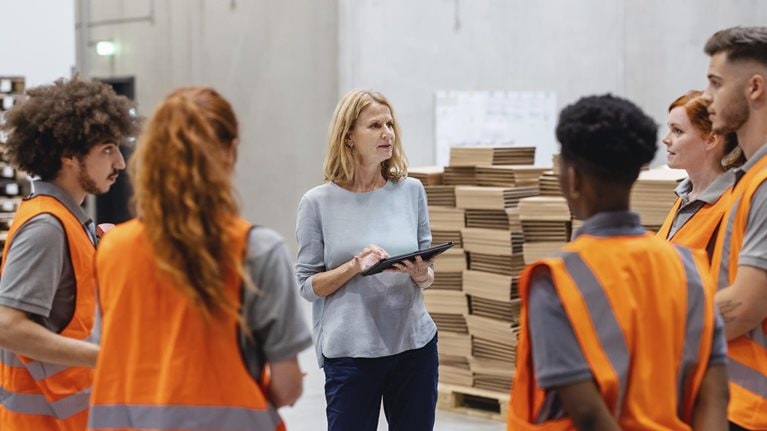
To improve your supply chain, modernize your supply-chain IT
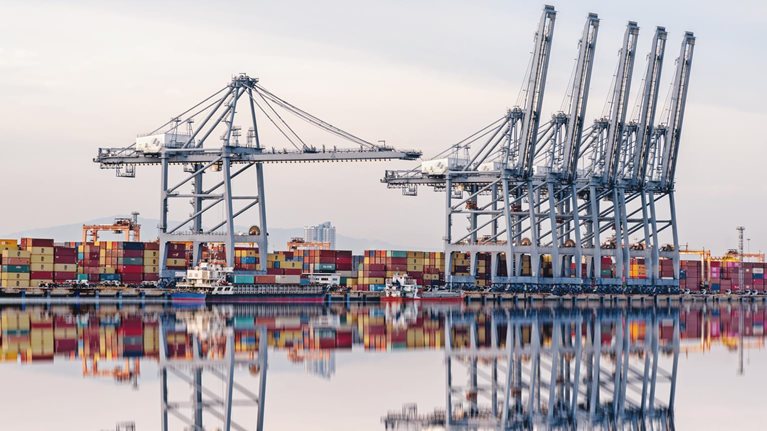
Supply-chain resilience: Is there a holy grail?
- End-to-End Strategy & FP
- Infrastructure Strategy & CP
- Business Continuity & SCRM
- Production Strategy
- Network Design
- Supply/Inventory Planning
- Product & Customer Profitability
- Sourcing & Procurement
- Production Scheduling
- Order Allocation
- Our Leadership & Board
- Testimonials
- Our Partners
- Schedule Demo
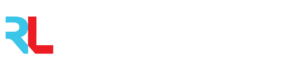
Share This Blog
At its finest, IBP is fully aligned with growth and innovation metrics, having turned S&OP into a strategic business partner. Visualize aligning your company’s operational decisions with forward-looking financial performance across various timeframes, representing complex trade-offs, constraints, and real-time business realities across the value chain; this is what a successful IBP looks like!
For more than a decade, our customers have struggled with the term IBP and how it relates to sales and operations planning (S&OP), sales and operations execution (SOE) sales inventory operations planning (SIOP), sales and operations management (S&OM), and other processes.
Despite knowing its importance, businesses have been slow to adopt integrated business planning. Many have yet to establish a fluid S&OP process.
Why Companies Struggle to Adopt IBP
So…why are companies still struggling to adopt IBP? A few reasons include:
- Conflicting goals among business units and barriers due to the evolutions of processes and technologies
- Existing technology design
- Traditional methods of doing business
A recent study shows that 79% of companies continue to use spreadsheet planning, yet only 39% say that spreadsheets support a collaborative planning process .
( Download the research perspective here for more insights and how to tackle problems with spreadsheet planning. )
Here’s the problem: Inflexible tools like spreadsheets don’t allow for a cross-functional representation of the business. Also, spreadsheets don’t provide forward-looking insights — a requirement for IBP. Instead, spreadsheets produce infeasible plans, inhibit collaborative planning, and suck loads of time that could be better spent elsewhere.
In one case study, a snack food giant wasn’t meeting demand on its most profitable product due to constrained capacities. When it tried utilizing its 20+ spreadsheets, they continued to fall short of reaching targets and became well aware that they were missing out on major profit opportunities.
Spreadsheets may work for isolated scenarios but not integrating functions to solve one common goal (meeting demand) while aligning with strategic objectives (e.g., recognizing additional profit opportunities). This is the essence of integrated business planning
Top 7 Barriers to Integrated Business Planning
In addition to spreadsheets, here are a few other barriers that we have found:
- Technology and process structures don’t allow integration. Traditional software solution designs differ in structure, hindering integration. Supply chain software was built from the ground up with a data model that was singularly focused toward certain areas like demand, supply, logistics, etc. Financial planning and analysis tools which model the General Ledger/Chart of Accounts from a transactional and roll-up perspective take the opposite approach. As such, supply chain planning and financial planning technologies were never destined to meet.
- Complex skill set required. Optimization solutions present barriers within barriers: modeling a complex supply chain often requires difficult coding and provides no visualization.
- Different cultures within the organization. Business units within the enterprise usually have a culture of its own; the undertaking of understanding another unit’s goals while striving to reach its own seemed impossible.
- Linear scenario management tools. Like optimization, scenario management tools can’t replicate real-world complexities, nor acknowledge that what-ifs are not linear.
- Use of spreadsheets as a primary planning tool. Maintaining the status quo use of spreadsheets presents an inflexible resource unable to integrate and align business goals.
- Inflexible solutions prevent data quality, access, and management. Solutions are designed to operate a specific way, and often unlike the business, meaning that the access to data or its quality and management are reliant upon the system.
- No C-Suite awareness. Understanding the meaning and feasibility of IBP often lies outside the C-Suite periphery. As a relatively new process that has been difficult to put into practice, IBP is an educational endeavor within the organization; IBP fails to get the attention of the C-Suite that benefits from it most. The CEO/CFO can be unaware of the benefits of IBP. In this post, we describe situations where employees keep profit-improving opportunities a secret , because an individual silo may be somewhat negatively impacted.
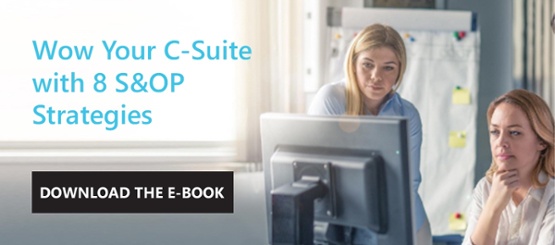
Clearly, navigating the challenges to implementing IBP starts with understanding the advantages that IBP provides.
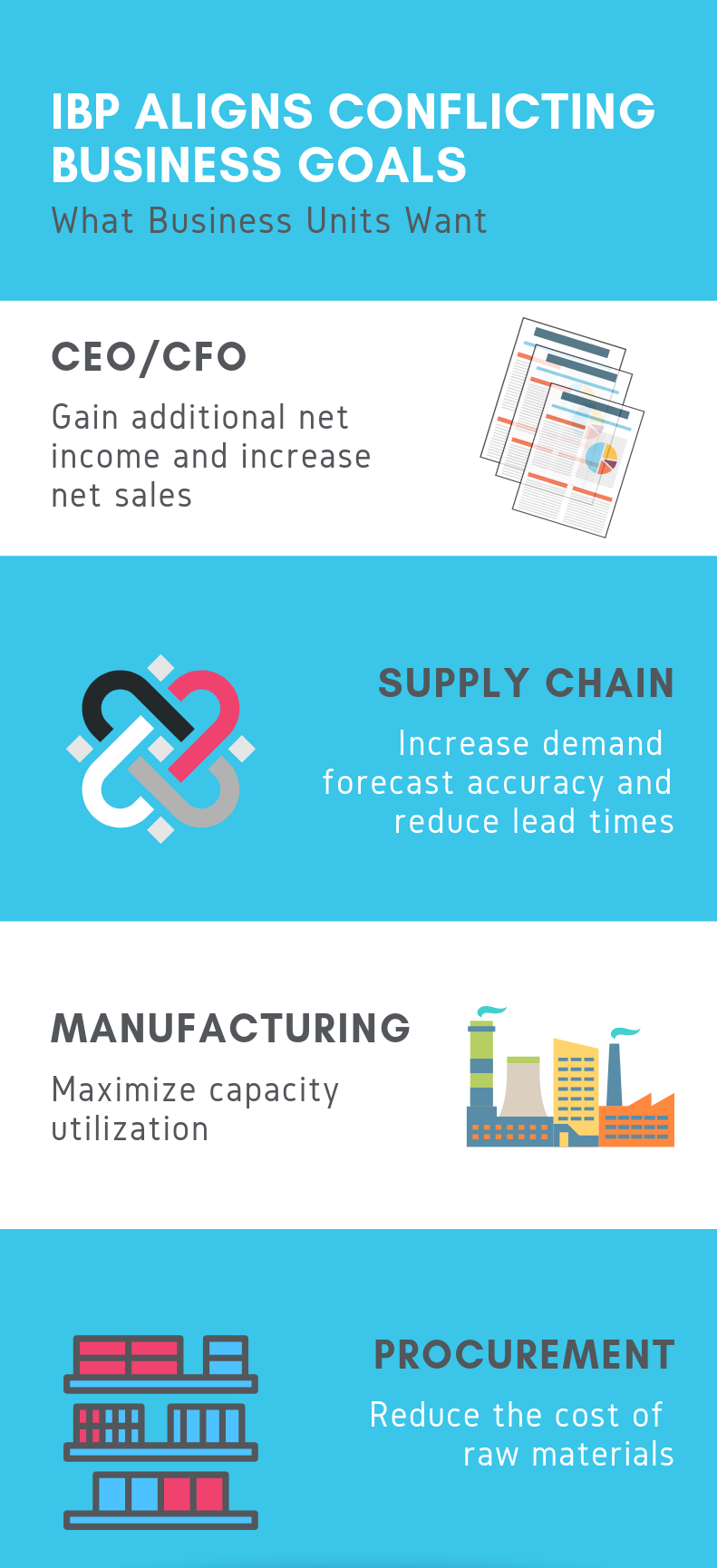
How Does IBP Work?
IBP represents the end-to-end business goals with a process that takes into consideration each business silo and its various functions. For example, is the operational plan represented in a cash flow statement? If not, what good is an operating plan that includes a product mix with margin contributions that put cash flow risk? It’s why the outcome of IBP is a true business plan, rather than a demand plan, supply plan, production plan, or a financial budget.
Through IBP, enterprises gain a single holistic plan that unifies the business, seamlessly connecting corporate performance management, financial planning processes, and operational planning systems. This comprehensive business plan increases business alignment through the sharing of performance strategies and helps quantify business risk so enterprises can rapidly adapt to meet challenges.

Why We Need IBP Now More than Ever
Even in a good economy, financial pressure to perform is paramount to maintaining a competitive edge and interesting enough, no different than the factors driving IBP following the 2009 recession. These include:
- Demand volatility has increased considerably for most companies.
- Supply complexity has increased with options such as subcontracting manufacturing and logistics operations — both of which are more common. Supply chains are broader in scope, including goods that are distributed across worldwide supply chains.
- Input cost volatility is a constant, increasing challenge for profitability. No matter the commodity (e.g., aluminum, gas, or petrochemicals), all experience sudden market changes.
- Non-linear connection between costs and volume fluctuates with a mix of fixed and variable costs; some costs vary by volume and others by time, making it more difficult to understand the financial implications of business decisions.
Yet, IBP is essentially an outgrowth of S&OP that fully aligns customer, product, demand, product, and strategic portfolios across a value chain to drive the strategy of a company, its financial performance, and its operational and tactical plans. This realization began as early as decades ago but hasn’t gained much traction in implementation until recently.
With process changes like global sourcing and distribution, the complexities of the supply chain make it necessary to synchronize operational plans with financial and strategic business goals and understand impacts to the enterprise as a whole.
The Need for What-If Analysis for Successful Integrated Business Planning
IBP is only possible with cross-enterprise, what-if scenario planning across various planning horizons. With true integrated business planning, new questions to new answers can be address — driving unmatched value to every aspect of the value chain.
In one use case involving a product mix portfolio, IBP can answer what-ifs such as:
- What if we need to move from one raw material to another, over the next several years?
- What if we want to expand into new opportunities. Where should we be investing?
- What if we make changes in design, materials, and production. How will it affect short- and long-term planning?
- What if new capital expenditures are required today and in the future?
- What if we made acquisitions instead of more capital expenditure projects?
The what-ifs allow companies to find optimal scenarios in addition to optimizing the existing way of doing business.
In other words, what-if scenario analysis is what allows companies to integrate their supply chain plans with finance, manufacturing, procurement, sales, marketing, etc.
The Unmatched Benefits of IBP
IBP has some astounding impacts on those companies who successfully adopt it. Some of the benefits our customers have seen are:
- Profit improvements equal to 2-5% of annual revenue within the first year alone
- Reduced working capital expenses by 15% or more
- Optimization of logistics, capacity, procurement, supply and demand all with the use of a single planning solution
- Improved cross-functional collaboration, planning agility, risk mitigation, and forecast accuracy
- Reduced planning timeframes from weeks or months to just a few days or hours.
- Increased stakeholder value for the company, at large
- Broader trust in plans
6 Factors to Find the Best IBP Solution
Cloud-based technologies, machine learning, and artificial intelligence (AI) sources have eliminated some technology barriers; however, traditional methods continue to play a significant role in preventing companies from using IBP.
When evaluating Integrated Business Planning solutions, these should include:
- Can execution characteristics, capabilities, and constraints be modeled correctly in order to gain an achievable strategic plan?
- Can the IBP solution co-create financial plans in sync with operational plans? Note: a financial plan refers to audit quality financial statements (e.g., Income statement, Balance Sheet, Cash Flow) which provide a full financial picture?
- Does this solution allow users to clearly understand variances – from a budget to a plan, or a baseline to a scenario, at operational and financial levels?)
- Can the solution evaluate alternative “what-if” scenarios in the formation of budgets, strategies, and operational plans? Can the scenarios consider financials as constraints? Can the scenarios optimize to multiple objective functions at the discretion of the user?
- Can we drill down and understand the root causes of those gaps?
- Does the solution have a concept of marginal contribution? This provides the specifics needed to understand the targeted actions taken. If more of this product is sold, will it have this impact? Is it worth it? If less of that product is sold, will it have this impact? Are the risks worth taking?
Intelligent Modeling as a Requirement for Successful IBP
Successful Integrated Business Planning includes unique technology capabilities. Below are the most important ones:
- An underlying holistic model that represents the business as it behaves in reality, including business, financial, and supply chain constraints. Additionally, it is essential to know how variable and fixed costs are incurred, the structure of reporting hierarchies, and process flows with mass/energy balance.
- Allowing users to simulate and optimize scenarios with multiple objective functions
- Supporting analyses from different angles (e.g., solving for optimal product mix rather than holding product mix constant, and solving for a supply plan) allow users to communicate effectively and understand the impact on key performance indicators.
- Providing rich information, including detailed cost analyses, marginal profitability, financial statements, key bottlenecks/constraints, etc.
River Logic as a Recognized Leader in S&OP/IBP
Currently, River Logic is a Leader in Gartner’s Magic Quadrant for S&OP and a Gartner-ranked global leader in both prescriptive analytics/optimization and Corporate Financial Planning. To date, we are the only vendor that is noted in all three of these areas.
River Logic has been a long-time thought leader in the IBP space and has been delivering Integrated Business Planning and S&OP solutions to global clients since 2005.
Our solution fundamentally looks at IBP through the lens of the CEO/CFO: charts of financial accounts and net income and a focus on the value chain. In other words, it truly has an integrated business plan as part of its data model regarding finance, supply, demand and any value chain function that needs to be modeled. River Logic is a comprehensive business modeling tool and much more than just supply-chain modeling tool.
1 Magic Quadrant for Sales and Operations Planning Systems of Differentiation , Gartner Research, May 2017.
More Blog Posts
Leveraging ai in supply chain strategy: insights from peter bull’s real talks webinar, ai’s transformative potential in supply chain strategy, business continuity planning in supply chain: lessons from mike tyson.
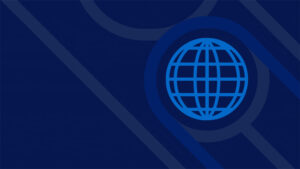
North American Building Materials Leader Cornerstone Building Brands Chooses ToolsGroup and River Logic’s Technology
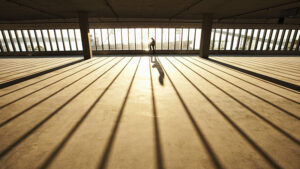
River Logic’s Value Chain Optimization technology chosen to Support Tarmac’s sustainable construction solutions
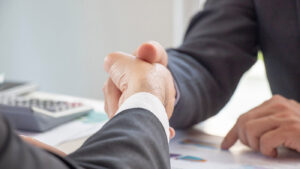
ToolsGroup And River Logic Partner to Provide a Comprehensive Supply Chain Planning Solution
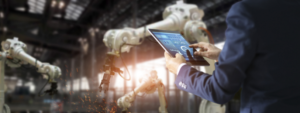
River Logic Dramatically Advances Supply Chain Experience with Enhancements to its Digital Planning Twin™
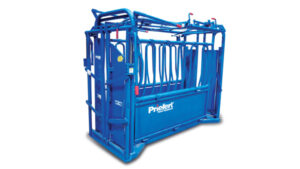
Priefert Selects River Logic to Enhance its Advanced Modeling Capabilities
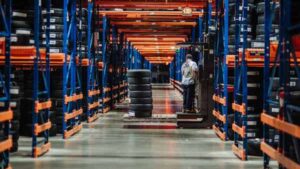
American Tire Distributors Engages River Logic’s Digital Planning Twin™ Technology Solution as Part of Digital Transformation
- End-to-End Strategy & Financial Scenarios
- Infrastructure Strategy & Capacity Planning
- Business Continuity Planning & Supply Chain Risk
- Product & Customer Profitability
- Sourcing & Procurement
- Cement Manufacturing
- Our Leadership & Board
Problem Solvers on Demand

- Consumer Goods
- Financial Services
- Industrial Goods
- Life Sciences
- Private Equity
- Professional Services
- Capabilities
- Artificial Intelligence
- Commercial Excellence
- Data Science
- Digital Health
- Digital Transformation
- Human Resources
- Interim Executives
- Life Science Strategy and M&A
- Life Science Supply Chain, Manufacturing, and Quality
- Life Science Transformation and Change Management
- Market Access & Value
- Mergers & Acquisitions
- Marketing & Sales
- Project Management
- R&D and Clinical Solutions
- Supply Chain
- Transformations
- 2024 High-End Independent Talent Report
- Guide to Working with On-Demand Talent
- The Interim Executive Advantage
- 2023 Skills Index
- 2022 Talent Lens
- The Next-Gen Staffing Strategy for Professional Services Firms
- Why You Need a Dynamic Digital Talent Strategy
- BTG Enterprise
- BTG Insights on Demand Podcast
- On-Demand Talent vs. Traditional Consulting: Costs & Value Analysis
- The Future of Work
- Resource Types
- Case Studies
- Expert Q&As
- Infographics
- Press Releases
- Research and Reports
- Talent Resources
Integrated Business Planning Best Practices: A BTG Expert Q&A
- Share this Article
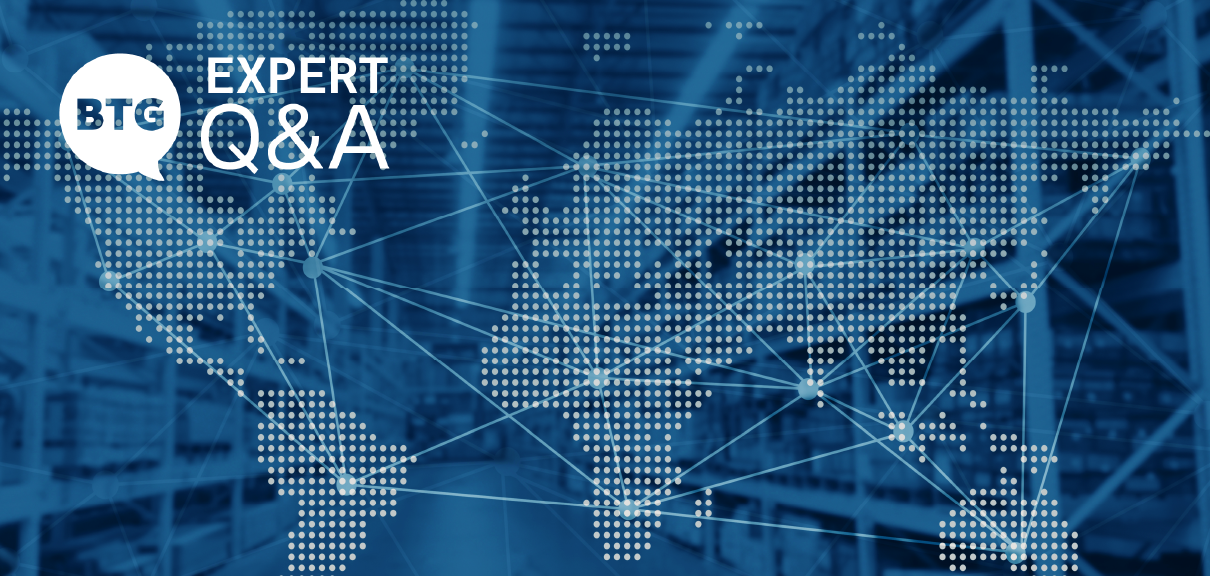
Integrated business planning (IBP) initiatives have accelerated in the wake of COVID-19 as senior executives cross-sector come to recognize that heightened economic and geopolitical volatility is here to stay. While not a new concept or trend, IBP is quickly becoming mission critical among savvy leaders who see it as the compass in the storm.
IBP at its core is a choreographing engine—tying together the right people, information, and insights at precisely the right time, in service of a more adaptive, intelligent response to cross-functional risk and opportunity.
To get the latest insights on IBP—with a particular focus on the consumer and retail industries—we’ve turned to Steve Hochman, a former Bain & Company and Abt Associates consultant who also held senior leadership roles including CEO, COO, and VP at several highly successful startups and the Nike Corporation, where he led global supply chain strategy and oversaw two major global planning transformations. Hochman advises clients cross-sector in supply chain strategy, end-to-end planning, and supply chain transformation.
Meet The Expert
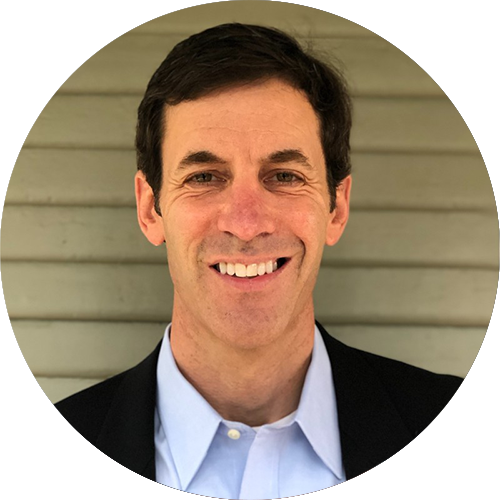
Steve Hochman
Steve hochman is the vp of research & advisory at zero100, inc. a boutique supply chain think tank that helps fortune 500 c-level executives accelerate operations innovation and transformation at scale..
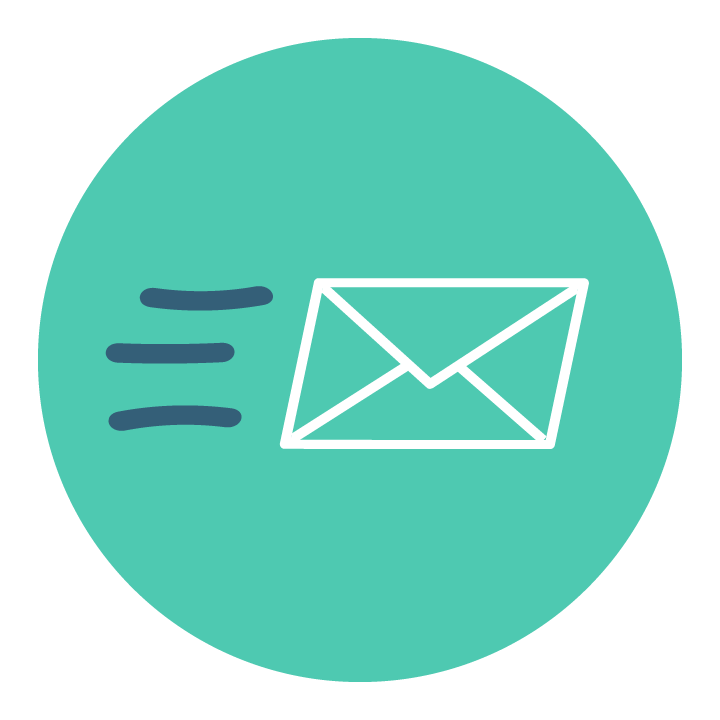
Get the Latest News and Insights
Subscribe for independent talent trends, expert advice, and updates from Business Talent Group.
Subscribe Today
What is the main goal of an integrated business plan? How does a successful IBP strategy help align high-level goals with day-to-day operations?
Integrated business planning is a process that continuously aligns targets, assumptions, and plans across all key players in a company to assure more reliable achievement of business plans and brand objectives. In plain English, it’s a way to get everyone on the same page, fast, and execute.
IBP emerged in the early 2000s because of a very practical problem: The more they grow, the more companies become functionally specialized. Particularly when the competition for talent heats up, specialization is necessary to achieve high degrees of competence and pool scarce skills. The problem is that specialization leads to silos. Over time, processes, information systems, incentives, and even team subcultures grow apart, as do their operating plans. Supply chain may see a factory constraint or an inventory risk, but sales teams are told to just keep on selling. Or, operations and sales are aligned, but neither is aligned to the budgets created by finance. And so on.
Fast forward to 2020, and you now have the added challenge of what statisticians called “randomness:” The idea that all plans to some extent are wrong because unforeseeable game-changing world events are now part of the fabric of everyone’s global operating environment. Anyone experiencing the effects of a pandemic, a post-pandemic business rebound, 50% fuel price hikes due to a war in Ukraine, an escalating US-China cold war, intensifying consumer expectations around greenhouse gas transparency, inflation that outlived every economist’s forecast, persistent labor shortages, and now revolutions in artificial intelligence that may change the nature of work itself, will know what I’m talking about.
So, having every executive on the same page is no longer a nice-to-have, it’s survival. Enter IBP.
How does IBP differ from traditional planning processes, such as Sales and Operations Planning (S&OP) or Demand Planning? What does the timeline look like for a company who decides to move from S&OP to IBP?
IBP is a natural evolution from earlier versions of planning. Way back in the 1990s, “planning” often just meant getting the orders entered properly ahead of a factory production run. All you needed was a smart analyst to key in the forecast, plus or minus maybe 20% to allow for an order cancellation or two.
S&OP emerged because, as companies grew in scale and complexity, increasingly specialized Operations and Sales functions started to feed factories different demand signals, and chaos ensued. Conversely, S&OP pioneers like Honeywell, Procter & Gamble, and Intel realized that bringing teams together with a more choreographed plan alignment process could be a source of competitive advantage. And it was. Tens of billions of dollars in shareholder value accrued to companies who brought in the top-down, cross-functional plan choreography that we now call S&OP.
The gap that remained was Finance. Particularly amongst larger companies with high degrees of business complexity, it made no sense to align sales and operations plans (often stated in units) if those plans didn’t also connect back to budgets (i.e. dollars). CFOs and divisional GMs at companies like Samsung and Nike recognized that so-called “unit-dollar translation,” while hard, was mission critical. And in many cases, those same companies invested millions of dollars in multi-year integrated planning transformations to ensure it. And thus IBP was born. No longer a supply chain process, among leaders IBP had become part of the business and systems core.
Learn more: Supply Chain Planning Gets a Post-Pandemic Makeover – Zero Percent Carbon, 100% Digital (zero100.com)
What are the key components of integrated business planning? What are the benefits of having a separate IBP division?
Integrated business planning takes existing supply, demand, commercial, product, and financial planning processes within a company and connects them. When done well, IBP is connective tissue rather than its own separate thing.
The only add-on is 1) the executive meeting that assures cross-functional alignment, and 2) the “pre-IBP” coordination that assure C-level executives are equipped to act on the hard tradeoffs of the hour.
When done right, IBP meetings are exception-based, meaning they are proactive escalations of the vital few risks and opportunities facing the business at that moment in time. And they are, crucially, decision-based. They are not about reporting the news. They are about confronting risk and opportunity, surfacing real bets and options, and making decisions that stick.
I was advising one global fashion brand recently who said culture change is actually what’s most challenging: In many companies, executive reviews are performative – focused on showcasing excellence. IBP is different. While certainly making room for celebration, the express goal is to put the ugly (or sometimes beautiful) truth on the table and confront it so that the company can move with more agility and confidence through the inevitable turbulence ahead.
The masters of IBP understand the value of this pre-IBP meta-capability and do a ton of legwork prior to the meeting itself to assure that one hour spent with all C-suite executives is set up for action.
What IBP practices are easiest for a supply chain leader to implement when beginning to take steps towards IBP excellence?
We often say the best thing to do when taking on an IBP transformation is to just get started. Bring C-level executives into the process and make them part of it. Put executive review meeting #1 on the calendar 60 days out and work towards it. Don’t overanalyze your plan alignment process. Identify the gaps by doing. Then improve.
For that first meeting: What are the big risks you face next quarter? What questions are crucial to answer to align plans against those risks? Is it a demand-side risk? A question on product assortment or pricing strategy? An emerging inventory bubble? Chances are, you know what the big issues are facing the business. The only thing missing is putting it on the table.
Behind the scenes, you can define the longer timeframe, more architectural work of systems, process, and cultural transformation. But get started. Add value now with the information and processes you have. Most IBP leaders get immense value from the associated momentum.
How can IBP help identify opportunities and risk amid uncertainty? How can supply chain leaders properly assess their processes and determine pain points?
IBP is tailor-made to identify risk and opportunity. By establishing a cadence by which we proactively bring plans together and see where assumptions are misaligned, IBP leaders develop a magical capability to surface business gaps sooner. Sometimes those gaps represent upside—untapped revenue, margin, or brand goodwill. Other times gaps really do equal risk. Either way, the continuous nature of plan alignment itself allows companies to move months faster.
The IBP lead at a $50B global diversified technology brand told me her company saves at least 6-12 months on key plan tradeoffs vs. conventional serial planning processes. And that time savings in turn is worth billions of dollars in recaptured growth and margin each year.
Knowing that IBP is not simply a supply chain planning process upgrade, how can leaders get stakeholders across the org aligned and involved?
Great question. It’s a bit of cliché to say large scale transformations require active executive sponsorship. But they really do. The more cross-functional the nature of the initiative, the greater that maxim holds true.
The first step in many IBP transformation initiatives is a Board of Directors’ presentation to educate on the “what and why” of IBP, with specific asks for help. Those presentations are often followed with carefully scripted roadshows to assure all C-level executives and their teams are clear.
IBP leaders will even go so far as to script out role descriptions for C-level executives ahead of that first experimental IBP meeting, training “upwards” to help each executive understand what they need to do to be successful. Beyond explaining “what’s in it for the boss,” IBP leaders need to explain what behaviors are required to deliver IBP value.
Another maxim is to say, “we’re all in sales.” With IBP, that’s absolutely the case. Supply chain or finance leaders who take on the IBP mantle need to develop a core competency not just in operational excellence, but in storytelling. At Zero100, we spend a lot of our energy helping executives with the latter. And it is always time well spent.
And of course, it helps if the storyteller themselves already has trust with the C-level stakeholders involved. Pick leadership talent wisely in this regard. Whether through finance, operations, or other prior experience, having a track record of adding business value is essential to opening the door to any uncertain change.
How can leaders ensure successful and effective integrated business plans? What are the best ways to measure and track related metrics, and how can they best be integrated into existing business processes?
The best way to know an IBP process is successful is if it delivers better decisions faster. Per the IBP leader at the technology company mentioned earlier, “time to decision” is the ultimate metric. The meta-metric flows from that initial indicator. For example, if I decided to liquidate excess inventory 6 months faster, how did that benefit the firm? Chances are, it led to a cleaner marketplace, more cash, and higher margins.
Companies that implement IBP wisely will often instrument their process with a logging mechanism, asking simply: “What would have happened if I had waited 6 months on this decision? How would the financials or the health of the brand have been different? What was the opportunity cost that we avoided by bringing the gap and the debate to a head sooner?” Usually that rough cut analysis is enough to prove to ourselves the huge IBP-led value accrued to the bottom line.
How can leaders ensure these plans and processes are sustainable and able to be maintained?
There are different ways to sustain momentum and operate IBP at progressively greater scale. The most important is generally organizational: IBP leaders will often create a planning “Center of Excellence (CoE)” or equivalent hub to drive continuous improvement and scale-up. Applying dedicated resources ensures organizational focus and signals to the organization that you are putting your money where your mouth is. In short, you want the horsepower in place to drive focus and trust.
Per above, the other signaling device is picking your strongest leaders to drive the change. If IBP is genuinely important to you, you’ll put your A-team on the case. Not only will that A-team have the necessary street cred at the top of the org chart, they’ll also be talent magnets for any long term change you want to drive at scale.
The other scale-driver of course is information systems. While quick process experiments are a great way to generate quick early wins, it’s pivotal to embed a technology swim lane in your transformation roadmap. Much can be achieved with spreadsheets in the first 90 days. After six months, you’ll want to have a robust plan for how you’ll integrate data to automate your IBP plan alignment processes. And you’ll want to have a forward-looking view of the technology landscape to harness fast-evolving capabilities like artificial intelligence, machine learning, and simulation through digital twins. Having a strong digital visionary embedded in your IBP initiative will be paramount.
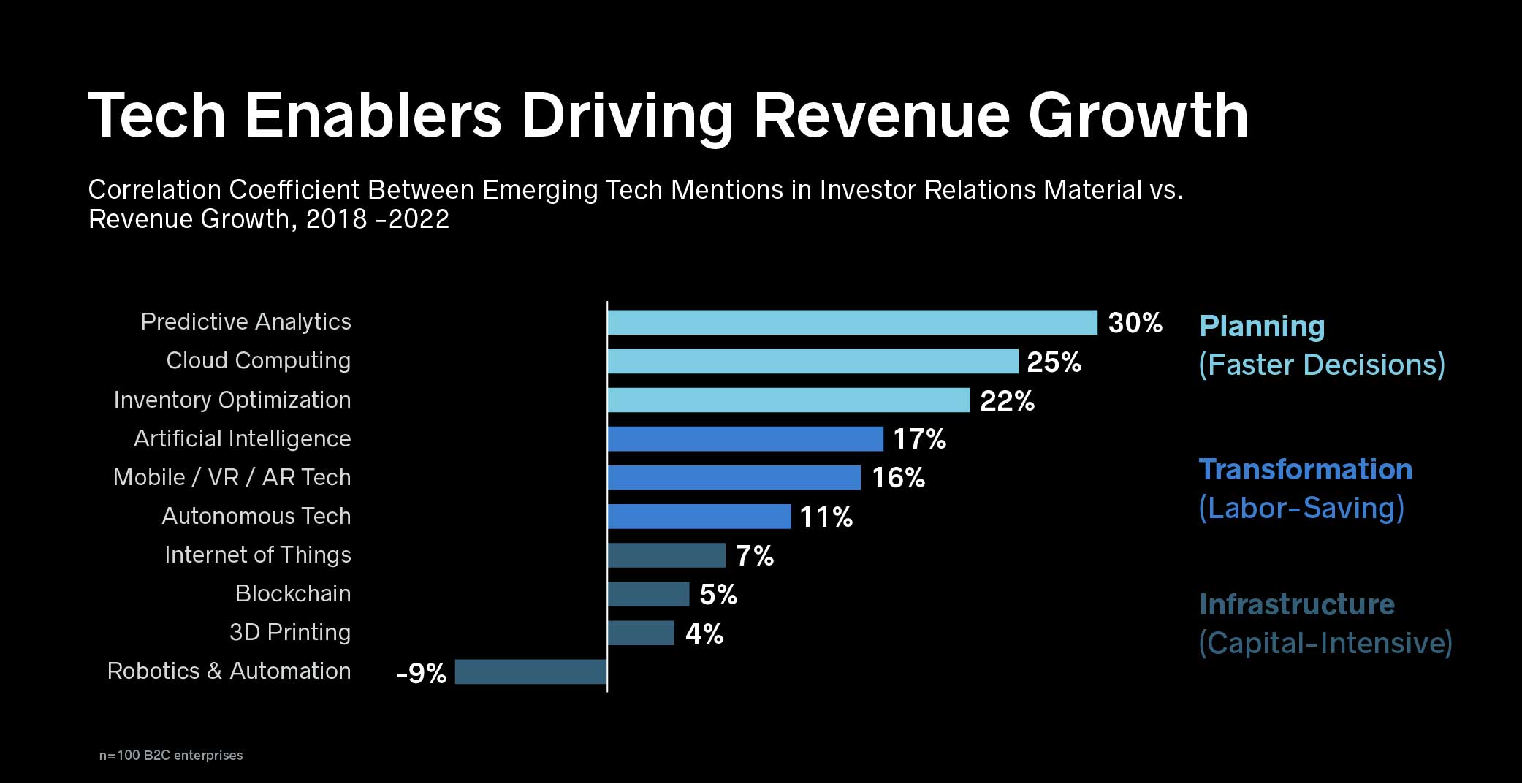
How can consumer goods companies create sustainable success and properly create a roadmap of actionable items?
Whether consumer goods or otherwise, the principles are the same.
The only additional item to consider is non-competitive peer conversations to learn from the wins and mistakes of others. A great way to accelerate learning is to plug into communities of practice that are cross-sector, e.g. a consumer goods company may learn more from a consumer electronics company than one of its direct competitors.
It’s partly why we complement our research with a lot of peer events for C-level supply chain practitioners. It’s about advancing the collective.
Where should IBP leaders be focusing for 2023? What advice do you have for them?
If I could give just one piece of advice, it would be to work back from 5 years out. Deliver rapid value because you need it for momentum. But technology is advancing too fast to leave your long-term technology and associated talent roadmap to chance. And it’s not just the fancy stuff like artificial intelligence you should track. It’s also newer cloud-based data architectures and master data management services that will fundamentally streamline and accelerate the way an IBP process will function. If you limit yourself to a 1- to 3-year vision, you may lock yourself into legacy architectures that block you from real step-function IBP advantage. You want to be the nimble one. That means careful tracking of digital trends. You may not implement all the cutting-edge tools all at once, but you want an architecture that allows you to pivot as new tools emerge. And equally important, you want to build internal skillsets to be able to digest and capitalize on the exceptional technical capabilities that are just around the corner. Deliver value now but be ready for what’s to come.
Learn more: Digital Twins Break Into the Boardroom – Zero Percent Carbon, 100% Digital (zero100.com)
Get the IBP expertise you need to succeed.
There are a lot of ways IBP experts can support your goals this year. Among them, identifying and building upon existing processes, identifying opportunities for improvement and growth, creating roadmaps for success, and providing insight on relevant current events and models. Independent talent are essential assets for companies looking to optimize and standardize supply chain and business processes in all industries thanks to their in-demand skills and niche expertise.
Reach out today to secure insights from Steve Hochman or start a project with another highly skilled independent consultant from Business Talent Group.
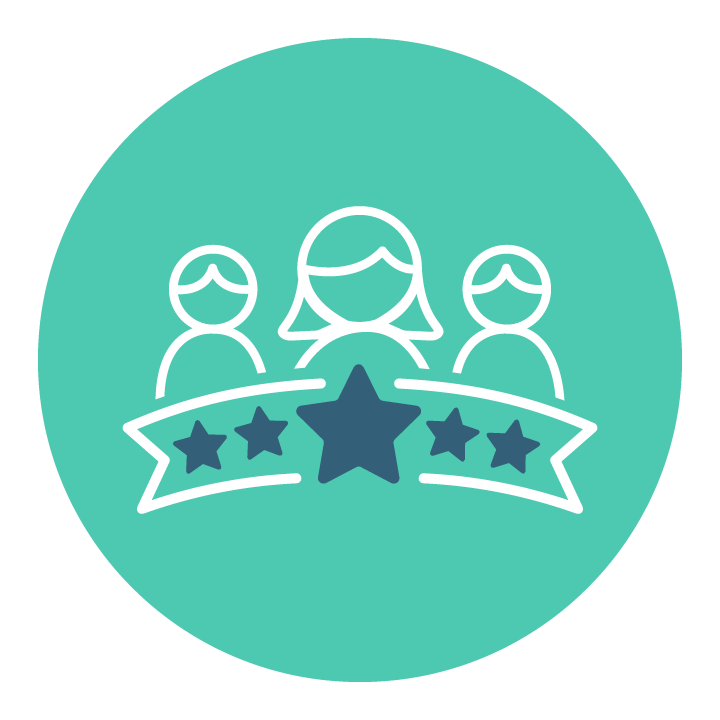
GET THE SKILLS YOU NEED
Thousands of independent consultants, subject matter experts, project managers, and interim executives are ready to help address your biggest business opportunities.
Get Started
Previous Article

The rise of high-end, on-demand talent offers professional services firms a better way to think about staff...
Next Article

Explore the top four benefits of independent consulting according to dedicated, full-time independent talen...
Get our free guide to working with on-demand talent.
Most Recent Articles

Each year, the BTG High-End Independent Talent Report reveals the top independent talent trends that executives should know. Learn more about our findings.

New report reveals how leading organizations are leveraging highly skilled, on-demand talent and interim leaders to access critical expertise and navigate a landscape marked marked by constant change.

Herman Vantrappen—strategy advisor and co-author of "The Organization Design Guide"—joins us to discuss the essentials of effective organization design.

Explore what professional authenticity means, why it's important for leaders to create an authentic organizational culture, and how to go about doing so today.

Explore how top companies are helping new leaders succeed by tapping independent talent for executive mentorship and support.


Networking is key for independent consultants who rely on their connections for project opportunities. Try these steps to build your network and deepen your existing connections.

One of today’s top leadership challenges is imposter syndrome. Studies show that this professional plight can affect individuals at all levels of the org—regardless of age or experience—at any...

In the dynamic life science industry, change is vital to maintaining competitive advantage. Start by learning how to best leverage on-demand expertise to yield successful transformations.

Learn more about “liquid talent” models and how this adaptable and dynamic staffing structure is shaping the future of work.

Mal Postings—innovation expert and technology executive—joins us to discuss the impact of artificial intelligence within the healthcare industry.

Tradition tends to bind organizations to outdated methods, even when evidence exists to prove the efficacy of a more modern approach. Often, it’s not until traditional methods become obsolete that lag

Vivek Garg—an intelligent automation and AI expert—joins us to discuss the art of intelligent automation and how advances in artificial intelligence help top companies build and scale savvy solutions.

When a project wraps up, its mission lives on. It’s up to you—and your team—to determine how to build upon the success you’ve achieved. ...

One of the biggest benefits independent talent offer is the ability to seamlessly collaborate with your existing team, but there’s an art to managing blended teams that mix internal with external...

Seemingly overnight, generative AI—or artificial intelligence capable of generating media and data in response to user prompts—became a front-page story and the hottest topic for companies large and

Today’s independents have plenty of choice when it comes to selecting their work. In fact, in competitive, cutting-edge fields like innovation, data science, and supply chain strategy, competition for

When should you bring on an independent professional? Given the challenges companies face to secure in-demand skills and expertise, the short answer is likely: now. The independent marketplace is...

Whether formal or informal, a strategic plan for your consulting practice can go a long way toward positioning you for success in the year ahead.

Whether you need a project manager to oversee a new initiative, an interim executive to lead through a critical time period, or niche expertise to capture a very specific opportunity, engaging

To achieve digital transformation in the insurance industry, leaders will need to look outside their own networks with independent talent.
- Share this Hub
- my. Inchainge
- Integrated Business Planning
What is Integrated Business Planning (IBP)? And what are the similarities, but also differences when compared to S&OP? In this article, Inchainge discusses everything you need to know about IBP.
What is integrated business planning (IBP)?
Integrated Business Planning (IBP) is the business planning process that extends the principles of Sales and Operations Planning (S&OP) throughout the value chain . It is to create a bridge between strategy and execution. IBP is a next step for companies that already have an S&OP process in place. It is a next step because it integrates the Financial Planning Cycle. The financial function will become part of this cross-functional process. In most companies the business owner of this process will change as well.
Similarities between IBP and S&OP
Integrated Business Planning and Sales and Operations Planning have several similarities between them. These are as follows:
- Monthly process
- Cross-functional approach
- Driven by business strategy
- Tactical planning at an aggregated level
Differences between IBP and S&OP
However, Integrated Business Planning includes content on top of Sales and Operations Planning:
- Financial function involved
- Integration financial planning cycle, like financial budget and forecast
- From volume planning to volume and value planning
- It drives the overall business performance
How does the IBP process work?
Companies have an annual budget cycle, based on their strategic plans and targets. The annual budget projects planned revenues and costs for the year.
In traditional S&OP companies go through a monthly process during which they project for the next 6 to 24 months where demand will go, and what resources need to be available to meet that demand. When gaps are discovered between expected demand and available resources looking this far ahead into the future, this often provides ample time to balance supply and demand, so that by the time real customer orders are submitted, demand can be met.
Suppose that during this monthly S&OP cycle, one would also look 6 to 24 months into the future where expected revenues and costs will go. And how these financial figures would look compared to the annually budgeted revenues and cost. Most likely gaps will occur here as well between the annually budgeted numbers and the monthly updated numbers. Actions could then be taken to address these gaps. Integrating a financial view. When this happens, we actually practice IBP. In IBP the relationship with the financial performance management cycle is very important. Budget and financial forecasting must be aligned and integrated with the steps from the original S&OP cycle.
The challenges of IBP
IBP is a next step in maturity after companies have implemented a proper S&OP process. Integrating finance sounds simple but is not easy at all. People from the physical supply chain side of the business, often speak a different language than people who operate on the financial side. Supply chain people often speak about units, products, and product families, whereas financial people often speak about money, currencies, etc. That also causes both functional areas to be assessed differently with the KPIs that they use. This calls for other participants in the IBP process, compared to participants in the S&OP process.
The 8 common pitfalls when implementing IBP
Be aware of the following risks related to integrated business planning:
- Lack of commitment in some of the needed departments
- If the S&OP process was not yet implemented or stable, IBP is too big of a step
- Targets and forecasts are mixed
- Information not available
- Discussion about numbers instead of the underlying assumptions
- Discussing only short horizon instead of midterm
- Too granular plans and discussions
- Thorough understanding of trade-offs is lacking
Want to know more? Experience IBP!
Because IBP is simple but not easy, a real-life experience creates enormous value for learning about this topic. The participants will feel and recognize the important issues in this process. In our business simulation game, The Cool Connection , we have incorporated the most important functions and decisions.
In this business game the team is forced to make a yearly financial budget and quarterly forecasts. The objective is to close the gaps between prediction (the budget and forecasts) on one hand and attained performance on the other. The best performing teams are both profitable and predictable at the same time. In business game The Cool Connection the team is almost experiencing a real-life IBP process.
Besides our business games, you can learn more in our articles about topics such as Total Cost of Ownership (TCO) , strategic alignment and external alignment and collaboration .
Now you know
Now you know that IBP is a next step for companies that already have an S&OP process in place, by integrating the financial planning cycle in this cross-functional process. IBP prompts companies to include planned revenues and costs in their annual budget cycle. Budget and financial forecasting must be aligned and integrated with the steps from the original S&OP cycle. Integrating finance sounds simple but is not easy at all. Supply chain people and finance people tend to speak a different language. Make sure to be aware of the 8 common pitfalls when implementing IBP.
You might want to learn more about

Learning is the process of acquiring new understanding, knowledge, behaviors, skills, values, attitudes, and preferences. There are many ways to learn but what works best? And why does it matter? In this article, Inchainge discusses everything you need to know about learning.

The Cool Connection
The Cool Connection is an innovative web-based business simulation game. It engages participants in making strategic decisions in the management of a manufacturing company of personal care products. Working in teams of four, participants will represent the functional roles of sales, purchasing, supply chain management and finance. They will be confronted with various real-life, real-time dilemmas.

- Total Cost of Ownership
When buying new equipment, the price tag only tells you part of the story. Energy costs, maintenance, and repair fees are often several times higher than the initial price! But often these are left unconsidered and hold nasty surprises further down the line. Calculating the Total Cost of Ownership is an important step when planning new investments.
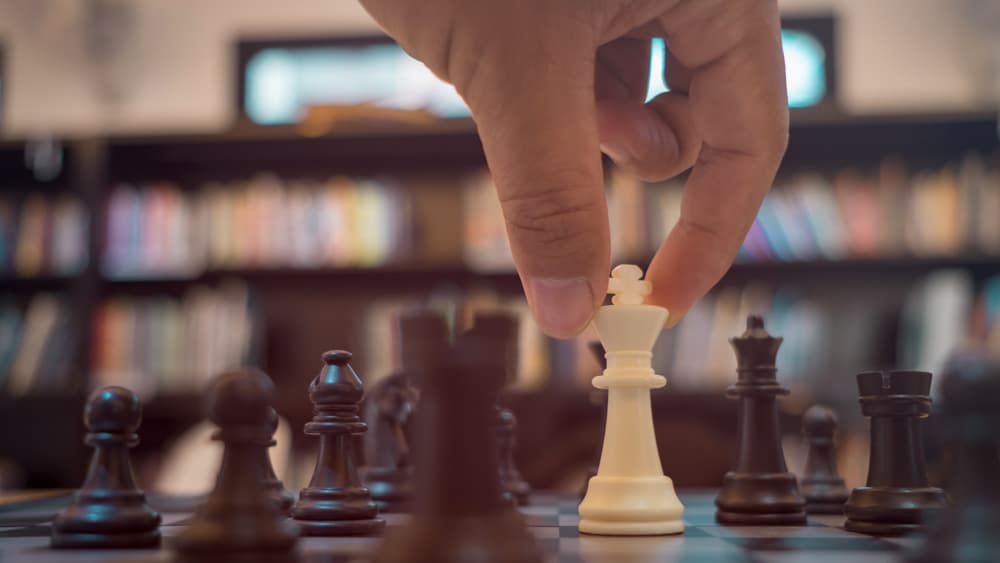
- Strategic Alignment
Understanding what strategic alignment really is and why it is important can make the difference between being a successful company and failing. Due to its complexity, the supply chain often faces challenges in aligning its strategy properly and working as one. In this article, Inchainge discusses everything you need to know about strategic alignment.

- External Alignment and Collaboration
In an increasingly global and connected world, companies rarely execute supply chain operations themselves, but must outsource certain tasks. To make sure that supply chains across several companies run smoothly, external alignment is essential. In this article, we’ll discuss everything you need to know about external alignment.
Dive into our knowledge base
- Key Performance Indicators
- Sales & Operations Planning
- Blended learning
- Delivery formats and scalability
- Experiential learning
- Flipped classroom
- Learning cycle
- Soft skills
- Building (virtual) teams
- Leadership skills
Supply chain
- Data analytics
- End-to-end Supply Chain Management
- LARG Supply Chain
- Logistics footprint
- Omnichannel
- Supply Chain
- Supply Chain Finance
- Supply Chain Management
- Supply Chain Risk management
- Supply Chain Volatility
- The Bullwhip Effect
- Sustainability
- Carbon footprint
- Circular Economy
- Does Green Governance drive the ride to a sustainable future?
- Everything You Need To Know About Eco-Efficiency
- Greenwashing: Everything you need to know
- Is it possible to measure the Triple Bottom Line?
- Sustainability v/s Circularity
- The 3Ps Series: People
- The 3Ps Series: Planet
- The 3Ps Series: Prosperity
- The Butterfly Diagram
- The Value Hill
- What are the 3Ps of Sustainability?
- What do we know about the Triple Bottom Line?
- Value Chain
Privacy Overview
Technologies
More insights for you, the 50 best oracle certifications.
- Argano 4 Microsoft
- Argano 4 Oracle
- Argano 4 Salesforce
- Argano 4 SAP
- ArganoConnect
The right foundations changes everything
- Founders Club
Alliances & Partnerships
- Customer Experience
- Commerce Solutions and Services
- Revenue Operations
- Human Capital Management
- Supply Chain Management
- Enterprise Resource Planning
- Enterprise Performance Management
- Change Management
- Cloud Migration
- Data & Analytics
- Implementation
- Integration
- Managed Services & Support
- Program Management
- Strategy & Consulting
- Training & Education
- Engineering & Construction
- Financial Services
- Healthcare & Life Science
- High Tech & Telecom
- Manufacturing
- Retail | Distribution
- Alliances and Partnerships
- Thought Leadership
- Client Stories
- Why work at Argano?
- Open Positions
- Linkedin Created with Sketch.
Made for you
What is integrated business planning (ibp), and why is it important.
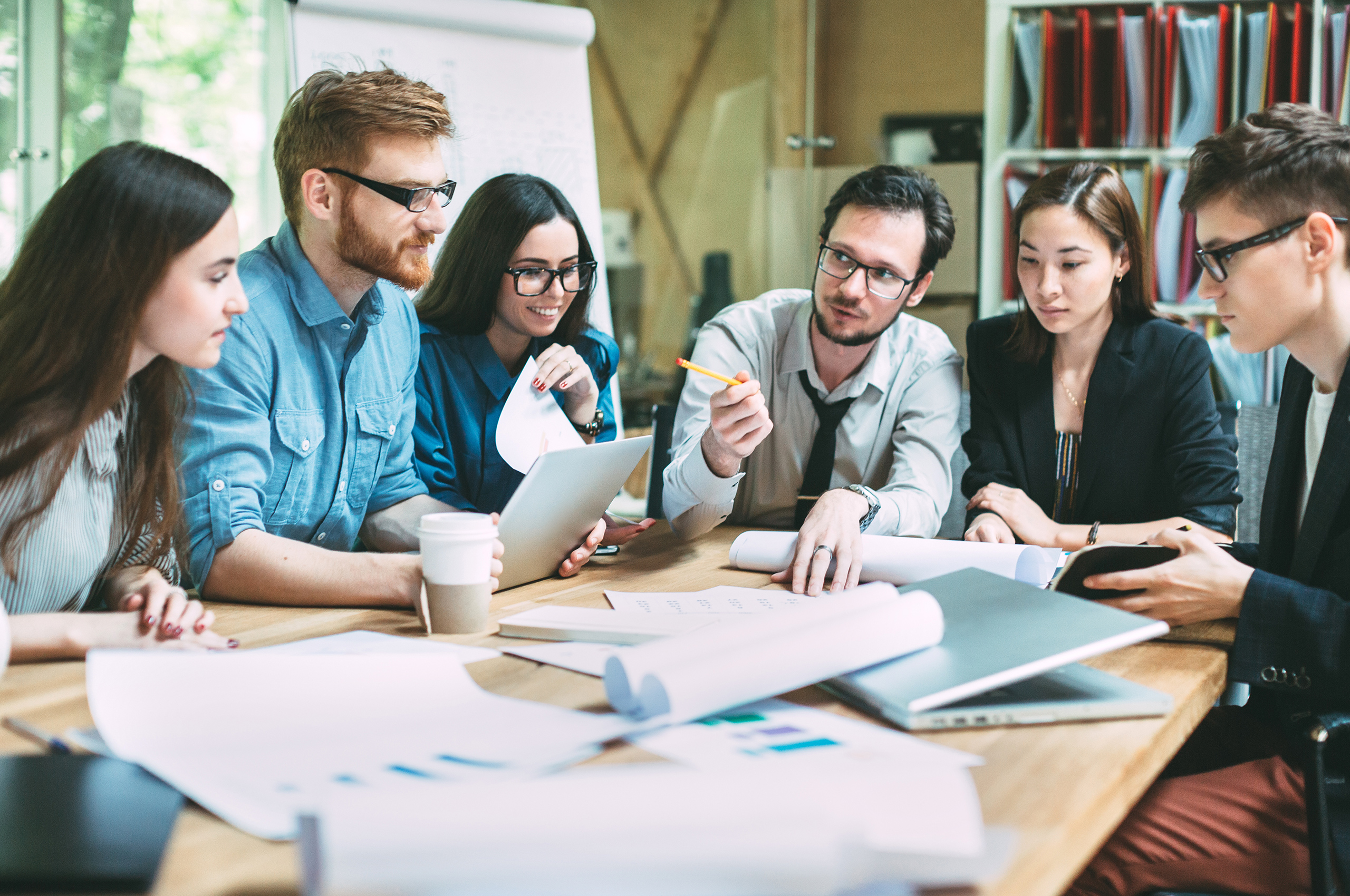
There’s nothing that can bring a business to grinding halt faster than lack of collaboration between different departments and poor visibility of processes within and between departments.
But creating a business plan that integrates all aspects of your organization can be challenging as each business process is often measured by its own, unique set of metrics, and some are more important than others, depending on which department is “running the metrics.”
For instance, while the demand forecast accuracy is a top priority for your supply chain managers, your procurement department may be more interested in reducing the price of raw materials, and your manufacturing division might aim to maximize its capacity utilization. Organizations with inconsistent planning practices risk running inefficiently, which can result in a substantial loss of time, energy, and money.
So, how do you align the many strategies, operations and functions from each of your departments to make informed decisions about market policies, investments, and even new product or service introductions?
One widespread method that is used to connect diverse business strategies is Integrated Business Planning (IBP). Developing and implementing an integrated business plan for your organization gives you a clearer understanding of your goals and how to plan to achieve them.
What is Integrated Business Planning (IBP)?
Companies have multiple operational functions – ranging from finance to supply chain, to product design and development, to marketing and sales, ad infinitum. By using IBP, you can link your strategic plans and be more aware of how resources, capabilities, and results relate to one another. This enables you to reach your maximum potential and enhance collaboration across supply chains.
With digitization driving success, IBP is becoming a “best practice” tool for business planning. From sales to operations to finance, data from every facet of an organization can be incorporated seamlessly. This method of incorporation allows companies to maximize output and understand how their resources, abilities, and outcomes are all working together. It also helps companies analyze what role each sector plays in the business.
Why Is Integrated Business Planning Important?
How can your business benefit from integrated business planning? Let’s take a look at a few benefits:
- Increasing visibility Organizations can integrate data from financial reports, supply chain projections, and strategic plans into their business plans using IBP. By doing so, businesses gain insights into how each part of the supply chain works both independently and collectively. As a result, it enables businesses to discover and resolve problems in an efficient manner.
- Increasing accountability With more visibility, employees are more plugged in and aware of the impact their actions can have on the business as a whole. This makes them more accountable and provides a clear understanding of exactly what their responsibilities are, which increases employee engagement and boosts compliance with processes and procedures.
- Aligning goals and actions An organization with visibility and accountability can get a clearer picture of what it is striving for and helps to ensure that everyone is taking the necessary steps to achieve it. In addition to enabling individuals to do their jobs more effectively, this will also allow the whole organization to run more efficiently.
- Allowing for better decision making An integrated business process enhances a company’s ability to evaluate data, the relevant context, and the big picture at the same time. By analyzing the results, they can make highly informed decisions based on the information they are presented with.
These benefits are desirable for any organization, but implementing integrated business planning successfully can be a complex process. Following best practices for IBP increases your odds of success and improves your outcomes.
Tips and Best Practices for Successful Integrated Business Planning
IBP is potentially valuable for your business. However, when you try to integrate additional functions and strategic planning into your traditional sales and operations planning (S&OP) cycle, it can initially lead to many challenges. Let’s take a look at a few tips for successful integrated business planning.
- Effective governance To make an IBP work, everyone needs to work together as a team and fulfil the company’s objective. Charting the roles and responsibilities of your employees and implementing policies and incentives to create an environment where everyone can work together can help improve team cohesion.
- Clear goal Start with a clear goal for implementing an IBP and how it will benefit your business (and individual contributors).
- Organized process When your process is already designed to align with your organization, it is easier to achieve the desired outcome.
- Right talent The backbone of an organization is its workforce. Choose your employees wisely; look for the skills, experience, and core competencies that are vital to IBP. You’ll need team members who are well-versed in strategic planning, financial planning, and supply chain planning. You will be able to more successfully adopt IBP across the company if you have talented and experienced people on board.
- Insightful analytics Businesses need to be proactive to remain ahead in their respective markets. Real-time analytics enables you to adapt swiftly to disruptions and market changes and make data-driven decisions based on your business strategy.
- Powerful technology Businesses are moving ahead with digital transformation. IBP, being a cross-functional initiative, needs a strong cloud-based technology platform to perform.
IBP has become an integral element of the day-to-day operations of many businesses, ensuring transparency and efficiency throughout the fast-paced supply chain right from procurement through manufacturing and delivery. As an increasing number of companies make the shift to digitization, the implementation of an integrated business planning (IBP) approach is vital.
Other articles you might enjoy
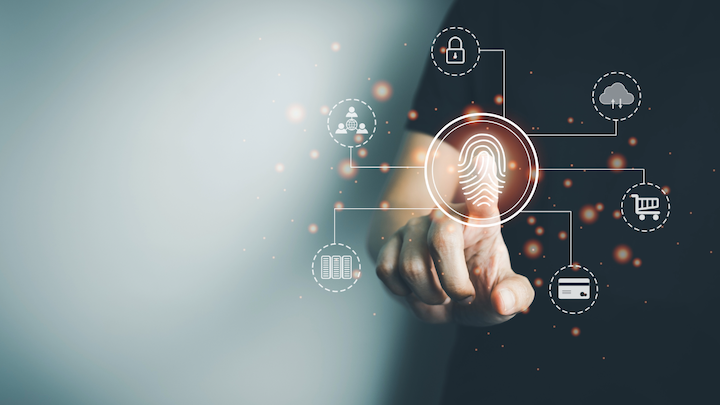
Strengthening Operational Resilience: A Use Case for IAM to...
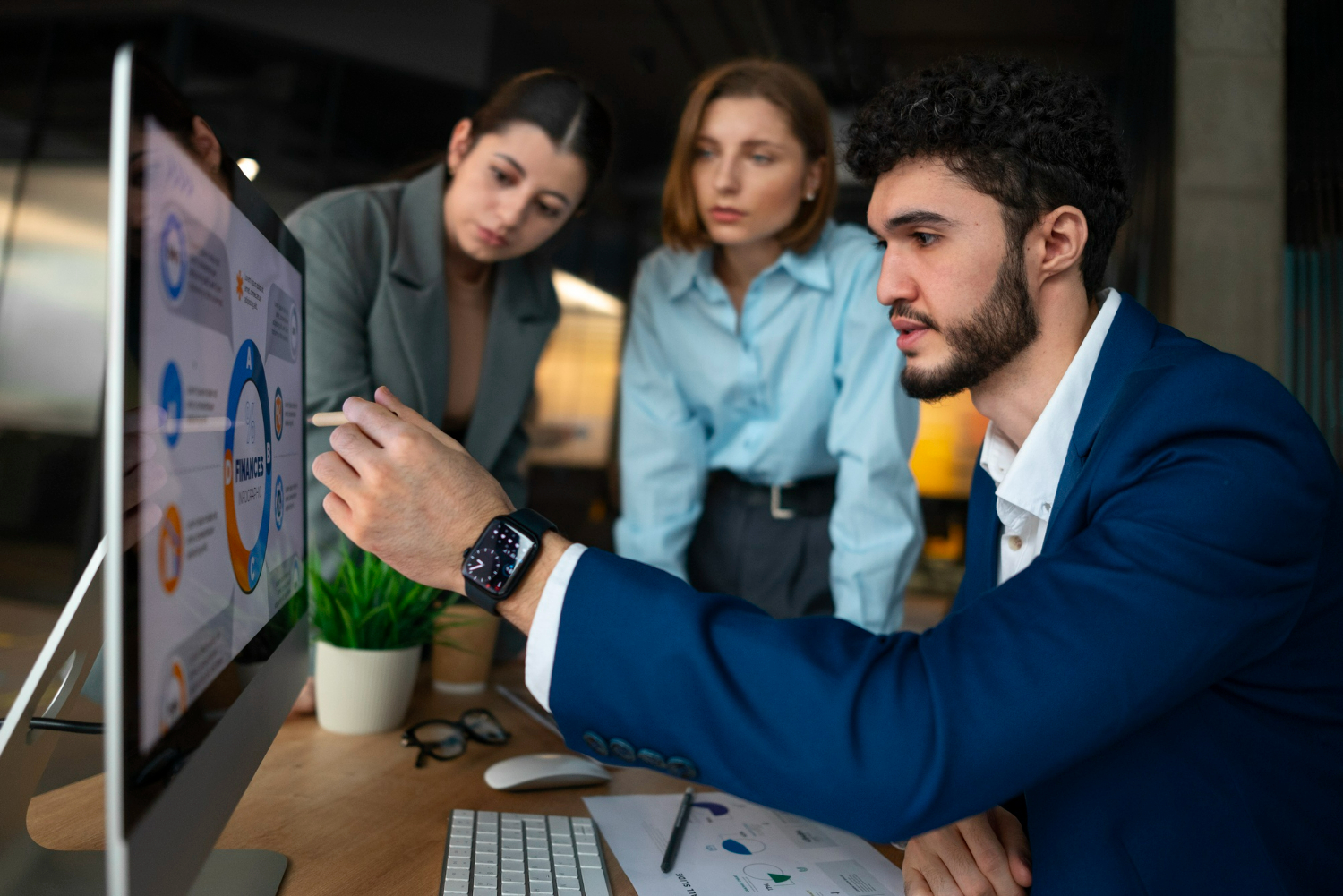
Why Use a Consultancy When Choosing a Sales Performance...
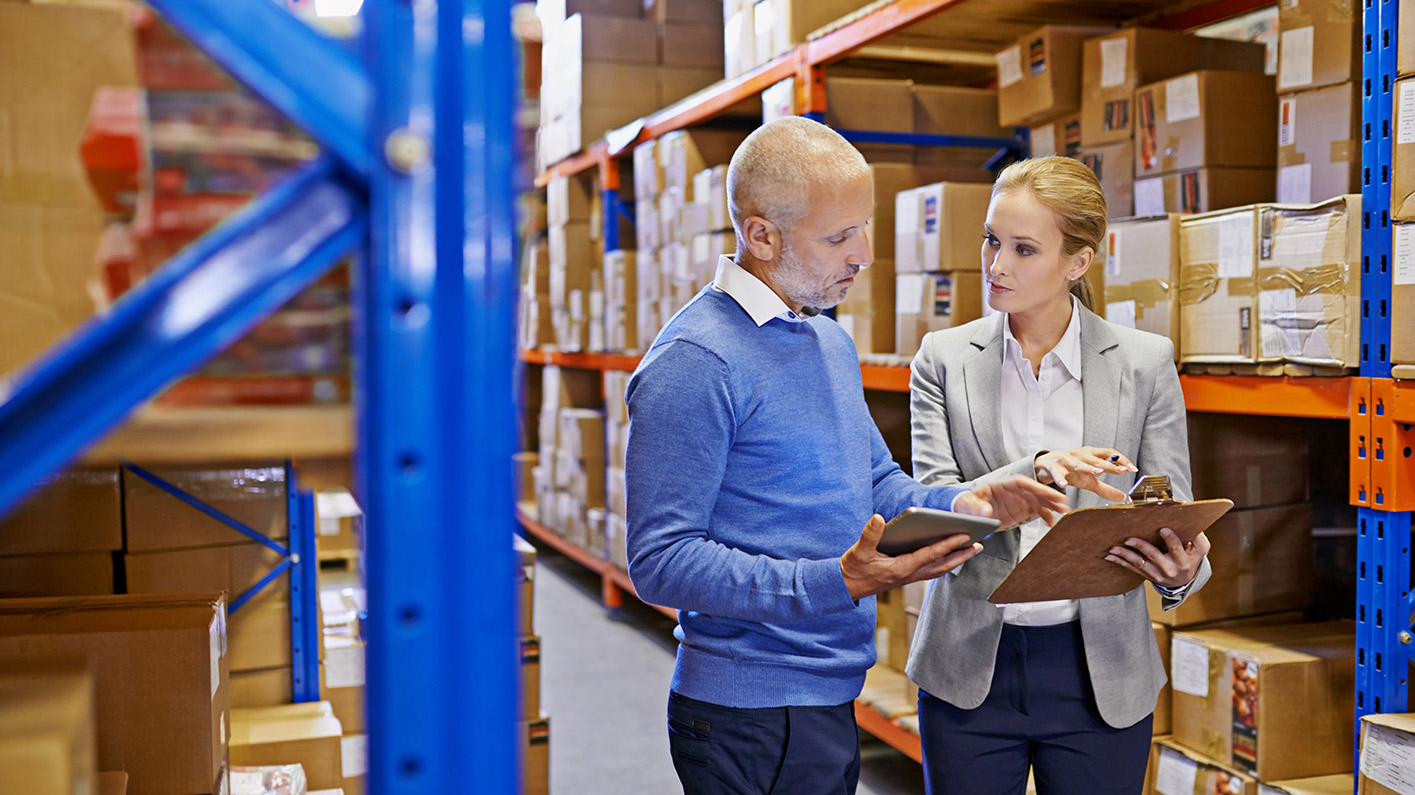
AI's Impact on Demand and Supply Synchronization: Is it a...
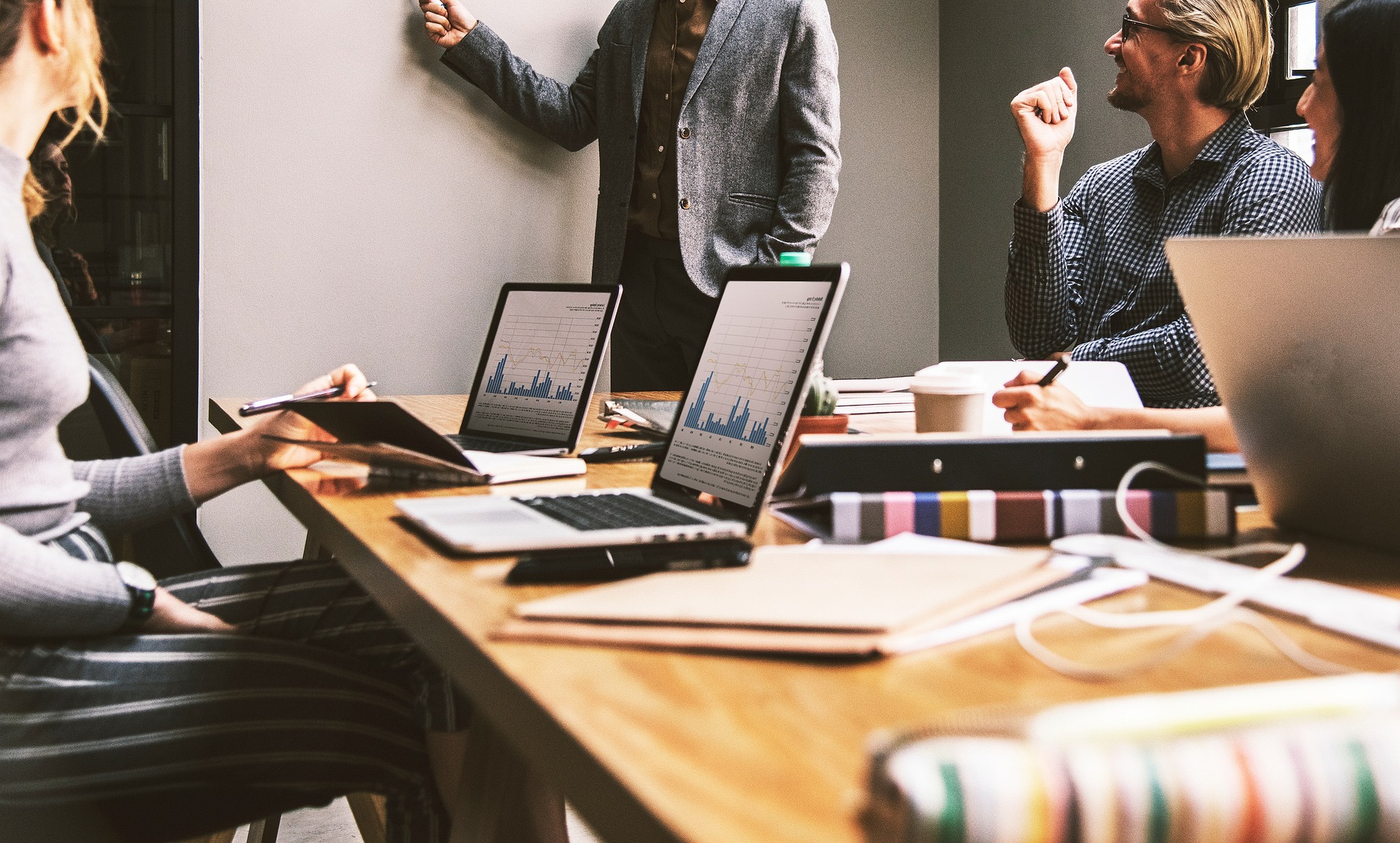
4 Signs Your Incentive Compensation Management Solution Needs to...

Digital transformation at the intersection of operations and technology
Subscribe for insights and updates
Copyright ©2024 Argano

- Group Training
- Individual Training

- Individual Certification
- Corporate Certification
- Companies Certified
- Testimonial
- Companies w/ Certification
- Levels of Certification
- Certification Details
- Sample Exams
- Recertification
- Preparation Materials
- Exam Schedule
- CPF Prep/Review

- Research Reports
- Virtual Conference Recordings

- Cancellation Policy
- Refund Policy for Events
- Ambassador Program
- Member Companies
- Partnership
- Apply to Speak
- Subscription
- S&OP Self-Assessment
- Sponsored Content
- Become a Sponsor
- Exhibit at IBF Events

What Is Integrated Business Planning (IBP)?
The term today is highly debated between two groups of practitioners: one defines it as the planning process that includes demand review, supply review, product management review, management business review, financial reconciliation, and business strategy. Some view IBP as a broader version of S&OP, which also emphasizes the role of strategic planning. It continues to evolve.
Business Partner Magazine
Tips and advice for entrepreneurs, start-ups and SMEs
5 Steps To A Successful Integrated Business Planning (IBP)
January 31, 2022 by Sandra Hinshelwood
Click here to get this post in PDF
Too long to read? Enter your email to download this post as a PDF. We will also send you our best business tips every 2 weeks in our newsletter. You can unsubscribe anytime.
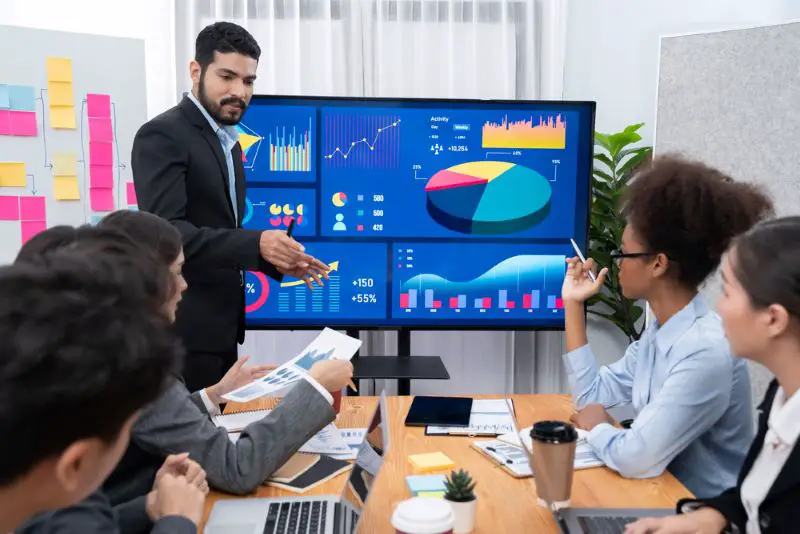
Integrated Business Planning (IBP) is a method for identifying the gap between company objectives and expected outcomes. IBP is a cyclic monthly procedure that enables collaboration planning and departmental alignment through cross-functional inputs.
While implementing IBP is a major organizational shift, much knowledge has been gained about the essential success elements. When planning the adoption of IBP, the finance function plays an important role.
Using specified company objectives, IBP develops accurate financial and operational resource requirements to minimize risk and maximize cash flow or profit . Sustainable growth in IBP refers to the maximum expansion rate a company can support without new funding, not to more significant environmental, social, and governance factors.
Which Businesses Can Use Integrated Business Planning?
Integrated business planning can assist any company, whether you’re a big company with many assets or a small business.
IBP isn’t prescriptive. It can be customized to your company’s needs. Regardless of size or complexity, an integrated business planning approach can align departments.
This article breaks down the IBP journey into steps. See the IBP process below:
1. Identify What Is Preventing The Company’s Success
The complexity of a company’s functions varies greatly.
A company’s finance process may never attain its full potential if it’s not connected with other financial operations. Process integration may be inadequate, causing a bottleneck that stops the company from realizing its full potential. Thus, the first step in the IBP journey is to identify the constraints limiting the company’s potential.
2. Create A Product Prioritization System
Profit and loss are crucial factors to consider when performing a project.
When IBP is enforced, only the initiatives that are assured to be profitable are funded. Similarly, products are ranked. A company may also have to discontinue a product line with minor growth prospects, even if it’s currently profitable.
When IBP is implemented, cost-benefit analyses (CBA) become critical. Project managers must first conduct CBAs to ensure that the estimated costs and benefits line with the company’s aims.
Using hit-and-miss strategies reduces overall business efficiency and boosts chances of success.
3. Ensure IBP Process Is On Track
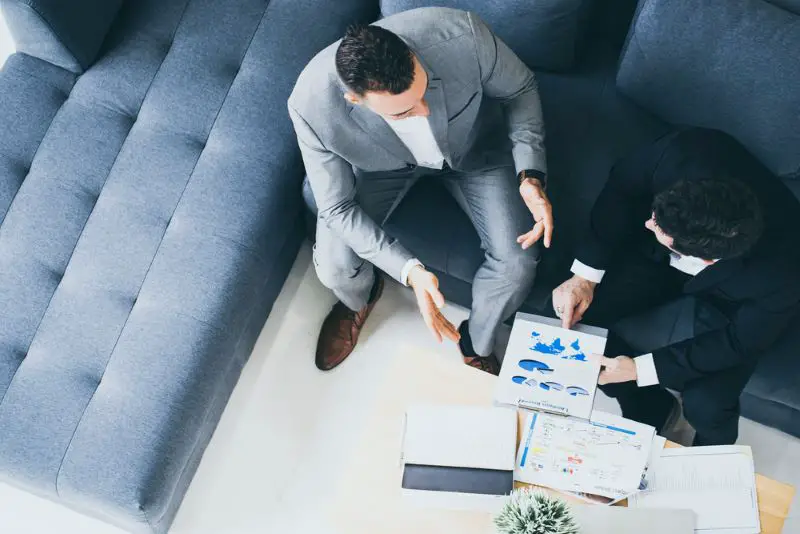
A strategically aligned IBP process can transform a firm. Rather than just balancing supply and demand predictions, IBP can assist professionals in making decisions that maximize overall corporate profit.
Once a company has defined goals, it must guarantee that they are being met. As a result, the business must regularly report on its progress to meet its deadlines and budget.
During this step of the IBP process, the organization has determined its skills. Some examples of these capabilities are as follows:
- Collaboration. Companies that realize the strategic advantage of collaborating with their suppliers and customers and combining their business plans can create a collaborative IBP phase. This is unlikely to be a strategic focus for organizations with supply chain dominance due to size or product distinctiveness.
- Risk management. This is for firms with extensive networks susceptible to global and geopolitical developments—for example, global supply chain companies and the finance industry.
- Innovation. Companies that can innovate and develop new products faster than their competitors in a highly competitive market are often seen in the tech industry.
- Knowledge management. For firms that rely heavily on knowledge employees and knowledge sharing between departments. Companies have IP to sell and protect. For example, consulting and software.
Once a corporation has determined its strategic competencies, it needs to implement or improve them. It will include an update on the plans’ status, risks, mitigations, and progress. The update provides sensitivity analysis around the techniques to achieve the strategic capability’s goals.
4. Set Common KPIs
Verify transparency of existing position and budget targets. Create cross-departmental key performance indicators (KPIs). Ensure that all parties agree on the definitions of these KPIs . This ‘good governance’ allows you to work towards similar aims. Transparency and confidence in information are improved. Assembling a ‘single version of the truth’ ensures a smoother planning process.
5. Adopt IBP-Supporting Technologies
Finance teams must have easy access to data from all operational areas. Rolling forecasts and better data usage require technology and transparency. You can’t manage well without the right tools. Modernize the planning process. Modern planning requires an IT-integrated planning solution to support all planning phases and provide reliable plan values and real-time analysis. For example, EPM software lets you assess, comprehend, and report on your business. It also encourages transparency, collaboration, and success across departments.
Conclusion
IBP is a continuous process that improves with practice. While IBP may not be flawless the first time around, it can be a very effective strategy for significantly improving business performance and establishing a durable competitive edge in the marketplace when adopted and managed well.
You may also like: The Perfect Software Development Process for Your Business
Image source: Depositphotos.com
We earn commissions if you shop through the links on this page.
Digital Marketing Agency
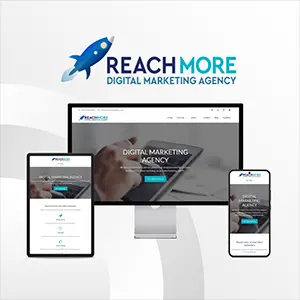
Business Partner Magazine provides business tips for small business owners (SME). We are your business partner helping you on your road to business success.
Have a look around the site to discover a wealth of business-focused content.
Here’s to your business success!

Small Business Glossary
Integrated business planning.
Integrated Business Planning (IBP) is a strategic approach that unites all the functional areas of a business to achieve a common set of goals . It is a holistic method that aligns strategic, operational, and financial planning to enhance business performance. In the context of small businesses in Australia, IBP is a critical tool that can help entrepreneurs navigate the complexities of the business landscape, streamline operations, and drive growth.
IBP is a dynamic process that requires continuous monitoring and adjustment . It is not a one-time event, but a cycle that involves setting objectives, planning, executing, monitoring, and adjusting. This iterative process allows businesses to respond quickly to changes in the market, seize new opportunities, and mitigate risks. The adoption of IBP can lead to improved decision-making , increased profitability, and sustainable growth .
Components of Integrated Business Planning
IBP is composed of several key components that work together to create a comprehensive business plan. These components include strategic planning, operational planning, financial planning, and performance management. Each of these elements plays a crucial role in the overall success of the IBP process.
Strategic planning involves setting the long-term direction of the business, including defining the vision, mission, and strategic objectives. Operational planning focuses on the day-to-day activities that support the strategic objectives. Financial planning aligns the financial resources with the strategic and operational plans, while performance management monitors and adjusts the plans based on actual performance.
Strategic Planning
Strategic planning is the first step in the IBP process. It involves setting the long-term direction of the business, defining the vision, mission, and strategic objectives. The vision sets out what the business aims to achieve in the long term, the mission defines why the business exists, and the strategic objectives outline the specific goals that the business needs to achieve to realise its vision.
In the context of small businesses in Australia, strategic planning can help entrepreneurs to identify their unique selling proposition, target market, and competitive advantage. It can also help them to navigate the complexities of the Australian business landscape, including regulatory requirements, market trends, and competitive forces.
Operational Planning
Operational planning is the second component of the IBP process. It focuses on the day-to-day activities that support the strategic objectives. This includes planning for production, sales, marketing, human resources, and other operational areas.
For small businesses in Australia, operational planning can help to streamline operations, improve efficiency, and reduce costs. It can also help to align the operational activities with the strategic objectives, ensuring that all areas of the business are working towards the same goals.
Benefits of Integrated Business Planning
IBP offers numerous benefits for small businesses in Australia. These include improved decision-making, increased profitability, and sustainable growth. By aligning strategic, operational, and financial planning, IBP can help businesses to navigate the complexities of the business landscape, seize new opportunities, and mitigate risks.
Improved decision-making is one of the key benefits of IBP. By integrating all areas of the business, IBP provides a holistic view of the business, enabling entrepreneurs to make informed decisions. This can lead to increased profitability, as businesses are able to identify and seize new opportunities, and mitigate risks.
Improved Decision-Making
One of the key benefits of IBP is improved decision-making. By integrating all areas of the business, IBP provides a holistic view of the business, enabling entrepreneurs to make informed decisions. This can lead to better allocation of resources, improved operational efficiency, and increased profitability.
In the context of small businesses in Australia, improved decision-making can help entrepreneurs to navigate the complexities of the Australian business landscape, seize new opportunities, and mitigate risks. It can also help them to respond quickly to changes in the market, ensuring that their business remains competitive and sustainable in the long term.
Increased Profitability
Another key benefit of IBP is increased profitability. By aligning strategic, operational, and financial planning, IBP can help businesses to streamline operations, reduce costs, and increase revenue. This can lead to increased profitability, which is critical for the survival and growth of small businesses.
For small businesses in Australia, increased profitability can provide the financial resources needed to invest in new opportunities, expand the business, and create jobs. It can also provide a buffer against economic downturns, ensuring that the business remains sustainable in the long term.
Implementing Integrated Business Planning
Implementing IBP in a small business involves several steps. These include defining the vision, mission, and strategic objectives; developing operational plans; aligning financial resources ; and setting up a performance management system. Each of these steps requires careful planning and execution to ensure the success of the IBP process.
While implementing IBP can be challenging, it can also be a rewarding process that leads to improved decision-making, increased profitability, and sustainable growth. For small businesses in Australia, IBP can provide a strategic framework that helps entrepreneurs to navigate the complexities of the business landscape, seize new opportunities, and mitigate risks.
Defining the Vision, Mission, and Strategic Objectives
The first step in implementing IBP is defining the vision, mission, and strategic objectives. The vision sets out what the business aims to achieve in the long term, the mission defines why the business exists, and the strategic objectives outline the specific goals that the business needs to achieve to realise its vision.
In the context of small businesses in Australia, this step can help entrepreneurs to identify their unique selling proposition, target market, and competitive advantage. It can also help them to navigate the complexities of the Australian business landscape, including regulatory requirements, market trends, and competitive forces.
Developing Operational Plans
The second step in implementing IBP is developing operational plans. This involves planning for production, sales, marketing, human resources, and other operational areas. These plans should support the strategic objectives and be aligned with the financial resources of the business.
For small businesses in Australia, this step can help to streamline operations, improve efficiency, and reduce costs. It can also help to align the operational activities with the strategic objectives, ensuring that all areas of the business are working towards the same goals.
Challenges of Integrated Business Planning
While IBP offers numerous benefits, it also presents several challenges. These include the complexity of integrating all areas of the business, the need for continuous monitoring and adjustment, and the potential for resistance to change. Understanding these challenges can help businesses to navigate them successfully and reap the benefits of IBP.
The complexity of integrating all areas of the business is one of the key challenges of IBP. This requires a deep understanding of the business, including its strengths, weaknesses, opportunities, and threats. It also requires strong leadership to drive the process and ensure that all areas of the business are aligned with the strategic objectives.
Complexity of Integration
In the context of small businesses in Australia, this challenge can be particularly daunting, given the complexities of the Australian business landscape. However, with careful planning and execution, it is possible to navigate this challenge successfully and reap the benefits of IBP.
Need for Continuous Monitoring and Adjustment
Another key challenge of IBP is the need for continuous monitoring and adjustment. IBP is not a one-time event, but a cycle that involves setting objectives, planning, executing, monitoring, and adjusting. This iterative process allows businesses to respond quickly to changes in the market, seize new opportunities, and mitigate risks.
For small businesses in Australia, this challenge can be particularly daunting, given the dynamic nature of the Australian business landscape. However, with a strong performance management system in place, it is possible to navigate this challenge successfully and reap the benefits of IBP.
In conclusion, Integrated Business Planning is a strategic approach that unites all the functional areas of a business to achieve a common set of goals. It offers numerous benefits for small businesses in Australia, including improved decision-making, increased profitability, and sustainable growth. However, it also presents several challenges, including the complexity of integration and the need for continuous monitoring and adjustment.
Despite these challenges, with careful planning and execution, it is possible to implement IBP successfully and reap its benefits. For small businesses in Australia, IBP can provide a strategic framework that helps entrepreneurs to navigate the complexities of the business landscape, seize new opportunities, and mitigate risks. It is a critical tool that can help entrepreneurs to drive growth, improve profitability, and ensure the sustainability of their business in the long term.
Start saving time today
Why waste time on financial admin when thriday can do it for you.
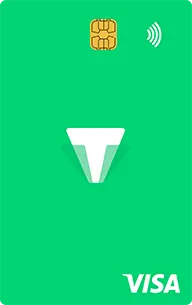
Thriday acknowledges the Traditional Owners of Country throughout Australia and recognises their connection to land, water and community. We pay our respects to them and their cultures, and to Elders past, present and emerging.
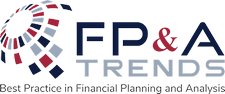
The FP&A Trends Webinar: Human & AI Synergy in FP&A
Click here to view details and register
By Dean Sorensen , Founder of IBP Collaborative
Integrated Financial Planning (IFP) and Integrated Business Planning (IBP) mean different things to different people. Primarily because there is no universal definition of what “fully integrated” processes entail. This article presents a maturity model to explain what it means and the capabilities that comprise it.
Introduction
What’s the difference between IFP and IBP? And how do IFP and IBP differ from the plethora of integration approaches and terminologies, examples of which are shown in exhibit 1? These questions were posed to me by a Vice President of Finance of a Global Manufacturing Company, hereafter referred to as Bob and GMC respectively.
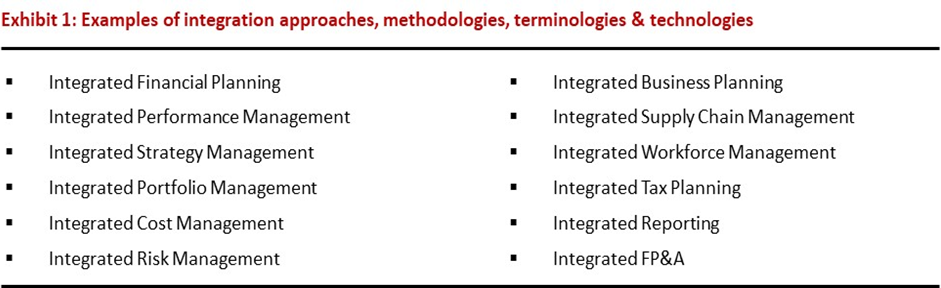
Why was Bob asking these questions? GMC had made significant investments in planning and performance management (P&PM) methods and tools. Despite these investments, capability gaps remained. GMC was still struggling to achieve the strategic, financial and operational (SFO) management objectives shown in exhibit 2. What Bob didn’t appreciate was that most of his [global manufacturing] peers were also struggling to achieve these interconnected objectives.
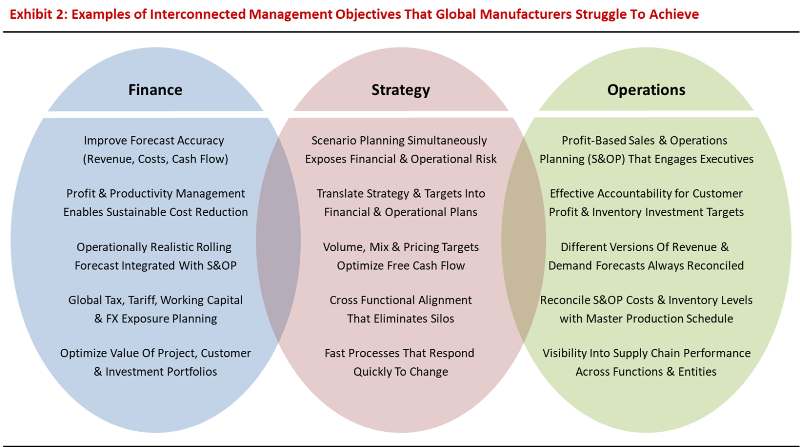
For Bob, the most glaring of these capability gaps was scenario planning. He envisioned an end to end scenario planning process that could answer interconnected questions, like those shown below in exhibit 3. This process would provide the basis to develop and deploy executable plans, while simultaneously optimizing free cash flow and exposing financial and operational risks.
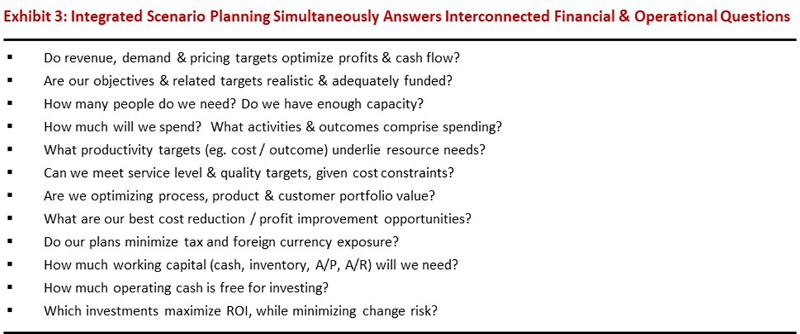
To Bob’s dismay, this vision never materialized. GMC’s rolling forecast process was only loosely connected to IBP and could only support the most basic forms of cash flow [and foreign currency exposure] forecasting.
Bob was frustrated by the situation. GMC had partnered with a large / leading software company (hereafter referred to as LSC) to avoid this very problem. LSC provided both IFP and IBP solutions, albeit by way of separate financial and operational P&PM applications. He assumed that the combination of the two would result in an integrated process that enabled GMC to achieve these objectives.
Questions & Complications
Bob now questioned the validity of this assumption. He wondered how LSC could be classified as a leader (by technology analysts) if they couldn’t support these SFO objectives. In light of this, Bob sought answers to 3 questions. First, what are “fully integrated” processes? Second, are our processes integrated? And third, what capabilities [that GMC could be missing] comprise fully integrated processes?
One factor complicates the ability to answer these questions. There is no universally accepted definition of what constitutes fully integrated P&PM processes and technologies. Which is one reason why terms like IBP and IFP are so liberally used. Another is that technology analysts still use separate maturity models to evaluate financial and operational applications.
There are two limitations of these technology-based maturity models. First, they aren’t industry-specific, so they don’t reflect unique needs of specific industries, like manufacturing. Second, they don’t recognize that SFO objectives [shown in exhibit 2] become highly interconnected as complexity increases. As a result, capability gaps in traditional financial and operational applications are not always exposed.
Question 1: What Are Fully Integrated Processes?
What’s needed is a more business-oriented maturity model. One that describes how integrated SFO process enable the achievement of one overarching business objective. That being, the ability to optimize the value of business outcomes for customers and stakeholders, across functions and entities.
Mature processes support this objective by enabling strategy and cost structures self-adjust to changing market conditions to achieve financial and operational performance targets. Two business capabilities play a central role in supporting such a process. They are explained below and form the framework for the maturity model shown in exhibit 4.
- Resource Quantification : Quickly and accurately quantify opportunities to optimize value [across functions and entities] while translating targets [eg. revenue, price, profit, cost, service and quality) into executable financial and operational plans for the outcomes and business processes that comprise customer value propositions. Further details of this capability are provided in a separate FP&A Trends article entitled “ Driver Based Planning Maturity ”.
- Profit & Strategy Alignment : Establish effective accountability, decision rights and rewards for managing key outcomes and tradeoffs that comprise customer value propositions and enterprise performance, while focusing and motivating people to behave and make decisions that optimize value for the organization as a whole, in both the short and long term. Further details of this capability are provided in a separate FP&A Trends article entitled “ Productivity Management ”.
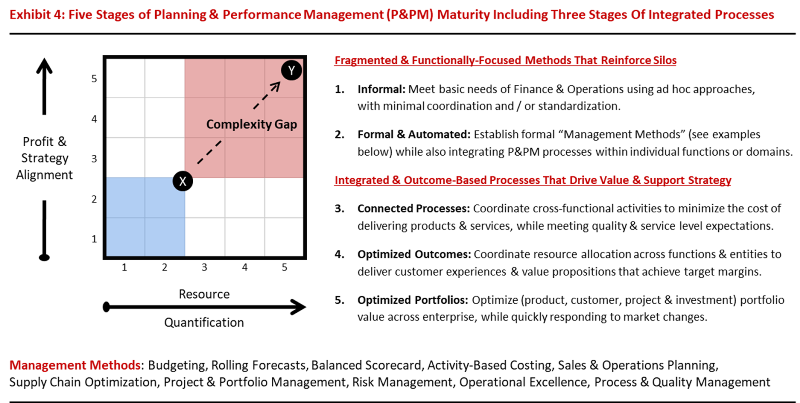
This model presents five stages of maturity across these two business capabilities. Stages 1 and 2 are the lowest level of maturity and are represented by the blue box in the bottom left corner. A key feature of stage 2 is the introduction of formal management methods and tools, examples of which are shown at the bottom of exhibit 4.
Stages 3 to 5 represent mature forms of integrated [and outcome-based] processes that are represented by the pink box in the top right. The hallmark of these maturity stages is improving the effectiveness of these management methods by embedding them into processes that integrate strategy, finance and operations.
Question 2: Do Our Tools Support Integrated Processes?
This maturity model provides the basis to answer Bob’s second question. The conclusion being that LSC did not support the integrated processes that GMC required, as denoted by Point Y on the chart.. It’s processes were stuck at stage 2, as denoted by Point X. Two primary factors led to this conclusion about gaps in GMC’s processes and tools.
First, LSC did not support mature planning models that could be shared by finance and operations, as defined in the “ Driver-Based Planning Maturity ” article. For example, it lacked a planning model that could support cash flow forecasting, profit-based sales & operations planning and scenario planning. This corresponds to a stage 2 maturity for Resource Quantification.
Second, LSC did not support cross-functional performance management, as defined in the “ Productivity Management ” article. For example, it didn’t support the capabilities defined as matrix planning and tradeoff management, which are stages 3 and 4 capabilities respectively. This corresponds to a stage 2 maturity for Profit & Strategy Alignment.
Bob was somewhat consoled by the fact that global manufacturers often experience this same “complexity gap”. It did much to explain why complex organizations, like GMC, struggled to execute against business objectives requiring superior cross-functional coordination. This includes operational excellence, profitable growth and sustainable cost reduction.
What it also helped Bob to understand is that, in mature processes, there is no distinction between IBP, IFP and other integration terms. There is simply an integrated P&PM process. To Bob, they now sounded like marketing hype that should be met with greater skepticism.
What Capabilities Comprise Fully Integrated Processes?
Bob’s third question was aimed at further understanding specific capabilities that comprised the gaps identified in exhibit 2. The capabilities that GMC lacked are identified below in exhibit 4 in the columns denoted as maturity levels 3 to 5.
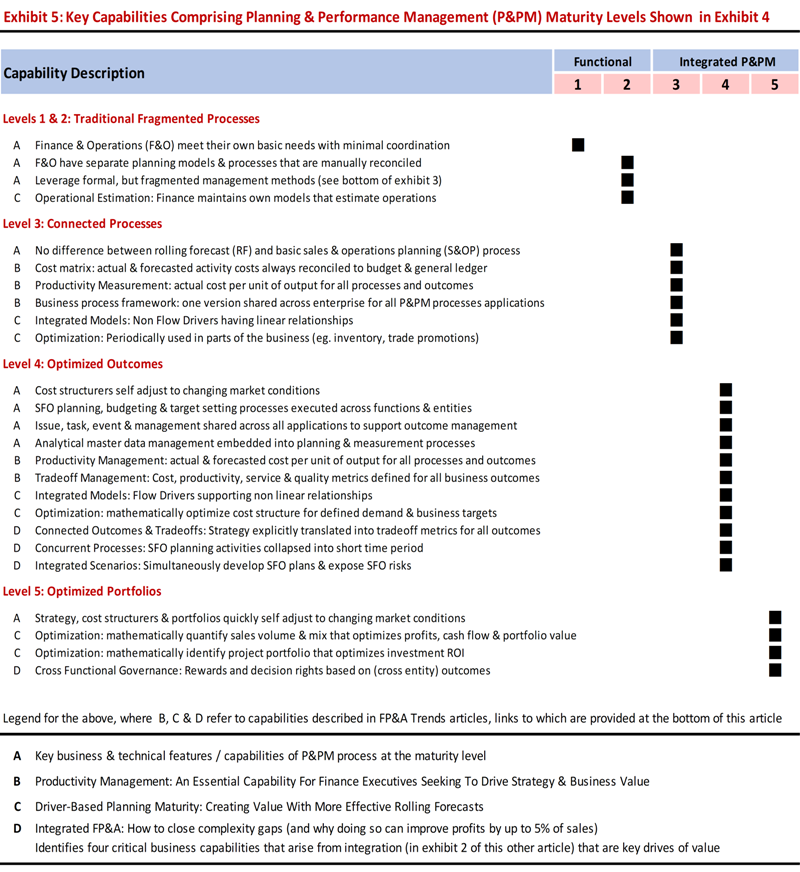
Details of the capabilities [shown above in exhibit 5] are contained in three separate FP&A Trends articles, links to which are provided at the bottom of this article. Each capability in the exhibit has a letter reference, which is described in the legend at the bottom of the exhibit. Three key insights can be gleaned from this exhibit:
- Specific capabilities [in stages 3 to 5] comprise the gaps of GMC’s processes
- Four of these capabilities [labelled “D”] are the primary gaps because they comprise the others
- The probability is high that these four capabilities are missing from IBP and IFP applications
This last point is of particular note. These four capabilities play a central role in helping global organizations manage complexity. Their absence undermines the ability to manage complexity costs. This is important because [as noted in the “ Integrated FP&A ” article] complexity costs can approach 5% of sales. In this context, these capabilities need to be a key focus of strategically focused finance executives.
Key Takeaways
Bob, like other forward-thinking finance executives, understood the importance of integrating SFO P&PM processes. Especially as a means of coping with complexity. Despite this understanding, GMC still failed to establish mature forms of integrated processes that could support their objectives. Here are four things you can learn from GMC’s experience that will help you to avoid these mistakes:
- Develop a healthy skepticism of IBP, IFP and other solutions, like those in exhibit 1. Many lack the capabilities to support mature forms of integrated processes.
- Employ a holistic approach for developing SFO P&PM processes. As GMC learned, failure to define integrated SFO processes and requirements at the outset, can lead to missed requirements and the capability gaps that they are now coping with.
- Consider the views of technology analysts, but remember that they view technologies from functional perspectives. Not from a process-driven one that brings together SFO perspectives. Without understanding this, their views can lead organizations in the wrong direction.
- Develop a shared understanding of what fully integrated P&PM processes look like, the specific capabilities that comprise them and why they are important for driving strategy and value.
This last point is especially important. Had GMC established such an understanding at the outset of their program, they could have avoided the situation in which they found themselves. In this context, the insights in this article can help to get you started in the right direction.
Related articles
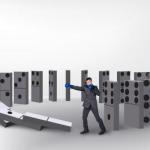
The cost of complexity can be significant – upwards of 5% of sales in global organizations. Forward-thinking...
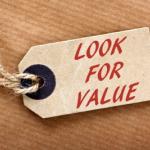
Mature driver-based planning models are an essential component of effective rolling forecast processes in complex, global...
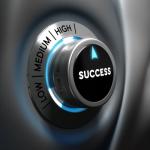
Managing enterprise productivity is an essential capability for value-focused Finance executives. It provides the basis for...
Subscribe to FP&A Trends Digest
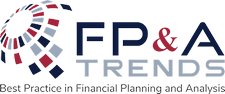
We will regularly update you on the latest trends and developments in FP&A. Take the opportunity to have articles written by finance thought leaders delivered directly to your inbox; watch compelling webinars; connect with like-minded professionals; and become a part of our global community.
Create new account
- Customer Portal
- Partner Portal
The Progression from Traditional S&OP to a Strategic IBP Process
Evolving traditional Sales and Operations Planning (S&OP) to a more strategic Integrated Business Planning (IBP) process has become critical to thrive in an increasingly complex and volatile global market. The shift from S&OP to IBP is not merely a change in terminology; it represents a fundamental transformation in how companies approach planning, decision-making, and collaboration across the organization.
Historically, many departments operated in silos, with supply chain, finance, merchandising, and other functions working independently. In our recent webinar: Aligning Strategic and Tactical Supply Chain Planning with Finance , our panel of supply chain experts discussed how these silos have to be broken down, and all stakeholders need to move together, not in isolation. IBP is the catalyst for this transformation, as it encourages a collaborative approach to planning that spans the entire organization.
The more advanced IBP process empowers companies to break down the barriers between different departments to foster a holistic understanding of the business landscape. This encourages cross-functional collaboration, enabling supply chain planners, finance experts, merchandisers and other key stakeholders in the organization to work synergistically towards common organizational goals. By improving alignment across the business and involving input from different perspectives in the planning process, companies benefit from more robust and resilient strategies.
What are the Key Differences Between S&OP and IBP?
When discussing the key differentiators between S&OP and IBP during the session, Richard Herrin, industry leader in advanced S&OP and IBP strategy, underscored a significant limitation of S&OP. He affirmed the traditional approach often fell short because it primarily focused on volumes and short-term objectives, while neglecting financial considerations. Richard noted: “9 out of 10 S&OP implementations never really delivered on the full promise, because it was just a volumetric exercise every month.” He then explained how IBP emerged as the solution to bridge these gaps, recognizing the need for a more comprehensive approach that integrates financial impacts into the decision-making process.
Rebecca Haerter, Vice President of Supply Chain at Full Compass Systems, elaborated on this, highlighting the tactical nature of S&OP, where the focus was on checking boxes without considering the broader consequences. In contrast, she said IBP promotes “great strategic discussions across the organization, with the key decision makers involved and aligned.” She added that in this process, the key decision-makers understand that the plan is only as good as its adaptability to changing circumstances.
The agility that IBP brings to the table is vital for businesses to adapt and remain competitive. It allows companies to shift inventories as market conditions change, avoiding the worst-case scenario where inventory is stuck in a declining segment while the business's growth drivers remain underfunded. The ability to adjust strategically and promptly to industry shifts is a game-changer, ultimately elevating revenue and margin.
In essence, IBP is all about collaboration. It brings together diverse teams and departments, fostering open and transparent discussions that allow for the best decisions to be made. As Rebecca mentioned, it's a process where individuals challenge each other's thought processes, bringing different perspectives to the table. This collaborative approach ensures that organizations can make the most informed decisions, adapt to change swiftly, and navigate the complexities of the modern business landscape successfully.
Watch the webinar to learn how your peers are making the most of advanced supply chain planning software to align operations across a robust IBP process: Aligning Strategic and Tactical Supply Chain Planning with Finance (johngalt.com)
Just for you:
Aligning strategic and tactical supply chain planning with finance.
In this webinar, we’ve brought experts to share their experiences aligning operations across a robust integrated business planning (IBP) process.
Leveling Up S&OP for a Well-Orchestrated Supply Chain
Download this ebook to assess the maturity of your S&OP process and explore steps to evolve your planning capabilities.
Featured Gartner Report
Discover how to unlock the full potential of S&OP with our guide on improving service, cost, inventory, and planning for supply chain leaders.
Ask the Experts: What is Your Favorite Scary Movie
Ask the experts: how does innovation impact the skills needed to excel in supply chain.
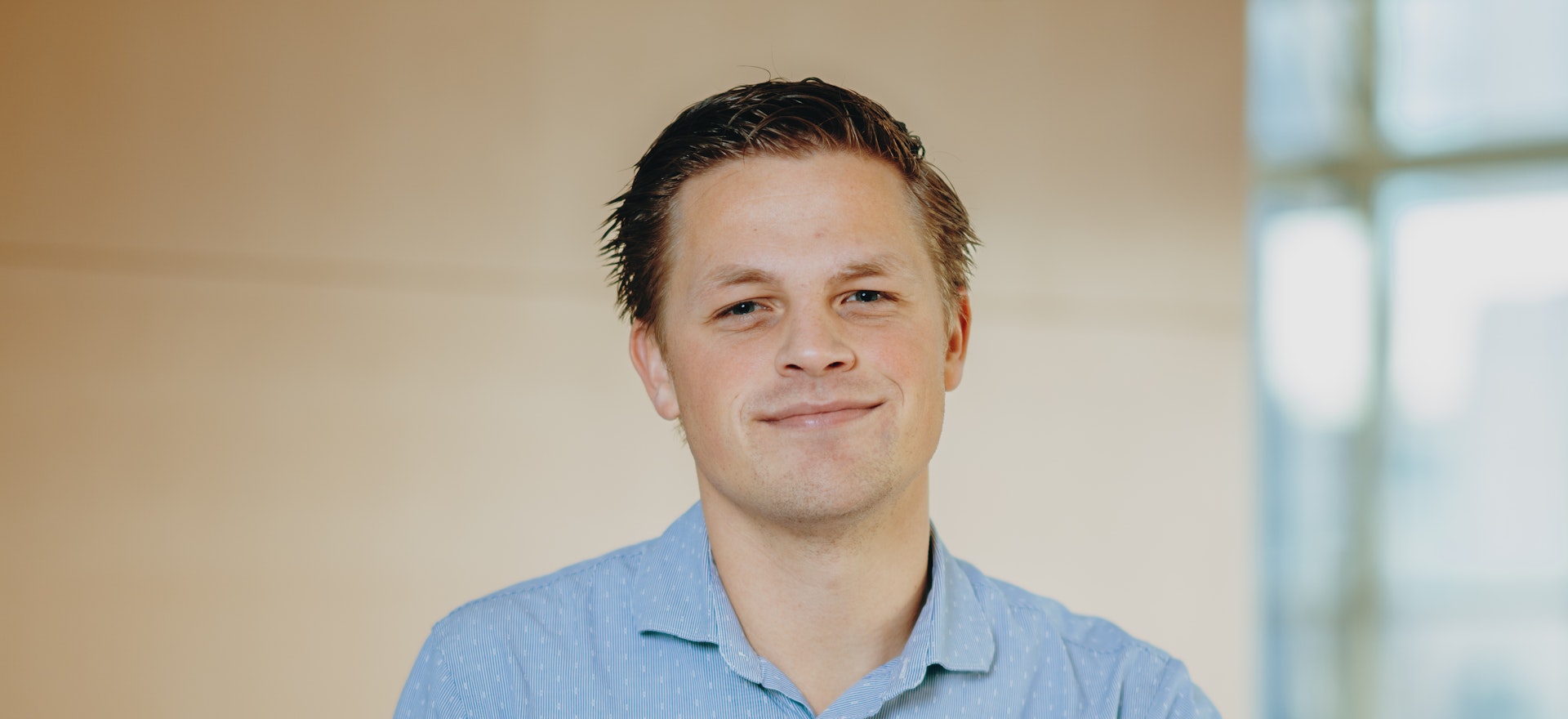
- Intelligent Planning using SAP IBP
- SAP Integrated Business Planning Explained
- The Perfect Planning Guard
SAP Integrated Business Planning Explained (SAP IBP)
SAP Integrated Business Planning (IBP) is a Cloud Based solution for supply chain planning designed to help companies streamline and enhance their planning processes. IBP provides a single platform for collaboration and data-driven decision-making, enabling companies to better respond to market changes and achieve their business objectives.
The IBP solution consists of six components that cover all processes within the supply chain.
Supply Chain Control Tower
IBP for Sales & Operations Planning
IBP for Demand
IBP for Response & Supply
IBP for Inventory
Demand-Driven Replenishment
SAP Integrated Business Planning is the successor to SAP APO (Advanced Planning and Optimization) . Where SAP APO primarily focused on optimizing supply chain planning, SAP IBP goes further, providing a more comprehensive and advanced solution for planning and managing the supply chain in one solution.
Supply Chain Challenges
In your company, there are many departments involved in making the planning successful: demand, supply, marketing, finance, management... and they all need to be aligned. However, this is very difficult if you do not have a system that can give everyone a voice.
In addition, you also need to take into account different perspectives: strategic, tactical and operational. The strategic level sets directions and goals for the long term, the tactical level creates aggregated plans to meet the strategic objectives, balances demand and supply, optimizes inventory and creates allocations. And finally, the operational level translates the aggregated plans into detailed plans for the short term (such as priorities for deliveries or confirmations).
Inhoudsopgave
Advantages of sap ibp, sap ibp consultancy.
SAP IBP Releases
Other SAP IBP Content
Ibp for s&op.
In today's rapidly changing world, it is more important than ever for companies to have a clear understanding of demand and supply. With the right planning tools, companies can ensure that they have the right products in the right place at the right time to meet customer demand.
The main component, S&OP (Sales and Operations Planning), helps companies optimize their demand and supply planning processes. The solution provides a single, integrated view of demand and supply data, enabling companies to make better decisions.
As companies can see all relevant data in one place, it becomes easier to see the bigger picture and identify potential problems or opportunities. S&OP is built up of four phases:
Demand review
Supply review
Reconciliation review
Management Review
This way, the solution helps companies make accurate demand forecasts. S&OP uses six different forecasting techniques to make accurate demand forecasts, even in dynamic markets. It also helps companies determine how much they can produce, which raw materials they need, and when they need to purchase them. IBP optimizes supply-side planning to meet demand, taking into account factors such as lead times, costs, and risks. S&OP also offers scenario planning capabilities, meaning companies can create and test different scenarios to see how these would affect demand and supply.
This allows for responding to unexpected events or changes in the market. In the fourth phase of S&OP, it can be determined whether the submitted proposal is in line with the financial objectives and key performance indicators of the company.
Curious about more information on the S&OP module, check out the McCoy TV below.
SAP IBP for Demand
It is crucial for many companies to understand the demand for their products and services. When a company can understand its demand patterns well, it can ensure that it has exactly the right amount of products and services to meet customer demand.
The SAP IBP for Demand module can play a key role in this by supporting companies in optimizing their Demand planning processes. With a range of features and benefits, this solution enables companies to make better-informed decisions about their operations. The SAP IBP for Demand module goes beyond S&OP in demand forecasting and uses advanced algorithms to generate even more accurate demand forecasts. By leveraging these powerful algorithms, companies can benefit from improved accuracy and reliability in anticipating demand patterns. SAP even allows the user to apply external algorithms (from, for example, Python) , which further expands possibilities.
The ability to improve forecasts together is a central benefit of SAP IBP for Demand. Different teams can work together to refine forecasts, allowing input from different departments to be integrated.
These collaboration capabilities lead to more accurate and realistic forecasts, enabling companies to respond more flexibly to changing market conditions.
Also, demand planning with SAP IBP makes 'demand sensing' possible. This provides deep insight into order patterns, allowing companies to refine their forecasts based on historical and current order data. By understanding these patterns, organizations can better respond to specific customer requirements, adapt to changing trends, and above all, optimize their demand forecasts.
Digital Supply Chain Planning Made Easy
An e-booklet
The term "Dynamic market" is one that has been mentioned more and more often in the last 20 years. Demand fluctuations, supply chain disruptions, and unforeseen events require flexible and proactive planning.
The Response & Supply (R&S) module of SAP IBP offers the possibility to deal with these in the supply chain, to optimize it, and to anticipate changing market conditions in this way.
In this way, demand and supply can be synchronized. With the help of advanced algorithms and real-time data insights, the module enables the user to optimize their supply chain. It enables planners to apply Multi level supply planning. In this way, an effective supply plan for the entire network can be created by modeling across locations and multilevel bill of materials. This enables the planner to decide what should be included in the model and where the supply plan should be limited. Within R&S, three algorithms are available including the unlimited heuristic, prioritization, and optimization. The prioritization and optimization algorithms ensure that the system delivers a feasible and constrained supply plan that takes into account the modeled constraints.
Another strong part of Response & Supply is that it can reduce supply chain risks through tactical rough cut planning. R&S makes it possible to balance demand and supply while taking material constraints into account. Planners can impose constraints on essential resources such as production, transport, and storage, preventing potential bottlenecks.
It also enables the user to act flexibly through operational response management. For example, it becomes possible to tackle challenges related to material scarcity by using an operational supply plan. This allows supply allocations to be made when material is scarce and sales orders to be reconfirmed to determine realistic availability dates with the delivery run.
The user also gets the opportunity to set up an internal deployment plan based on controlled quantities available for deployment, allowing for prioritization and optimization. With operational response management, 'gating factors' can be investigated, providing insight into the main causes of delays and shortages. The user can then use the web-based interactive planning to adjust the plan and work in a targeted manner. This approach promotes the company's agility and prepares it for success in a dynamic environment.
SAP IBP for Inventory
Efficient inventory management is no longer a strange wish in a world where markets are constantly changing, competition is increasing, and costs are rising. For this, companies strive for enough inventory (of the right materials) to guarantee service levels and at the same time not too much inventory to minimize inventory costs.
IBP for Inventory optimization (IO) provides a solution for optimizing inventory levels and achieving high service levels at the lowest possible costs. With the help of advanced algorithms, IBP IO calculates the optimal inventory levels based on various parameters, such as demand variability, service levels, and costs.
Companies are thus enabled to improve their inventories by looking at the whole supply chain, different situations, and types of customers. This allows them to find the right balance between inventory investments and service levels.
SAP IO has a Multi-stage inventory optimization that effectively deals with these problems by buffering errors in the forecast, demand risks, and efficiently managing the uncertainty in the supply chain. This way, the right quantities of inventory can be calculated for different products from finished product to raw material and it can be analyzed how these influence each other.
Because IBP is one integrated solution, it enables companies to collaborate with all departments and suppliers to avoid too much inventory, guarantee service levels, and optimize inventory costs. IO component enables planners to tackle complexity and various constraints, such as service level objectives, batch sizes, and lead times. By using simulations and scenarios, planners can assess the impact of different decisions and constraints.
IO also makes it possible for companies to gain insight into the product network and the geographical distribution of the inventory through built-in analyses. This insight allows IO to enable the user to evaluate causes of inventory levels and take targeted measures to minimize inventory costs and guarantee service levels.
The supply chain control tower can be a great addition to all the components discussed above. The name Control Tower somewhat implies the function of this IBP component. It gives you a complete picture of your digital supply chain, shows how different domains are connected, and allows you to easily navigate to other parts of SAP such as SAP S/4HANA and SAP Digital Manufacturing Cloud. The Control tower also addresses the lack of visibility in your entire network. It provides end-to-end monitoring of the supply chain by analyzing current and historical performance, it creates alerts to quickly identify potential problems, it enables you to set up procedure playbooks to follow procedures, view supply network lanes, it offers dashboards with KPIs and intelligent tools for managing custom alerts and issues within the supply chain, and offers the ability to use analyses to address problems in your supply chain.
Another major benefit of the Control tower is that it connects you to your external supply chain partners via the SAP Business Network. This allows you to plan better by taking into account the constraints of your suppliers and quickly respond to alerts. This results in cost savings and improved service levels within your entire supply chain thanks to a responsive planning approach made possible by the Control tower.
Finally, the IBP for Demand-Driven Replenishment calculates decoupling points, average daily usage, and buffers for the positioning and sizing of materials to enable the material flow through your supply chain.
DDMRP (Demand Driven Material Requirements Planning) is an advanced planning technique that helps companies effectively manage their inventory levels. Unlike traditional planning systems, DDMRP uses actual demand data instead of forecasts to drive demand-driven replenishment. This ensures better planning accuracy and prevents over or under stocking. DDMRP uses five core components:
Strategic inventory positioning: determines where decoupling points are placed to position inventory at strategic points in the supply chain.
Buffer profiles: defines the required protection at decoupling points to absorb fluctuations in demand and supply. It uses a color-coded buffer model with different zones.
Dynamic adjustments: ensures that buffers can be flexibly adjusted based on market changes and future events. This keeps the inventory level protection optimal.
Demand-driven planning: uses sales orders instead of planned orders to drive demand planning. This ensures better accuracy in planning and prevents overstocking.
Visible and collaborative execution: priorities are assessed, inventory forecasts are checked and custom alerts are checked to manage the execution of the supply chain. Dashboards in SAP IBP provide an overview of the results and analyses.
With SAP IBP, companies can implement DDMRP and benefit from better inventory balance, increased operational efficiency, and improved customer service. DDMRP helps companies reduce the bullwhip effects, optimize inventory levels, and improve the overall performance of the supply chain.
In addition to the six main modules, IBP offers even more advantages. It is a cloud-based platform that runs on SAP HANA, which ensures easy integration with other SAP systems, but can also receive data from various sources at an aggregated or detailed level. Best practices are followed during integration, but on the other hand, it is also a scalable and flexible model.
The user experience is optimal thanks to the Web UI and Excel UI. Planners can create various "what if" scenarios and perform simulations that aid in the decision-making process. All results and information can be viewed in customizable charts and dashboards, and any required KPI can be calculated. And the best part is that it's not a static system, as it follows a roadmap with constant improvements.
As McCoy, we have a team of SAP IBP experts for all your planning issues. Our goal is to help you increase your revenue, reduce your inventory, and work more efficiently by using reliable and always available data. Continue reading to discover how we do this.
SAP IBP Releases Updates
SAP IBP releases quarterly updates to ensure that the platform remains up-to-date with the latest features, improvements, and bug fixes. These release updates provide users with new capabilities and improved performance, enabling them to manage their supply chain planning processes even more effectively.
We have listed some of the releases for you with the most important updates:
SAP IBP Release 2305
SAP IBP Release 2205
SAP IBP Release 2111
SAP IBP Release 2108
SAP IBP Release 2105
SAP IBP Real-Time Integration
SAP IBP Intergation with Transportation Management
Make Digital Supply Chain Planning work for your business
Case study ibp inventory, why is ibp for inventory the best solution for your inventory planning, perfect planning guard, how to improve your planning results by 5-10% more let us explain the perfect planning guard, watch all our sap ibp video's on mccoy tv, everything you need to know.
Introduction to Integrated Planning
After completing this lesson, you will be able to:
- Outline processes covered by SAP Integrated Business Planning for Supply Chain solution
Introduction to Integrated Business Planning and SAP Integrated Business Planning for Supply Chain
The current lesson outlines the structure of the course presenting every unit as a milestone. Every unit refers to a macro process of Supply Chain Planning. Further, Integrated Business Planning is explained as a general term within Supply Chain Planning. Integrated Business Process refers to a business process used to address supply chain challenges, risks, and opportunities.
The second unit addresses Integrated Planning Processes within the previous definition, answering the question - "how can we integrate business processes in Supply Chain Planning via SAP Integrated Business Planning?".
Next unit three, presents important SAP IBP functionalities to achieve a professional user experience, such as
- Managing Master Data via MS Excel and the SAP Fiori Launchpad
- Analytics and Dashboards supported by the SAP Fiori Launchpad
- Analytic Stories supported by the SAP Fiori Launchpad
- Planning Workspace via the SAP Fiori Launchpad
Within Supply Chain Planning, the most common challenges occur when companies focus their efforts on integrating functional Planning areas. Integrated Business Planning, as a general term within Supply Chain Management, refers to macro processes such as Demand Planning, Inventory Planning and Optimization, Supply Planning, and Exception Management. This course connects a professional user experience with these as explained unit by unit as follows:
SAP IBP addresses every macro process listed before, that is, it combines Supply Chain monitoring, Sales and Operations Planning, Demand Management, Inventory Planning, and Supply Planning into a comprehensive solution, which also supports the integration of data from external systems such as SAP ERP or SAP Advanced Planning and Optimization. SAP IBP provides applications to facilitate the following key differentiators:
Balancing of demand and supply
Harmonization of Planning across corporate functions through organizational visibility and alignment
Responsive Planning with advanced algorithms, optimization, and what-if scenario simulation Planning
Demand-driven Supply Chain Planning based on Demand Sensing, analysis, and predictive forecasting
Multi-stage Inventory Optimization and improved customer service levels
End-to-end Supply Chain visibility with real-time monitoring, Analytics, alerting, and exception management
Creation of product allocation and supply plans, and ability to respond to changes with simulations and gating factor analysis
SAP Learning System Access
If you have an active subscription to the SAP Learning Hub, you can also select an SAP IBP system to practice the course exercises using the following link.
Log in to track your progress & complete quizzes

Sales & Operations Planning vs Integrated Business Planning
The sales and operation planning (S&OP) process has been around for a long time. For those that have successfully put S&OP into practice, there have been measurable benefits. However, many organizations struggle with putting the plan into action. In fact, there is surging interest in the idea of S&O E with the “E” representing execution instead of “planning”. The underlying challenge of this segment is that they are done with “planning” for S&OP, they must get a workable, repeatable process completed.
Others are moving beyond S&OP and into integrated business planning (IBP). Let’s take a moment to consider the differences between S&OP and IBP. After all, S&OP and IBP have similar foundations and the lines between the processes can be blurred.
S&OP is primarily focused on the sales and operations functions of the organization, while IBP encompasses the entire enterprise. IBP aims to align all aspects of the business, including finance, marketing, human resources and supply chain.
S&OP typically has a shorter time horizon, typically 12-24 months, while IBP usually operates on a longer time horizon, spanning three to five years.
S&OP is usually a monthly process, while IBP is often done quarterly or annually.
Decision-making
S&OP is typically used to make tactical decisions about demand and supply planning, while IBP makes more strategic decisions about resource allocation, risk management, and business performance.
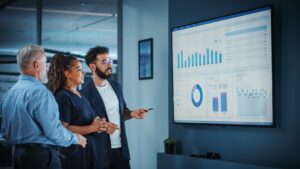
Information and Analytics
IBP involves more comprehensive data gathering and analysis, including financial and operational metrics, scenario planning, and risk management. S&OP typically focuses more on demand and supply data.
Using information from across all business units allows for the identification of gaps in process/revenue objectives, options to address these gaps and ultimately a plan to close them. This is done by running simulations and asking “what-if” scenarios to determine risks and outcomes.
Stakeholder Engagement
IBP typically involves a wider range of stakeholders, including executives, functional leaders, and external partners. S&OP is more focused on the sales and operations teams. Additionally, the ownership of the IBP process tends to be in the “corner office”. For S&OP, the ownership is usually at the manager/functional owner level.
IBP is not for everyone. The level of organizational engagement and commitment is high and there may not be a pay-off in terms of the level of effort vs. benefit. If the items below are true for your business, an IBP plan may be right for you.
Multiple Business Units
For organizations with multiple business units and different products, services, and markets, IBP can help ensure that resources are allocated effectively across the enterprise. It also ensures alignment with the overall business strategy.
Complex Supply Chain
When an organization has complex supply chains and multiple suppliers, manufacturing facilities, and distribution channels, IBP can ensure that supply and demand are balanced, risks are managed, and resources are optimized.
Global Operations
IBP can help ensure that local market conditions and regulations are factored into the planning process and that resources are allocated effectively across the global enterprise.
Long-term Planning
IBP can help ensure that the supply chain strategy is aligned with the overall business objectives and that the resources are allocated effectively to achieve those objectives over a longer time horizon.
Comprehensive Analytics
IBP can help provide a more holistic view of the business, including financial and operational metrics, scenario planning, and risk management that feed into strategic decisions.
Understanding the appropriate approach to planning for your business is a good starting point. Before moving into action, it makes sense to understand your readiness to undertake S&OP/IBP. A few years back, Gartner benchmarked an S&OP maturity scale. The steps in this progression begin with no plan to enterprise-wide coordination.
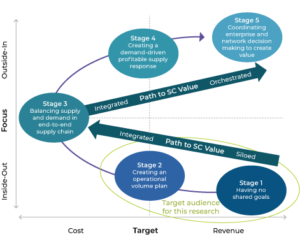
Click to enlarge
Moving up in scale comes down to the typical levers of people, processes and technology. Stages 1 and 2 are more dependent on people and processes. The movement to stage 3 and beyond requires some technological assistance. Especially for larger and more complex supply chains.
Regardless of where you are on this maturity scale, ask yourself these questions:
- Who stands to benefit from implementing/improving your planning process? These are the individuals who need to be engaged/brought into the initiative. As a supply chain leader, your focus may be heavily operational (as in moving inventory from A to B), but do the finance or product teams benefit? The answer is probably yes. Do not overlook them as they can be advocates for change.
- Where is your organization going to be in 5 years? How important are sustainability or streamlined operations? Align your plans with the corporate vision (which is a large IBP stepping stone).
- Perhaps the trickiest change is understanding the person who owns this initiative. It’s OK to have multiple people involved in the process, but there must be one person singularly responsible for the planning and outcome of S&OP/IBP. Multiple owners will bog this initiative down and muddy the results.
Given the level of effort involved in this, the final question is, is S&OP or IBP worth it? Here is a sampling of 40 clients from Colleen Crum at Oliver Wight, a leading consulting firm in integrated business planning on the range of improvements for those that embarked on an IBP journey:
- Increased demand plan accuracy by 18-25%
- Increased sales revenue by 10-15%
- Increased on-time delivery by 10-50%
- Inventory reduction by 18-46%
- Safety stock reduction by 11-45%
- Increased productivity by 30-45%
What if a company can improve its performance by the above amounts? What would be the impact on financial performance and/or customer satisfaction?
A study by Aberdeen Research sheds some light on the answers to previous questions. The following show results documented by companies using IBP, categorized by best-in-class, industry average and industry laggards.
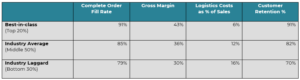
As you can see, the business case is there. All it takes is the vision and drive to get moving. If you are not moving forward, you risk going backward. If you need a little push to get going, contact Arkieva. Our team would be happy to discuss your current state and objectives and add to the business case you need to make.
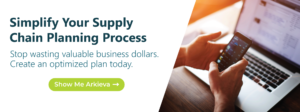
Share This Article.
About the author: jon cohan.
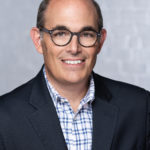
Related Posts

Unwrapped: What You’ll Take Away from the 2024 Gartner Supply Chain Symposium
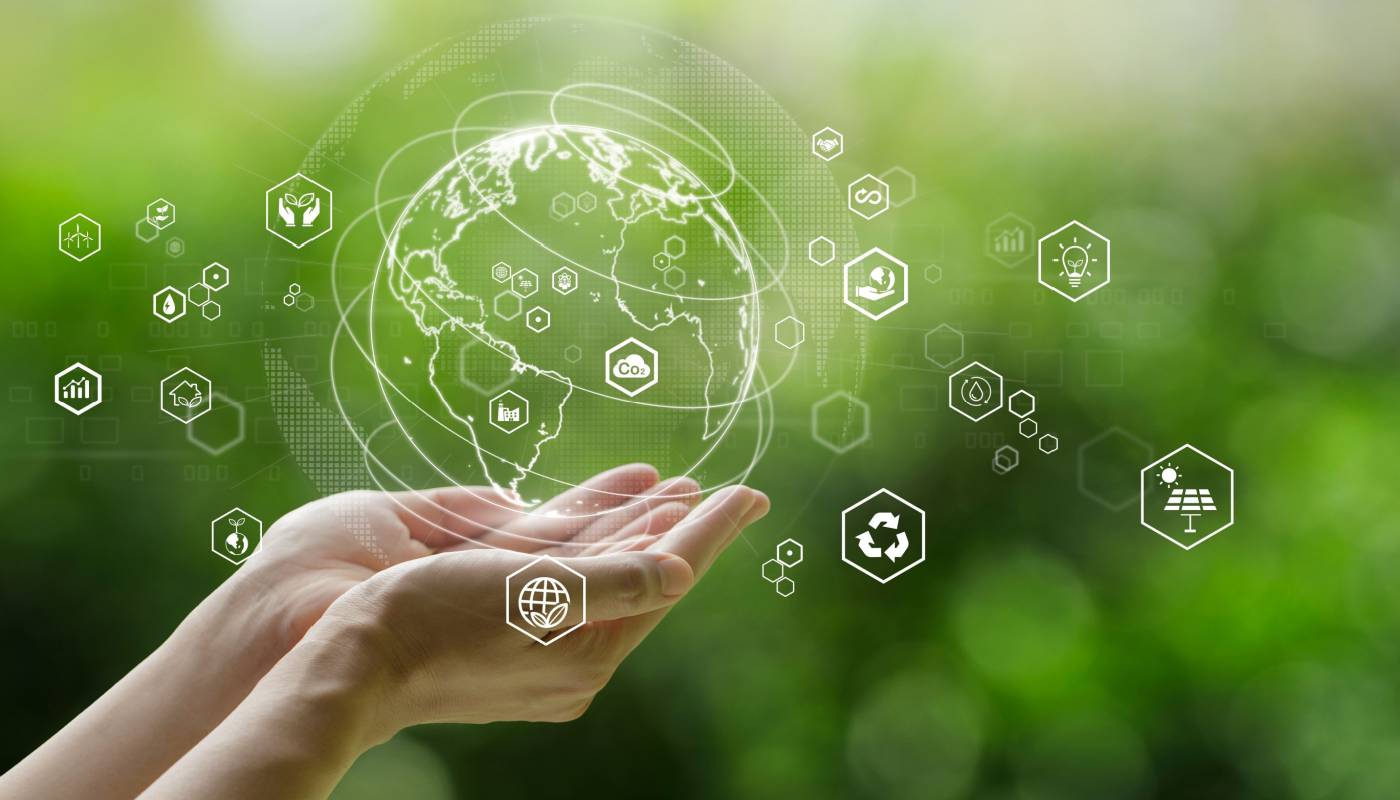
The Latest R in Sustainability: Reshoring
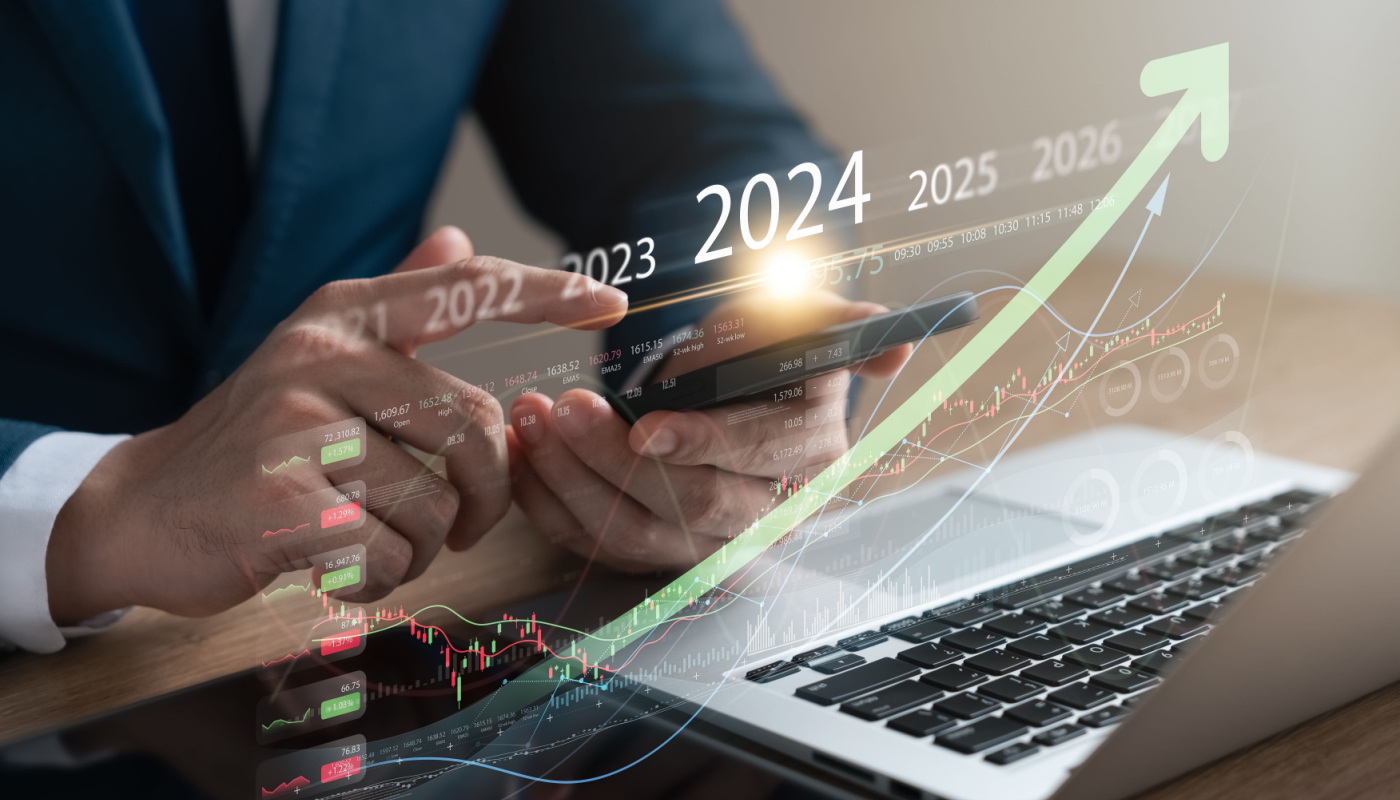
Unpacking S&P Global’s 2024 Supply Chain Industry Outlook
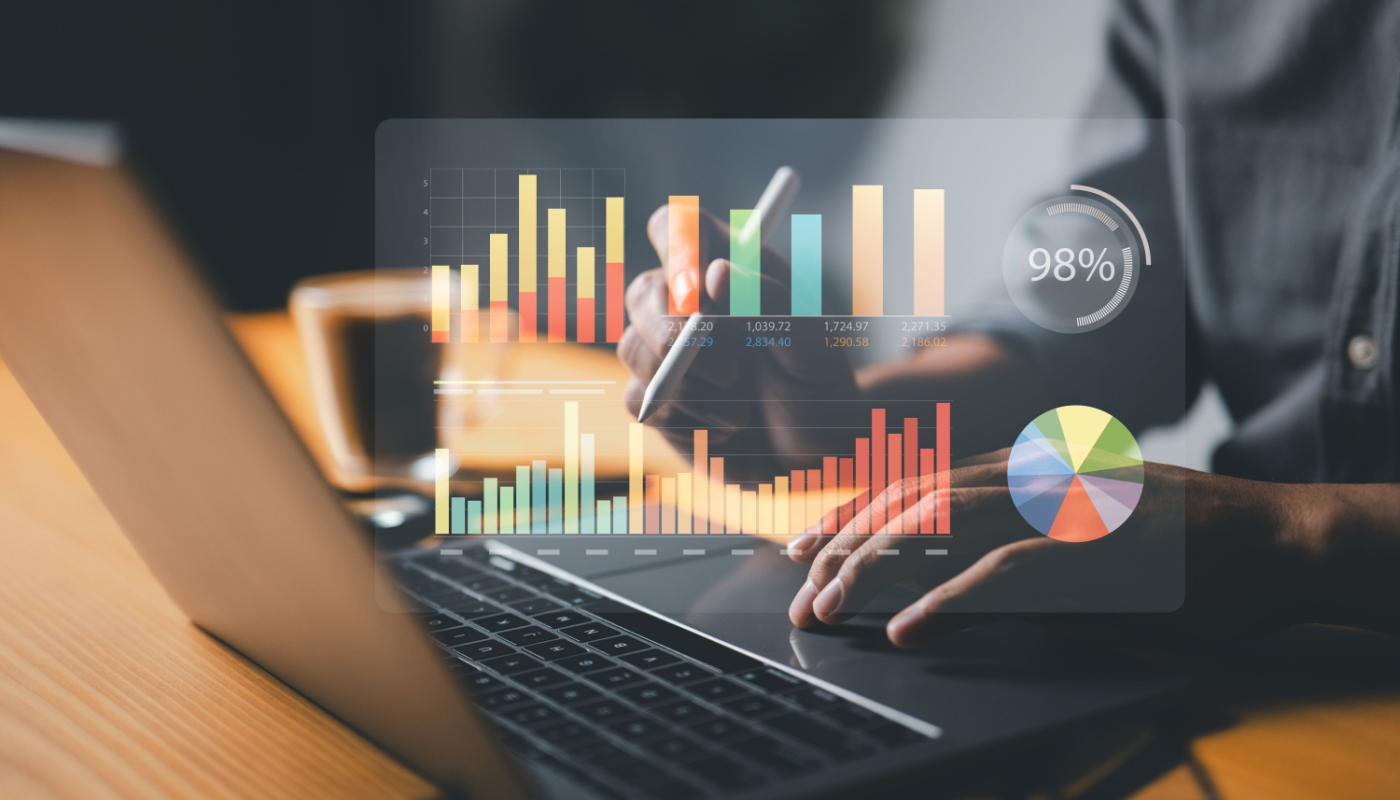
How to Improve Forecast Accuracy
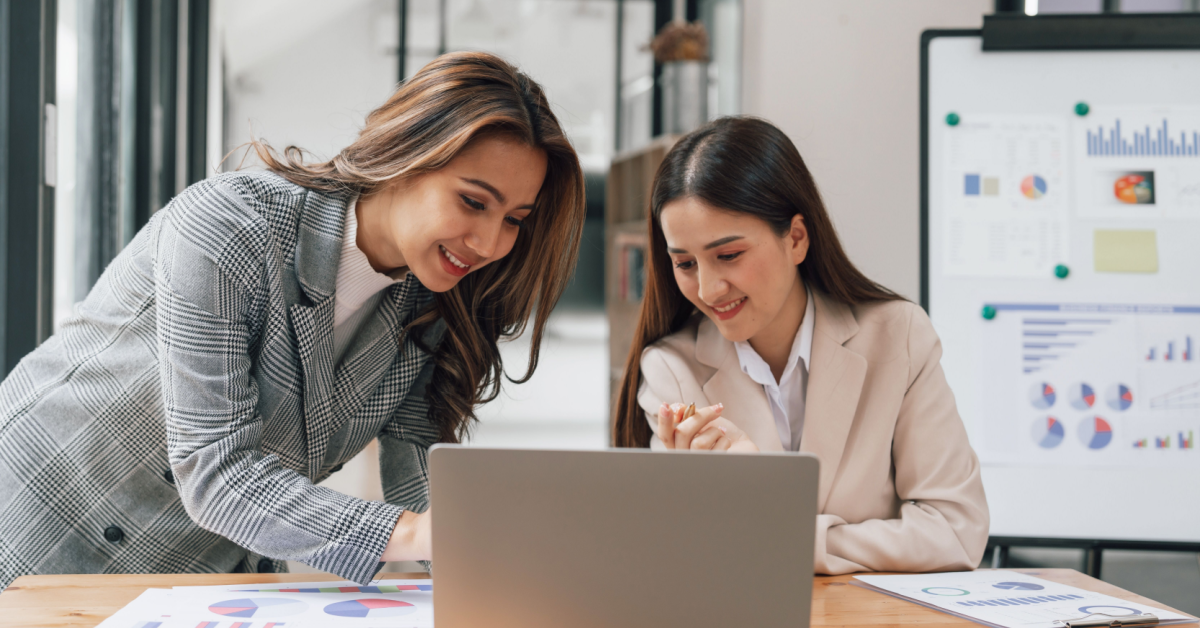
A Journey Through Safety Stock, Part 11
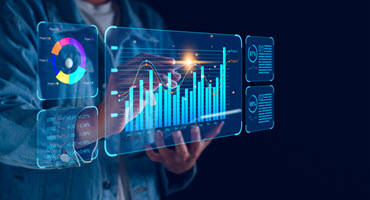
What is S&OP?
Pin it on pinterest.
Avantax Acquires Integrated Tax & Wealth Strategies’ $760 Million Wealth Management Business
DALLAS, May 01, 2024 (GLOBE NEWSWIRE) -- Avantax® Inc., a leader in tax-focused financial planning and wealth management, has acquired the wealth management business of Integrated Tax & Wealth Strategies, an independent wealth management firm that is one of the largest businesses within the Avantax Community, with $760 million in total client assets, as of Dec. 31, 2023.
Integrated Tax & Wealth Strategies’ founder – highly successful independent financial advisor Brian Stephens – will continue with the tax practice. Integrated Tax & Wealth Management’s other financial advisors and wealth management team have become W-2 investment adviser representatives of Avantax Planning Partners℠.
Stephens said conversations about further deepening his partnership with Avantax began after he watched many of his peers pursue a similar path with Avantax Planning Partners.
“I’ve seen several other advisors align with Avantax Planning Partners, and while I looked at various options even outside of Avantax, I realized that other broker-dealers don’t understand our business model where tax preparation is such a key component of the investment relationship,” Stephens said. “I feel Avantax is the right answer because they are 100% aligned with my belief that the best solution for clients is to keep investment and tax preparation tied together.”
Stephens’ wealth team, including Matt Murch, CFP®, Joseph Webster, CFP®, Sabrina Pledger, Amy Villarreal, Kyle Pledger and Cheryl Wright, have joined Avantax as employees and will continue to support the relationships the team has built over the past 25 years.
The next evolution of Stephens’ relationship with Avantax grew from a customized approach for Stephens and his team; it was designed with long-term growth potential in mind.
“For each deal, the Avantax discovery process starts with what’s most important to that business owner,” said Michael Molnar, SVP of Corporate Development, M&A and Succession Planning at Avantax. “Brian outlined how he wanted his clients to be served, the growth opportunities he hoped to create for his team and partners, and what he wanted his next several years to look like. We successfully structured the deal to meet Brian’s goals while setting the stage for the next phase of growth.”
In welcoming Stephens and his team to the new relationship, Todd Mackay, President, Avantax Wealth Management, said: “Brian’s ability to expand his business, create growth opportunities for his team, and provide excellent service to his clients is exemplary. This new relationship between Brian and Avantax is a natural fit. We are eager to see Brian and his team continue growing the integrated tax and wealth management business with Avantax as we focus on further strengthening their already powerful client relationships.”
Tax and financial professionals can learn more about Avantax by clicking here.
About Avantax ® Avantax, Inc. (Avantax), a unique community within Cetera Holdings, delivers tax-intelligent wealth management solutions for financial professionals, tax professionals and CPA firms, supporting its goal of minimizing clients’ tax burdens through comprehensive tax-intelligent financial planning. Avantax has two distinct, but related, models within its business: the independent Financial Professional model and the employee-based model. Avantax refers to its independent Financial Professional model as Avantax Wealth Management ® . Avantax Wealth Management (AWM) works with a nationwide network of Financial Professionals operating as independent contractors and offers its services through its registered broker-dealer, Avantax Investment Services, Inc., Member FINRA, SIPC, registered investment advisor (RIA), Avantax Advisory Services, Inc., and insurance agency subsidiaries. We refer to our employee-based model as Avantax Planning Partners℠. Avantax Planning Partners offers services through its RIA, insurance agency, and affiliated broker-dealer, Avantax Investment Services, Inc., and partners with CPA firms to provide their consumer and small-business clients with holistic financial planning and advisory services. Collectively, Avantax had $92.8 billion in total client assets as of Dec. 31, 2023. For additional information, please visit www.avantax.com.
Media Contacts: Tony Katsulos Avantax, Inc. (972) 870-6654 [email protected]
Alexandra Lynn StreetCred PR for Avantax, Inc. 929-317-4240 [email protected] [email protected]

Avantax Acquires Integrated Tax & Wealth Strategies’ $760 Million Wealth Management Business
DALLAS, May 01, 2024 (GLOBE NEWSWIRE) — Avantax® Inc., a leader in tax-focused financial planning and wealth management, has acquired the wealth management business of Integrated Tax & Wealth Strategies, an independent wealth management firm that is one of the largest businesses within the Avantax Community, with $760 million in total client assets, as of Dec. 31, 2023.
Integrated Tax & Wealth Strategies’ founder – highly successful independent financial advisor Brian Stephens – will continue with the tax practice. Integrated Tax & Wealth Management’s other financial advisors and wealth management team have become W-2 investment adviser representatives of Avantax Planning Partners℠.
Stephens said conversations about further deepening his partnership with Avantax began after he watched many of his peers pursue a similar path with Avantax Planning Partners.
“I’ve seen several other advisors align with Avantax Planning Partners, and while I looked at various options even outside of Avantax, I realized that other broker-dealers don’t understand our business model where tax preparation is such a key component of the investment relationship,” Stephens said. “I feel Avantax is the right answer because they are 100% aligned with my belief that the best solution for clients is to keep investment and tax preparation tied together.”
Stephens’ wealth team, including Matt Murch, CFP®, Joseph Webster, CFP®, Sabrina Pledger, Amy Villarreal, Kyle Pledger and Cheryl Wright, have joined Avantax as employees and will continue to support the relationships the team has built over the past 25 years.
The next evolution of Stephens’ relationship with Avantax grew from a customized approach for Stephens and his team; it was designed with long-term growth potential in mind.
“For each deal, the Avantax discovery process starts with what’s most important to that business owner,” said Michael Molnar, SVP of Corporate Development, M&A and Succession Planning at Avantax. “Brian outlined how he wanted his clients to be served, the growth opportunities he hoped to create for his team and partners, and what he wanted his next several years to look like. We successfully structured the deal to meet Brian’s goals while setting the stage for the next phase of growth.”
In welcoming Stephens and his team to the new relationship, Todd Mackay, President, Avantax Wealth Management, said: “Brian’s ability to expand his business, create growth opportunities for his team, and provide excellent service to his clients is exemplary. This new relationship between Brian and Avantax is a natural fit. We are eager to see Brian and his team continue growing the integrated tax and wealth management business with Avantax as we focus on further strengthening their already powerful client relationships.”
Tax and financial professionals can learn more about Avantax by clicking here.
About Avantax ®
Avantax, Inc. (Avantax), a unique community within Cetera Holdings, delivers tax-intelligent wealth management solutions for financial professionals, tax professionals and CPA firms, supporting its goal of minimizing clients’ tax burdens through comprehensive tax-intelligent financial planning. Avantax has two distinct, but related, models within its business: the independent Financial Professional model and the employee-based model. Avantax refers to its independent Financial Professional model as Avantax Wealth Management®. Avantax Wealth Management (AWM) works with a nationwide network of Financial Professionals operating as independent contractors and offers its services through its registered broker-dealer, Avantax Investment Services, Inc., Member FINRA, SIPC, registered investment advisor (RIA), Avantax Advisory Services, Inc., and insurance agency subsidiaries. We refer to our employee-based model as Avantax Planning Partners℠. Avantax Planning Partners offers services through its RIA, insurance agency, and affiliated broker-dealer, Avantax Investment Services, Inc., and partners with CPA firms to provide their consumer and small-business clients with holistic financial planning and advisory services. Collectively, Avantax had $92.8 billion in total client assets as of Dec. 31, 2023. For additional information, please visit www.avantax.com.
Media Contacts:
Tony Katsulos
Avantax, Inc.
(972) 870-6654
Alexandra Lynn
StreetCred PR for Avantax, Inc.
929-317-4240

- Review of Books
- Agriculture
- Manufacturing
- Energy Policy
- Well-connected Deer Industry Tackling Integrated Farm Planning
Press Release – Deer Industry NZ
Making things simpler, not harder, for deer farmers in farm planning and coping with regulations is Deer Industry NZ (DINZ) industry capability manager John Ladleys current focus. With markets demanding higher environmental and societal standards …
Making things simpler, not harder, for deer farmers in farm planning and coping with regulations is Deer Industry NZ (DINZ) industry capability manager John Ladley’s current focus.
With markets demanding higher environmental and societal standards from the products deer farmers are supplying, the deer industry is organised and DINZ is dead set on supporting producers navigate the thicket of planning systems and services to come out the other side with an integrated farm plan (IFP), he explains.
The main fuel for this deer industry initiative, “Engaged Farmers to Succeed”, is its $700,000 share of the $37 million the Government budgeted for a national integrated farm planning system for farmers and growers. The programme is funded through to 2026 and is administered through the Ministry for Primary Industries (MPI).
The IFP programme aims to help up to 40,000 farmers and growers nationwide through a broader approach to integrated farm planning that cuts out duplication, identifies improvements, helps achievement of business goals and promotes better information sharing. MPI kicked things off by creating planning templates covering a basic farm plan, people, biosecurity, animal welfare, emissions, biodiversity and intensive winter grazing.
Ladley says that for IFP to work, deer farmers need to understand the benefits of the process and how it could improve returns. “They aren’t interested in yet another cost of doing business.”
He says the landscape of farm planning support for farmers is very cluttered at the moment and has been skewed towards responding to regulation.
“IFP is much broader ranging. In fact, when done properly, it can act as a template for someone taking over a farm business from scratch.”
Ladley doesn’t want to add to the clutter and current uncertainty about the direction of regulatory change, but rather he’d like deer farmers to be able to leverage the work that’s currently being done.
“Some of the meat processors also have teams helping their suppliers with the NZ Farm Assurance programmes, NZFAP and NZFAP Plus; there are other commercial entities offering similar services and of course there are farmer- or community-led initiatives like catchment groups. They are all doing good work in this space.”
For these reasons the deer industry team is taking a cautious approach to building trust among farmers that there will be a better way to build a solid planning framework around their business.
“We’re still at the start of that process, doing some monitoring and evaluation to get better insights. We need to identify where people are on that farm planning bell curve. That will drive what we do.”
Around 300 deer farmers are signed up to NZFAP, according to DINZ, with around 30 accredited to NZFAP Plus, “and many more in the process of signing up,” notes Ladley.
Ladley suspects that those who are “ahead of the curve” will find that they have already done a lot of the work for IFP.
A big advantage for the deer industry is that it is very strongly connected through an active Deer Farmers’ Association and also through the networks that were built through the seven-year Passion2Profit (P2P) programme, which ran until 2022. “Nineteen of the P2P Advance Parties, representing nearly 200 deer farmers, will be taking on the IFP programme, plus three of the P2P Environment Groups.”
Avoiding duplication or reinventing the wheel with farm planning is a priority for Ladley and he’s familiar with NZ Farm Assurance Programmes which are a very good framework for an IFP. They are not mutually exclusive, he says, and are in fact useful building blocks.
“We’ll be taking a modular approach, helping deer farmers build an IFP based on what they’ve already done, and taking on the work in bite-sized chunks.
“A lot of our effort will be in connecting farmers with the products and services that will help them get there. But their existing connections with each other and the deer industry’s strong collegiality will also be a real asset.”
Content Sourced from scoop.co.nz Original url
Kommentare sind geschlossen.
Latest Business news
- Prime Minister’s Science Prizes Announced
- Air New Zealand Announces Changes To Sustainability Advisory Panel
- If Not Journalists, Then Who?
- European Free Trade Agreement A Game-changer For Canterbury
- Flood Resilience PhD Student Widi Auliagisni Named Future Thinker Of The Year 2024
- NZ-EU Free Trade Agreement Brings Immediate Gains
- Draft Design Recommendations On A Green Taxonomy For Aotearoa NZ Released For Public Feedback: Deadline Approaching
- Toast To Trio Named For First Great Wine Capitals Knowledge Exchange!
- Urgent Call For Revised Driving Licence Procedures For Seniors
- Decision To Abandon Regulation Of Residential Property Managers A Setback For The Whole Industry
- One Week To NZ’s Biggest Tourism Showcase
- Accelerating Airport Security Lines
- Bragato Research Institute Appoints New CEO
- Healthcare Organisations Lose 20% Of Their Sensitive Data In Every Ransomware Attack, Reports Rubrik Zero Labs
Recent Comments
- Lan: Unbelievable that a WEST AUSTR...
- jackp: Murray, when Key is involved t...
- Murray Guy: There are no boundaries when i...
- Lan: Canada & EU do it..Bryce ...
- Lan: I read somewhere that they do ...
- Simon Johnson: The former Department of Labou...
- Andrew P Nichols: Long overdue. Nowhere else in ...
- Rafi: I look forward to Mr Lees-Gall...
- Kevin McMahon: Yes, good on Lord Monckton. ...
- Bee: How do you think Kim Jon Key m...
Recently on Scoop
- Business Reports
- China Economic Scan
- Compare house prices
- Deposit Rates
- Direct Broking – NZX & ASX Trading & Prices
- Findata – Market Data
- Good Returns
- Herald Business
- Interest.co.nz – Interest Rates News & Views
- National Business Review
- Property Talk
- Stuff Business
- Value Cruncher – NZX

IMAGES
VIDEO
COMMENTS
Integrated business planning framework. Integrated Business Planning (IBP) is a holistic approach that integrates strategic planning, operational planning, and financial planning within an organization. IBP brings together various functions, including sales, marketing, finance, supply chain, human resources, IT and beyond to collaborate across ...
Integrated Business Planning Explained. Many organizations mistake IBP for a supply-chain-centric exercise. While linking supply chain planning with other departments, from sales and operations through finance, is important, that's just one element. ... Integrated business planning takes place at a regular cadence; every month is most common ...
A typical IBP process involves several stages: Data Collection and Analysis: Gathering relevant data (e.g., sales forecasts, production capacities, inventory levels and financial projections) from different departments. Demand Planning: Predicting future demand based on historical data, market trends, customer feedback and sales forecasts ...
One global manufacturer set up its integrated business planning (IBP) system as the sole way it ran its entire business, creating a standardized, integrated process for strategic, tactical, and operational planning. Although the company had previously had a sales and operations planning (S&OP) process, it had been owned and led solely by the supply chain function.
Integrated business planning (IBP) is a process for translating desired business outcomes into financial and operational resource requirements, with the overarching objective of maximizing profit and / or cash flow, while cutting down risk. The business outcomes, on which IBP processes focus, can be expressed in terms of the achievement of the ...
3:57. Integrated Business Planning is a best-practice process that aligns Commercial, Financial and Supply Chain activities. In doing so, they are performed as coordinated business decisions with the intent to deliver increased revenue, improved service levels, reduced supply chain costs, greater productivity, better cash flow and higher profits.
What is Integrated Business Planning (IBP) Integrated business planning — the subject of a new report from the Association for Finance Professionals (AFP) — is a single holistic plan that seamlessly connects strategic plans with sales plans, operational plans, and financial plans while balancing practical constraints about the availability ...
Intelligent Modeling as a Requirement for Successful IBP. Successful Integrated Business Planning includes unique technology capabilities. Below are the most important ones: An underlying holistic model that represents the business as it behaves in reality, including business, financial, and supply chain constraints.
Integrated usiness lanning plus our journey towards digital end-to-end planning. 05. Market Ambiguity. • Due to strong connections between companies worldwide, international political uncertainties, like the Brexit, influence most companies • Traditional business models are challenged by disruptive ideas like 3D printing. Digitalization.
Integrated business planning is a process that continuously aligns targets, assumptions, and plans across all key players in a company to assure more reliable achievement of business plans and brand objectives. In plain English, it's a way to get everyone on the same page, fast, and execute. IBP emerged in the early 2000s because of a very ...
Integrated Business Planning (IBP) is the business planning process that extends the principles of Sales and Operations Planning (S&OP) throughout the value chain. It is to create a bridge between strategy and execution. IBP is a next step for companies that already have an S&OP process in place. It is a next step because it integrates the ...
Integrated FP&A. Planning and Budgeting. Risk-Adjusted Planning. Extended Planning & Analysis (xP&A) Integrated Business Planning (IBP) is often seen as a natural progression from Sales and Operations Planning (S&OP), which came to life in the 80's to align sales and operations. As S&OP found its origin in the supply chain, IBP is often ...
Integrated Business Planning (IBP) is more of a philosophy than a rigorously deined academic term; it is the gathering of all aspects of business planning so they can be viewed, understood, and acted upon in a seamless process. Breaking down the term helps us understand the goals of this paper:
Allowing for better decision making. An integrated business process enhances a company's ability to evaluate data, the relevant context, and the big picture at the same time. By analyzing the results, they can make highly informed decisions based on the information they are presented with. These benefits are desirable for any organization ...
What Is Integrated Business Planning (IBP)? The term today is highly debated between two groups of practitioners: one defines it as the planning process that includes demand review, supply review, product management review, management business review, financial reconciliation, and business strategy. Some view IBP as a broader version of S&OP ...
Project managers must first conduct CBAs to ensure that the estimated costs and benefits line with the company's aims. Using hit-and-miss strategies reduces overall business efficiency and boosts chances of success. 3. Ensure IBP Process Is On Track. A strategically aligned IBP process can transform a firm.
Integrated Business Planning (IBP) is a strategic approach that unites all the functional areas of a business to achieve a common set of goals. It is a holistic method that aligns strategic, operational, and financial planning to enhance business performance. In the context of small businesses in Australia, IBP is a critical tool that can help ...
Integrated Business Planning Explained Many organisations mistake IBP for a supply-chain-centric exercise. While linking supply chain planning with other departments, from sales and operations through finance, is important, that's just one element.
Integrated Financial Planning (IFP) and Integrated Business Planning (IBP) mean different things to different people. Primarily because there is no universal definition of what "fully integrated" processes entail. ... They are explained below and form the framework for the maturity model shown in exhibit 4. Resource Quantification: Quickly ...
The Progression from Traditional S&OP to a Strategic IBP Process. Evolving traditional Sales and Operations Planning (S&OP) to a more strategic Integrated Business Planning (IBP) process has become critical to thrive in an increasingly complex and volatile global market. The shift from S&OP to IBP is not merely a change in terminology; it ...
SAP Integrated Business Planning Explained (SAP IBP) SAP Integrated Business Planning (IBP) is a Cloud Based solution for supply chain planning designed to help companies streamline and enhance their planning processes. IBP provides a single platform for collaboration and data-driven decision-making, enabling companies to better respond to ...
Integrated Business Planning, as a general term within Supply Chain Management, refers to macro processes such as Demand Planning, Inventory Planning and Optimization, Supply Planning, and Exception Management. This course connects a professional user experience with these as explained unit by unit as follows:
IBP typically involves a wider range of stakeholders, including executives, functional leaders, and external partners. S&OP is more focused on the sales and operations teams. Additionally, the ownership of the IBP process tends to be in the "corner office". For S&OP, the ownership is usually at the manager/functional owner level.
Integrated Tax & Wealth Management's other financial advisors and wealth management team have become W-2 investment adviser representatives of Avantax Planning Partners℠.
DALLAS, May 01, 2024 (GLOBE NEWSWIRE) — Avantax® Inc., a leader in tax-focused financial planning and wealth management, has acquired the wealth management business of Integrated Tax & Wealth Strategies, an independent wealth management firm that is one of the largest businesses within the Avantax Community, with $760 million in total client assets, as of Dec. 31, 2023.
DALLAS, May 01, 2024 (GLOBE NEWSWIRE) -- Avantax® Inc., a leader in tax-focused financial planning and wealth management, has acquired the wealth management business of Integrated Tax & Wealth ...
The IFP programme aims to help up to 40,000 farmers and growers nationwide through a broader approach to integrated farm planning that cuts out duplication, identifies improvements, helps achievement of business goals and promotes better information sharing. ... team is taking a cautious approach to building trust among farmers that there will ...